Front axle
Parts
![]() |
![]() |
Steering-related parts (e.g., tie rod) are described in steering linkage page.
Common issues with the front axle/suspension are:
- Front tyre/s wearing unevenly.
- Front suspension making a creaking sound at low speed indicating possible ball joint failure.
- Looseness indicated by excess movement in ball joint/s. I.e., it feels worn and not firm in its socket.
- Cracks in the control arm (Item 85) bushings and ball joints.
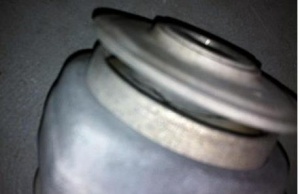
If you experience any of the above issues, the following parts are the ones that often need replacing due to wear after about 130,000 Km (80,000 miles).
- The front rear lower control arms (shock mount control arms) are not a "must replace" item. If your car has higher miles (80k+), then it would be a good idea to replace them as well. The outer end of the arm can be quite tricky to force off the ball joint at the knuckle (spindle).
- The thrust arms (torque arms) wear out faster, as they take the brunt force of the vehicle under braking. Once you pull out the thrust arms, take a look at the chassis side joint. If the rubber has clearly failed (lots of cracks), then it may be a good idea to change the shock control arms as well.
Tips for DIY repairs
- Make absolutely certain that the car is properly and safely supported. You will be pulling and pushing hard on the car while you are under it.
- It might be helpful to kept all new parts in the freezer for a few days to shrink them before assembly because the fit tolerances are so tight. Remove each part from the freezer until just prior to installing the part.
- Make sure to soak all the bolt/nuts a few hours before you start work with PB blaster or Penetrene.
- In hindsight, it is useful to replaced both the strut (also called Thrust Arm or Torque Strut) and control arms (upper control arm and lower control arm) at the same time because they have similar bushings that undergo the same service environment. Additionally, if doing both control arms, for easier access to a ball joint and ease reinstallation it is helpful to completely remove the Steering Knuckle (also called spindle or hub).
- Take your time disconnecting and reconnecting any of the electrical connectors in the area - its easy to mess these up. Use some masking tape to mark the connections.
- Once the car is jacked up and the wheels removed, release the air pressure on the top of the shock. With the key off, and the vehicle raised up, crack open the fitting at the top of the airmatic strut. Be careful not to allow any dirt in the system. Once everything is connected back up it will just fill back up once the car is turned on.
- When using the Ball Joint Separator tool (and you have a lot of free time), tighten it, walk away. Come back a few hours later, tighten it a little more and walkway. Repeat the steps. The ball joint normally breaks loose due to tension. If you are lucky it will let go after about 30-40 minutes.
- Use a hot air dryer on each stuck nut for about five mins each and they come out easy, the heat breaks down the lock-tight bond.
- The 5mm Alan has blue Loctite from the factory and normally requires an impact grade driver to remove. If you end up rounding the Alan out, (which can easily happen) then the drill must come out and carefully drill out the set screw. Here's how to remove them using a a miniature butane torch [1]
- Good website for more tips on how to get set screws out and ball joints separated. [2]
- If you are doing this DIY with a jack and stands the easiest way is to remove the Steering Knuckle (also called spindle or hub) with the arms attached after removing the brake caliper. Just remove the tie rod end from the knuckle then disconnect the strut from the control arm, followed by releasing the upper control arm from the knuckle then control arms from the chassis. This way it is a lot easier to remove the arms from the knuckle on a work-bench.
- Removing the Steering Knuckle (also called spindle or hub) as a first step really frees up the area for further work. Please note that it is essential to use a 5mm hex key to hold the center stud from turning when removing the 21mm nut at the wheel hub. A long handled key with a Blackhawk brand 21mm ratcheting closed end wrench is useful.
- After strut replacement the correct procedure is to do a ride height adjustment using M-B's Star Diagnosis System (SDS) and then a four wheel alignment, failure to do so will result in bad tyre wear. (not verified)
- As long as you do not extend or shorten the Tie-Rod, from the inner tie rod, after it is disconnected from the steering knuckle, there is no need for alignment. So, leave the Tie-rod alone after you separate it from the knuckle.
- When you are done with repair, put the wheels on and carefully lower the vehicle back down with the weight of the car resting on the suspension. THEN, tighten the airmatic fittings and turn the car on. The vehicle should return back to its normal height. Only tighten the lower control arm bolt to the vehicle fitting with the vehicle weight fully on the wheels (or lower the car onto car ramps), as this will prevent the rubber from being torqued and tearing in the lower control arm.
Special Tools Required
How to Replace Front Lower Control Arm Bushings
http://www.benzworld.org/forums/w220-s-class/1810897-02-s500-lower-control-arm-bushings.html
Fitted Bolt
The Transverse Control Arm and Thrust Arm uses standard bolt A2203330071 fitted at factory. After an accident or through years of heavy use the chassis of the vehicle deforms which causes problems for suspension geometry adjustment. For more flexible suspension adjustment a fitted bolt A2203330171 can be installed. See wheel alignment.
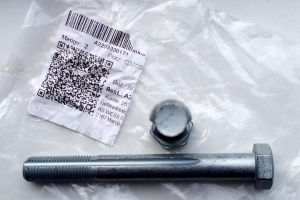
Replace supporting joint
|
![]() |
- Remove steering knuckle (5)
- Check supporting joint (7)
- Press supporting joint (7) out of steering knuckle (5)
- Install in the reverse order
The joint can be pressed out without completely removing the steering knuckle (only by disconnecting the upper control arm), but it is much more convenient to do it on a removed steering knuckle.
This video shows in detail how to replace the Ball Joint outside of the car (with the steering knuckle removed from the car):
![]() |
http://www.benzworld.org/forums/w220-s-class/1519699-w220-ball-joint-replacement-diy-tutorial.html
Remove/install torque strut at front axle
|
![]() |
- Lift vehicle on lifting platform.
- Remove front wheel
- Press radius rod (18) out of steering knuckle. Installation: Replace self-locking nut (18b).
- Detach front engine compartment paneling from the inner paneling of the fender
- Swing back the inner paneling of the fender
- Unscrew nut (18c), pull out bolt (18a) and remove strut rod (18) from front axle carrier.
- If repair kit installed: The bolt (18a) may not be twisted. Always counterhold bolt (18a) when loosening or tightening nut (18c), otherwise the lock tabs for caster adjustment in the rubber mount (18d) will be sheared off.
- Installation: Screw on nut (18c) of bolt (18a) until it abuts, however do not tighten yet so that the rubber mount (18d) of the strut rod (18) can twist when the vehicle is rocked to settle the suspension. Tighten nut (18c) with the vehicle in curb position.
- Check rubber boot on ball joint of torque strut (18) for damage. If damaged the strut rod (18) should be replaced.
- Check rubber mount (18d) of torque strut (18) for damage. If damaged the strut rod (18) should be replaced.
- Install in the reverse order. Installation: Only tighten nuts (18b, 18c) in the ready-to-drive condition.
Torque specifications:
- Self-locking nut, torque strut to front axle carrier: Stage 1: Nm 80, Stage 2: Angle 120.
- Self-locking nut, radius rod to steering knuckle: Stage 1: Nm 50, Stage 2: Angle 60.
Remove/install spring control arm on front axle
|
![]() |
Shown on spring control arm without thrust plates:
|
![]() |
Remove/install:
- Raise vehicle with vehicle lift
- Remove front wheel
- Detach torque strut (18) from steering knuckle (5). Installation: Install new nut (18b). Check rubber boot on ball head of torque strut (18) for damage. If rubber boot is damaged, install new torque strut (18). Alternatively, it might be easier to detach upper control arm from steering knuckle.
- Vehicles with AIRmatic (semi-active air suspension), code 489: Unscrew nut (23c) and pry link rod (23) off spring control arm (17). Installation: Press link rod (23) onto hexagon of stabilizer bar pivot bushing at spring control arm (17). Check rubber boot of stabilizer bar pivot bushing of link rod (23) at spring control arm (17) for damage, install new stabilizer bar pivot bushing if necessary.
- Remove bolts (40c) from spring strut (40). Installation: After tightening the bolts (40c) must be flush with the suspension strut (40) or slightly recessed.
- Using a suitable lever, loosen spring strut (40) at ball joint. Check rubber boot of ball joint for damage and install new spring control arm (17) if necessary.
- Press spring control arm (17) out of steering knuckle (5). Installation: Replace self-locking nut (17b).
- Vehicles with Active Body Control (ABC) (option code 487 - ABC SUSPENSION (ACTIVE BODY CONTROL)), when removing right spring control arm (17). Remove the pressure-supply circuit's valve body from the right side of the front subframe and tie it to one side.
- Remove spring control arm (17) from front subframe. Do not twist bolt (17a). Always counter the bolt (17a) when slackening the nut (17c), otherwise the locating tabs for camber adjustment in the rubber bushing of spring control arm (17) will be sheared off. Installation: Screw nut (17c) all the way onto bolt (17a) but do not tighten, so that the rubber bushing of spring control arm (17) can turn when the suspension is compressed. Do not tighten nut (17c) until in ready-to-drive condition.
- Install in the reverse order
- Perform wheel alignment check
Torque specifications:
- Front axle stabilizer bar, Nut, link rod to spring control arm: 150 Nm
- Suspension struts, Bolt, front suspension strut to spring control arm: 20 Nm
- Wheel location, hub: Self-locking nut, track control arm to stub axle: Stage 1: 50 Nm, Stage 2: 60°
- Wheel location, hub: Self-locking nut, spring control arm to front axle carrier: Stage 1: 80 Nm, Stage 2: 120°
Remove/install steering knuckle
|
![]() |
- Remove front wheel
- Remove brake disc
- Remove front wheel hub (actually not needed)
- Detach brake cover plate
- Detach left front rpm sensor (L6/1) from steering knuckle (5)
- Press tie rod joint (10a) out of steering knuckle (5)
- Press follower joint (8) out of steering knuckle (5)
- Press radius rod (18) out of steering knuckle (5). Do not detach torque strut (18) from the front axle carrier.
- Press spring control arm (17) out of steering knuckle (5). Do not detach spring control arm (17) from the front axle carrier.
- Check supporting joint
- Install in the reverse order
- Before starting engine, actuate brake pedal several times until the pressure is built up and maintained in the brake system.
- Only tighten nuts and bolts of chassis components when vehicle is in a ready-to-drive condition.
Torque specifications:
- Self-locking nut, track control arm to stub axle: Stage 1: Nm 50, Stage 2: ° 60.
- Self-locking nut, radius rod to steering knuckle: Stage 1: Nm 50, Stage 2: ° 60.
- Self-locking nut, upper wishbone follower joint to steering knuckle: Stage 1: Nm 20, Stage 2: ° 90.
- Self-locking bolt, front axle rpm sensor to steering knuckle: Nm 25
- Self-locking nut, tie rod to steering knuckle: Stage 1: Nm 50, Stage 2: ° 60
- Bolt brake cover plate to steering knuckle / wheel carrier: M6 Nm 10
Inspect front axle joint for play, inspect rubber boots
|
![]() |
- Check rubber boot (7f) on supporting joint for leakage and condition. If the rubber boot (7f) is leaky, replace supporting ball joint (7) or lower control arm.
- Check front axle supporting joints
- Check rubber boot (18f) on ball joint of torque strut (18) for leaktightness and condition. If the rubber boot (18f) is leaky, replace strut rod (18).
- Check rubber boot on follower joint for leakage and condition. If rubber boot is leaky (e.g. grease escape) replace upper transverse control arm or upper ball joint.
- Check follower joint for play. If there is play in the upper ball joint, replace upper transverse control arm or upper ball joint.
Checking supporting joint and follower joint of steering knuckle mount (removed)
|
![]() ![]() |
- Move the ball pin in all directions with an approximately 150 mm long pipe. The ball pin should move without play (without seizing), and should not cause any creaking noise.
- Check rubber boot (7f) on supporting joint for cracks and damage. Replace supporting joint if necessary.
- Check rubber boot (8f) on follower joint for cracks and damage. If necessary, replace follower joint or upper transverse control arm. For upper transverse control arms made of die-cast aluminum the upper transverse control arms must be replaced. For upper transverse control arms made of sheet metal aluminum the follower joint must be replaced.
Checking follower joint of steering knuckle mount (installed)
|
![]() |
- Raise vehicle with lifting platform
- Check rubber boot (8f) for signs of cracks and damage and, if necessary, replace upper transverse control arm or follower joint. For upper transverse control arms made of die-cast aluminum the upper transverse control arms must be replaced. For upper transverse control arms made of sheet metal aluminum the follower joint must be replaced.
- Check play of follower joint and, if necessary, replace upper transverse control arm or follower joint. Feel the ball joint for signs of play while forcefully pushing and pulling the front wheel. For upper transverse control arms made of die-cast aluminum the upper transverse control arms must be replaced. For upper transverse control arms made of sheet metal aluminum the follower joint must be replaced.
- Check rubber boot (8f) for leaktightness and condition. If rubber boot is leaking (e.g. grease leaking out) install new upper transverse control arm (6).
Check front axle supporting joints
|
![]() ![]() |
- Check rubber boot of supporting joint (7) for cracks and damage
- Check play in supporting joint (7).
- With pit or drive-on platform with guard edge check play by moving the front wheel up and down.
- Checking by hand: Replace supporting joint if play is perceptible.
- Checking with dial indicator: Replace supporting joint if play > 0.6 mm.
- On vehicle lift check play by moving the front wheel up and down while simultaneously feeling the supporting joint (an assistant is required). Replace supporting joint if play is perceptible.
Remove/install upper control arm
- Remove front wheel
- Separate plug connection from level sensor.
- Detach link rod (arrow) from level sensor on the upper transverse control arm (6)
- Press follower joint (8) out of steering knuckle (5)
- Secure steering knuckle (5) with wire to prevent it from swinging away
- When removing the right upper transverse control arm, detach coolant expansion reservoir and put to one side. Do not detach the coolant hoses.
- Remove upper control arm (6) from frame. Installation: Do not tighten nuts until vehicle is ready to roll. Counterhold nut with suitable box wrench.
- Check follower joint
- Install in the reverse order
Torque specifications:
- Self-locking nut of upper wishbone on front end: Nm 50
- Self-locking nut, upper wishbone follower joint to steering knuckle: Stage 1: Nm 20, Stage 2: ° 90
- Nut, level sensor link rod to upper control arm: Nm 10
![]() |
![]() |
![]() |
![]() |
![]() |
Replacing bushings for upper control arm
MB is not selling bushings for upper control arm separately. However, FAG is selling bushing under a part number 829026210 (10 EUR).
Pushing out the original LEMFÖRDER bushing is quite easy as the compression range for the bushing is just a few millimeters. FAG bushing has a much larger compression range (see below).
In practice, it is unlikely that bushing replacement would be useful, because the ball joint (which cannot be replaced) usually goes out of order sooner than the rubber bushings.
![]() |
![]() |
![]() |
![]() |
![]() |
Remove/install front wheel hub
|
![]() |
- Only tighten nuts and bolts of chassis components when vehicle is in a ready-to-drive condition.
- Remove front wheel
- Remove brake disc
- Pull off hub cap (9e)
- Undo hexagon socket head screw (9i), remove clamp nut (9d) and remove outer tapered roller bearing (9m). Installation: Adjust wheel bearing play.
- Pull off front wheel hub cover (9). If the front wheel hub (9) is seized, detach AR33.20-P-0310-01A the front wheel hub (9) using a slide hammer puller (023). Installation: Coat the radial sealing ring with grease and, if necessary, pack the space between the lip and outer tapered roller bearing (9m) with grease. Push the front wheel hub (9) with inner tapered roller bearing and radial sealing ring onto the steering knuckle spindle (5a). Installation: Fill the front wheel hub (9) with grease.
Check:
- Check brake cover plate (35). Replace if necessary. Installation: When using a new brake cover plate (35), ensure that the rubber grommet that seals the wheelspeed sensor socket is pushed onto the wheelspeed sensor.
- Check steering knuckle spindle (5a) for discoloration and wear, and check bearing surface of radial sealing ring. Discoloration can be caused by the excessive heat that can result from incorrect bearing adjustment: Replace stub axle.
- Check front wheel hub (9). Check tapped holes and rotor teeth for damage, and if necessary: Install new front wheel hub (9).
- Check the lateral and radial runout of the front wheel hub (9). If permitted measurements are exceeded: Install new front wheel hub (9).
- Inspecting tapered roller bearing and bearing races. Damaged bearings cannot be replaced (actually can); if necessary: Install new front wheel hub (9).
- Install in the reverse order
- Front wheel hub flange lateral runout: mm 0.03
- Radial runout on disk wheel alignment fitting of front wheel hub: mm 0.05
Inspecting tapered roller bearing and bearing races
The tapered roller bearings and bearing races can be used again if:
- the tapered rollers and bearing races have a smooth, grey running track
- no discoloration (from severe overheating, etc.) is found.
- the roller cage and the face ends of the tapered rollers are not damaged.
- the bearing races sit tight in the wheel hub.
The tapered roller bearings and bearing races cannot be interchanged. If damage is present, a new front wheel hub must be installed. The replacement front wheel hub is supplied complete with both bearings and sealing ring.
Wheel bearings
Issues:
- Bad bearings- need replacement
- Loose bearing nut, need adjustment
- Repacking of bearings
Part numbers
- Outer wheel bearing: A0029806502
- Inner wheel bearing: A1409810305
Hub seal and ABS wheel speed slotted disc (ABS tone ring):
- A0229979747 (OE) - EUR 40
- FEBI BILSTEIN 24994 - EUR 3
Bearing kits:
- SNR R151.35 - EUR 25
- SKF VKBA3565 - EUR 23
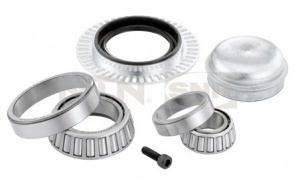
Wheel hub with bearings preinstalled:
- OE A2203300725 (308 EUR)
- FEBI BILSTEIN 30945 (100 EUR)
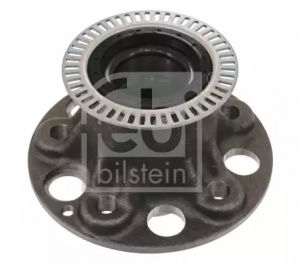
Replacing wheel bearings
- Raise car to full height.
- Chock rear wheels
- Loosen front wheel nuts.
- Jack up front of car and place on jack stands.
- Remove front wheel
- Remove brake calliper
- Support calliper to remove strain on abs wheel speed and brake wear sensor cables
- Remove Torx bolt securing brake disc to hub
- Remove brake disc.
- Remove dust cap. (For installation, fill the interior of the dust cap with high temperature wheel bearing grease. A smear of silicon will also help prevent any grease from leaking out and contaminating the wheel hub cap.)
- Undo Locking bolt on axle nut.
- Remove axle nut (For installation tighten nut and then back off to achieve 10 to 20 micrometres axial play in brake disc as measured by a magnetic base dial gauge clamped to the disc and measuring end of the axle.)
- Remove wheel hub. (If you are lucky the inner bearing and seal will come out with the hub.) (For installation ensure that there is no grease on the ABS tone ring and ensure that the hub is presented to the axle exactly square so that the inner bearing doesn’t cock on the axle shaft.)
- Clean off any remaining grease from axle.
- If necessary use and angle grinder to grind away part of the inner bearing until it is able to be split and removed from the axle.
- Do a final clean-up of the axle. (For installation, thoroughly coat the axle with high temperature wheel bearing grease before installing the hub.)
- Using a hammer and drift, knock off the ABS tone ring.
- Clean-up the wheel up of any old grease. (For installation, fill the interior of the wheel hub with high temperature wheel bearing grease.)
- Using a suitable diameter piece of bar stock, press out the outer bearing.
- Using a suitable diameter piece of bar stock, press out the inner bearing.
- Clean up the wheel hub.
- Pack the new bearings with high temperature wheel bearing grease. (An easy method is to place half a cup of grease in the corner of a plastic bag. Drop in a bearing and kneed thoroughly until the bearing is saturated with grease.)
Packing wheel bearings with grease - Install in the reverse order and repeat for the other front wheel.
When hammering in ABS Tone Ring, make sure to not bend the ring otherwise wheel speed sensor will not be able to read the rotation speed.
Bearing grease
High temperature antifriction bearing grease (NLGI grade 2). Passenger cars: Front wheel hubs
Product name (Customer, town/country):
- MB 265.1 Hochtemp-Wälzlagerfett A 002 989 00 51 (Daimler AG, Stuttgart/Germany)
- ARAL Radlagerfett (Aral Aktiengesellschaft, Hamburg, Germany)
- AVIA LITHOPLEX 2 EP (Avia Mineralöl-AG, Munich, Germany)
- Axellence 152 S Green (Axel Christiernsson International, NOL/SWEDEN)
- AXELLENCE 1525 EPS Green (Axel Christiernsson International, NOL/SWEDEN)
- Caltex Delo Grease ESI (Chevron Global Lubricants, GENT/ZWIJNAARDE, BELGIUM)
- Castrol LMX Li-Komplexfett (Castrol Limited, SWINDON, UNITED KINGDOM)
- Chevron Delo Grease ESI (Chevron Global Lubricants, GENT/ZWIJNAARDE, BELGIUM)
- Fuchs Renolit LX-PEP 2 (Fuchs Petrolub AG, Mannheim, Germany)
- Hytex EP 2 LF (Chevron Global Lubricants, GENT/ZWIJNAARDE, BELGIUM)
- KAJO-Wälzlagerfett LC 002 (Kajo-Chemie GmbH, Anröchte, Germany)
- LiLube Plus (SAF Holland GmbH, Aschaffenburg/Germany)
- MOTOREX FETT 3000 (Bucher AG Langenthal, Langenthal, Switzerland)
- RAVENOL Hot Red Grease HRG 2 (Ravensberger Schmierstoffvertrieb GmbH, Werther, Germany)
- Renolit LX-PEP 2 DC (Fuchs Petrolub AG, Mannheim, Germany)
- rhenus LKR 25 (Rhenus Lub. GmbH & Co KG, Mönchengladbach, Germany)
- Siebert high-temperature grease 5611 (Siebert GmbH, Mönchengladbach/Germany)
- Texaco Starplex EP 2 (Chevron Global Lubricants, GENT/ZWIJNAARDE, BELGIUM)
Unlisted products satisfying 265.1 specification:
- FEBI BILSTEIN 21909 (EUR 4)
- SWAG 10 92 1909
Adjust wheel bearing play
|
![]() |
![]() |
Removing:
- Remove front wheel
- Turn-in wheel bolt (48a) opposite from brake rotor attachment bolt (to immobilize brake rotor).
- Press brake pads back into brake caliper
- Pull off hub cap (9e) using removal and installation tool
Checking:
- To set up the wheel bearing loosen hexagon socket bolt (9i) and tighten clamp nut (9d) lightly whilst turning the front wheel hub.
- Mount dial indicator (022) with dial indicator holder (015) on the brake disk
- Adjust wheel bearing play by turning (arrow) the clamping nut (9d) in stages while pushing and pulling the brake disk firmly back and forth. Do not twist or tilt the wheel hub during the measurement. Correct measurement is only possible by pulling and pushing parallel to the wheel axle. Incorrect measurement will result in the set wheel bearing play being too small. This can then lead to wheel bearing damage.
- Tighten the Allen bolt (9i), check the wheel bearing end float again.
- Remove the dial indicator (022) with dial indicator holder (015).
Install:
- Fill hub cap (9e) with high-temperature roller bearing grease.
- Mount hub cover (9e)
- Remove wheel bolt (48a)
- Mount front wheel
- Wheel bearing play at front axle: mm 0.01...0.02
- Filling capacity: Hub cover: g 15, Hub (total capacity): g 95
Use of aftermarket inner wheel bearings
WARNING: Do not use aftermarket inner bearings without carefully checking that they perfectly match a genuine M-B bearing.
In particular notice the shape of the inner shoulder on the inner bearing on the side that is in contact with the axle back flange. Genuine M-B bearings have a small radiused shoulder. Some aftermarket bearings have a square shoulder. (The next diagram shows a complete but good M-B inner bearing compared with aq bad inner bearing. Only the race is shown as the bad bearing had to be destroyed by being ground with an angle grinder to produce a wafer thin section to allow it to be removed. See scorch mark where the split occurred.)
The radiused shoulder on the inner bearing fits neatly against the radiused edge on the axle flange. If an inner bearing with a square edge is used it will interfere with this radiused edge and the hub will not be in the correct position. The area of interference is shown in the next diagram.
The consequence of using an inner bearing with a square shoulder is that the wheel hub sits slightly proud by about 1mm to 2mm when installed on the axle. This also means that the clearance between the ABS tone ring and the ABS magnetic sensor is increased by the same amount and causes the speed reading sesnor to not work at all or not work properly. The magnetic sensor needs to be in very close proximity to the slotted ABS tone ring to generate adequate speed signals.
If the car is driven with this situation, after a few minutes, the instrument cluster will show ESP Failure and ABS Failure messages along with Drive to the nearest workshop being indicated.
If the gap is too wide, analysis with Star DAS will show that there is zero or an "implausible" speed signal generated by the front wheel ABS sensor.
The fix is to use genuine inner wheel bearings for the front wheels.
Wheel speed sensor
Shown on model 203
![]() |
|
The front wheelspeed sensors (L6/1 and L6/2) are mounted on the front steering knuckle assemblies. The rear wheelspeed sensors (L6/3 and L6/4) are installed on the rear wheel carriers.
It is active sensor consisting of a casing and a sensor element relying on a magnetoresistive effect to monitor rotation rate. The task of the sensor is to supply the current wheel speed to the ESP control module.
Function of the active wheel speed sensor
The diagram shows the current path through the active wheel speed sensor during an acceleration phase.
![]() |
|
The strength and direction of an external magnetic field causes a change in the internal resistance inside the sensor. An electronic analysis system accommodated in the sensor produces a square-wave signal, whose frequency is proportional to the rotational speed but whose amplitude is constant. This signal is received by the relevant dynamic handling control system and transmitted over the CAN.
A reluctor with multiple trigger points generates the external magnetic field. This consists of an elastomer plastic containing metallic particles. These are aligned by a special magnetization method so as to produce various magnets whose polarity at the circumference alternates from north to south.
Parts
- A2205400117 (OE) - left/right (~EUR 110).
- FEBI 27857 (~EUR 40)
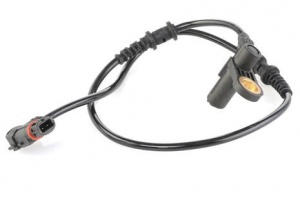
Remove/install left front or right rpm sensor
Shown on model 220
![]() |
|
![]() |
|
Remove/install:
- Remove bolt (6a).
- Take out left front rpm sensor (L6/1) or right front rpm sensor (L6/2). Installation: Apply light coating of grease to bore in steering knuckle (2). Hot lubricating paste.
- Unlock and disconnect left front axle multiple circuit junction connector, major assembly compartment (X62/7) or right front axle multiple circuit junction connector, major assembly compartment (X62/6). Press clip in direction of arrow.
- Install in the reverse order.
- Installation: Ensure that the electrical feed line to the rpm sensor has sufficient play. The vehicle suspension must be able to fully compress and rebound without damaging the feed line. The feed line should not chafe at any point, as this could lead to system failure.
- Installation: Model 230 without code (P99) Special model "AMG Black Series", observe installation position: The chafe protection (1) must be screwed to the front rpm sensor as shown here. It must not be mounted between the rpm sensor and steering knuckle (2).
- Installation: On model 215, 220 check rotor of wheel hub for damage. Pay attention to cleanliness of magnetic tip.
- Connect STAR DIAGNOSIS, read out fault memory and erase if necessary
Torque specification:
- Self-locking bolt, front axle rpm sensor to steering knuckle: 25 Nm
Front wheel speed sensor can be replaced without removing the wheel. To get access the steering wheel must be turned out as much as possible and Airmatic raised setting must set.
Remove/install left rear or right rpm sensor
Remove/install stabilizer bar on front axle
![]() |
|
- Raise vehicle with vehicle lift
- Remove bottom engine compartment paneling (vehicles with gasoline engine)
- Remove bottom section of soundproofing (vehicles with disel engine)
- Unscrew nut (23c) and pry link rod (23) off spring control arm (17). Check rubber boot of stabilizer bar pivot bushing in spring control arm (17) for damage and replace stabilizer bar pivot bushing if necessary. If the rubber boot of the stabilizer bar pivot bushing is damaged, the stabilizer bar pivot bushing (and not the spring control arm) has to be replaced. Installation: Press link rod (23) onto hexagon of stabilizer bar pivot bushing in spring control arm (17).
- Remove bolts (21e) and remove retaining bracket (21b). The threaded connection has been changed from M8 to M10. When using new parts the nut M8 possibly fitted in the frame-type integral support is to be replaced by a nut M10. Drill the hole in the frame-type integral support accordingly and protect against corrosion.
- Take off torsion bar (10). Check rubber mount of stabilizer bar (10) for damage and wear and replace stabilizer bar (10) if necessary. The rubber mounts are molded onto the torsion bar (10).
- Unscrew nut (23b) and remove link rod (23) from torsion bar (10). Installation: Tighten nut (23b) only when vehicle is in ready-to-drive condition. To do so, counterhold bolt (23d) with shortened Allen wrench (shop-made). Turn steering if necessary. Check rubber mount of link rod (23) for damage and replace link rod (23) if necessary.
- Install in the reverse order
Torque specifications:
- Nut, link rod to spring control arm: 150 Nm
- Nut, link rod to stabilizer bar: 150 Nm
- Bolt, torsion bar to front end: 40 Nm
Remove/install front stabilizer bar link rod
![]() |
Shown on left side of vehicle (W211):
|
![]() |
![]() |
![]() |
- Lift vehicle on lifting platform.
- Unscrew nut (23a) of link rod (23) from stabilizer bar pivot bushing. Do not damage rubber boot of stabilizer bar pivot bushing. If damaged, replace stabilizer bar pivot bushing. If the rubber boot of the stabilizer bar pivot bushing is damaged, the stabilizer bar pivot bushing (and not the spring control arm) has to be replaced.
- Unscrew nut (23b) of link rod (23) from stabilizer bar using box wrench bit. To do so, counterhold threaded bolt with shortened Allen hex wrench 11mm (shop-made). Turn steering if necessary. Installation: Replace self-locking nut (23b).
- Remove link rod (23) of torsion bar. This may require jacking up the spring control arm.
- Install in the reverse order
Replacing stabilizer bar bushings
Replacing bushings instead of the entire stabilizer will save ~10 EUR per stabilizer.
For pressing bushings in and out, M14 screw with appropriate caps can be used.
- For pressing out: 44/34 pressing cap; 62/52 receiving cap.
- For pressing in: 48/38 pressing cap; 62/52 receiving cap.
![]() |
![]() |
![]() |
Install new stabilizer bar pivot bushing in spring control arm
![]() |
Shown on model 220:
|
- Remove front wheel
- Detach torque strut (18) from steering knuckle (5). Installation: Replace self-locking nut. Check rubber boot on ball head of torque strut (18) for damage. If rubber boot is damaged, install new torque strut (18).
- Remove track rod (10) from steering knuckle (5). Installation: Replace self-locking nut.
- Loosen nut (23b). To do so, counterhold bolt (23d) with shortened Allen wrench (shop-made). Turn steering if necessary. Installation: Tighten nut (23b) only when vehicle is in ready-to-drive condition.
- Unscrew nut (23c), detach link rod (23) from spring control arm (17) and swing vertically upward. Installation: Press link rod (23) onto hexagon of stabilizer bar pivot bushing (8) on spring control arm (17).
- Remove rubber boot (9) and wire fasteners of torsion bar pivot bushing (8). When pressing out the torsion bar pivot bushing (8) with the rubber boot installed the special tool is damaged due to too high press-out force.
- Press stabilizer bar pivot bushing (8) out of spring control arm (17)
- Checking: Check rubber boot (19) of ball joint in spring control arm (17) for damage. If rubber boot (19) is damaged, install new spring control arm (17).
- Checking: Check rubber mount of spring control arm (17) for damage. Replace rubber mount if necessary.
- Install in the reverse order. Installation: Tighten nuts and bolts of chassis components only when vehicle is in ready-to-drive condition.
Press out/press in stabilizer bar pivot bushing
![]() |
![]() |
Pressing out:
- Do not use an impact wrench or other compressed-air tool otherwise the threaded spindle on the puller (2) will be damaged.
- The threaded spindle on puller (2) is only used for retensioning and not for pressing out the stabilizer bar pivot bushing (8).
- It is essential to remove the rubber boot (and its wire fasteners) of the torsion bar pivot bushing (8), otherwise the puller (2) will be damaged as a result of the high press-out forces.
- Press out stabilizer bar pivot bushing (8) with puller (2), press (1), press-out sleeve (2.1) and counterholder (2.3) from the spring control arm (17) opposite to the direction of travel.
- Attach the counterholder (2.3) correctly on the stabilizer bar pivot bushing (8) (see picture). The bore in the counterholder (2.3) must be seated centrally over the stabilizer bar pivot bushing (8). The removal and installation tool 220589074300 contains: Puller (2); Press-out sleeve (2.1); Counterholder (2.3).
Pressing in:
- Clean mounting hole in the spring control arm (17).
- Using puller (2), press (1), press-in sleeve (2.2) and counterholder (2.3) press stabilizer bar pivot bushing (8) into spring control arm (17) in the direction of travel.
Torque Specifications
Torque specs for a 2004 S600 (with ABC) are as follows from WIS. According to WIS, these values apply to all W220 and 215 cars with ABC. If your 2003 S600 has ABC, then it is assumed these apply. Do double check though as we will not be held liable for any damages.
- Tie rod to steering knuckle (spindle) is 50NM then 60 degrees
- Torque arm (thrust arm) to chassis 80NM then 120 degrees
- Torque arm (thrust arm) to knuckle (spindle) 50NM then 60 degrees
- Upper control arm to knuckle (spindle): 20NM then 90 degrees
- Lower control arm (aka spring control arm-front rear lower control arm that shock mounts) to knuckle (spindle) 50NM then 60 degrees
- Lower control arm (aka spring control arm-front rear lower control arm that shock mounts) to chassis 80NM then 120 degrees
NOTE: all must be torqued under load at the correct ride height (ie the vehicle on the ground). Since most don't have a four post lift, you'll need to take careful measurements, then support each corner accordingly before fully tightening. You will also need four eccentric bolts if you wish to have a proper wheel alignment done afterwards. Eccentric bolt kits are # W0133-1630584