Wheel alignment
Wheel Alignment
http://www.jltechno.com/en/alignment-data-lookup
Tutorials
DIY toe-in measurement
Trackace DIY laser wheel alignment tracking gauge (~100 EUR) is a cheap, simple and precise measurement tool to measure front wheel's toe-in/toe-out.
According to W220 specifications, the front wheels should have toe in of 0° 15'(± 10').
![]() |
![]() |
Adjust toe at the front axle (FA)
Adjust:
- Switch off easy entry/exit for driver seat and steering wheel. Otherwise the driver seat and steering wheel move into a different position if the driver door is opened or closed for example. The upper frame may be damaged when the holding device (055) is installed. Switching off takes place via the buttons on the steering wheel in the "comfort" menu of the multifunction display.
- Swivel sun visor to one side and fix steering wheel in center position using retainer (055). Carefully mount retainer (055), in order to avoid damaging the steering wheel or the headliner.
- Check center position of steering gear and steering wheel. The steering gear is centered when the marking on the cap is aligned with the mark on the control valve housing. If necessary, shift steering wheel.
- Install wheel spreader (030) at the front in the direction of travel on the inside of the wheel (in the direction of travel). The elastic bearing of the transverse control arm and steering linkage produces a correspondingly large toe value that is reduced to the correct dimension in the ready to-drive condition.
- Counterhold tie rod (10) at the hexagon and loosen jam nut (10f).
- Rotate the tie rods (10) to adjust the toe angle.
- Tighten jam nut (10f)
- Remove retainer (055).
- Remove wheel spreader (030).
- Check bellows for twisting and align if necessary.
Front axle toe check values: 0° 15'(± 10')
Torque spec:
- Lock nut, tie rod to inner tie rod: 60 Nm
![]() |
|
![]() |
Shown on model 220 without 4MATIC
|
![]() |
Shown on model 220 with 4MATIC
|
![]() |
Shown on model 220 without 4MATIC
|
Adjust toe at the front axle (FA)
Adjust:
- Install repair bolt (19c). Screw on nut (19b) until it abuts, but do not tighten yet so that the rubber mount of the torque strut (18) or spring control arm (17) can twist when the vehicle is rocked to settle the suspension.
- Recheck vehicle level at front axle after adjusting the camber and caster. The vehicle level must match the dimension established during the initial measurement.
- Tighten nut (19b). The repair bolt (19c) must not turn after fixing. When tightening the nut (19b) counterhold the repair bolt (19c) otherwise the lock tabs in the rubber mount of the torque strut (18) or spring control arm (17) will be sheared off.
Torque specification:
- Repair kit nut: 120 Nm
Install repair bolt
Spring link in mm | Camber change | Torque strut in mm | Caster change |
---|---|---|---|
+4 | -26' | ±0 | +35' |
-4 | +26' | ±0 | -35' |
Spring link in mm | Camber change | Torque strut in mm | Caster change |
---|---|---|---|
±0 | -5' | +4 | -46' |
±0 | +5' | -4 | +46' |
Spring link in mm | Camber change | Torque strut in mm | Caster change |
---|---|---|---|
+4 | -31' | +4 | -11' |
-4 | +31' | -4 | +11' |
+4 | -21' | -4 | +1°22' |
-4 | +21' | +4 | -1°22' |
1. Jack up vehicle at the front (the suspension must be fully rebounded).
2. Vehicles with ABC suspension: To remove the production bolt (19a) of the right front spring link, detach the bracket of the valve unit for pressure supply (52) from the front axle carrier.
![]() |
|
3. To adjust the camber and caster, the respective production bolt (19a) on the torque strut or spring link must be replaced with a repair bolt (19c).
![]() |
|
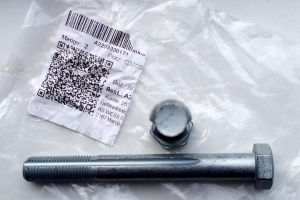