Airmatic: Difference between revisions
(information about mechanical springs) |
(→Parts: Chinese valve block - poor reliability) |
||
(91 intermediate revisions by 3 users not shown) | |||
Line 17: | Line 17: | ||
The '''EMERGENCY''' Procedure, or what to do if your car is sitting on the ground, is shown below. | The '''EMERGENCY''' Procedure, or what to do if your car is sitting on the ground, is shown below. | ||
Some of the air suspension components covered in this page are also used in W211, W216, W219, W221, W240 and W639 MB chassis vehicles. | |||
==Description== | ==Description== | ||
Line 137: | Line 139: | ||
* Locking function | * Locking function | ||
If the control module detects that all wheels are unloaded when the vehicle is stationary, the valves of the | If the control module detects that all wheels are unloaded when the vehicle is stationary, the valves of the spring struts are closed. The vehicle therefore remains at the current level. This is essential, for example, when changing a wheel or during repair work (lifting platform). | ||
'''Safety circuit''' | '''Safety circuit''' | ||
Line 160: | Line 162: | ||
In addition the system has an AIRmatic Central Reservoir (42) which stores the compressed-air. | In addition the system has an AIRmatic Central Reservoir (42) which stores the compressed-air. | ||
The AIRmatic Central Reservoir (42)pressure is between 13 and 16 bar (1,300 and 1,600 KPa or 189 and 232 psi) (at sea level). | The AIRmatic Central Reservoir (42) pressure is between 13 and 16 bar (1,300 and 1,600 KPa or 189 and 232 psi) (at sea level). | ||
The AIRmatic system is either supplied with pressure via the AIRmatic Central Reservoir (42) or via the AIRmatic Compressor Unit (A9/1). | The AIRmatic system is either supplied with pressure via the AIRmatic Central Reservoir (42) or via the AIRmatic Compressor Unit (A9/1). | ||
Line 172: | Line 174: | ||
from the air compressor is delivered to the spring struts via the | from the air compressor is delivered to the spring struts via the | ||
valve unit until the vehicle level has been adjusted. The vehicle | valve unit until the vehicle level has been adjusted. The vehicle | ||
level at the front axle is recorded by two level sensors at the | level at the front axle is recorded by two level sensors at the front | ||
axle and conveyed to the AIRmatic with ADS control module. The | axle and conveyed to the AIRmatic with ADS control module. The | ||
level at the individual spring struts is controlled by four level valves | level at the individual spring struts is controlled by four level valves | ||
Line 248: | Line 250: | ||
<!-- WIS GF32.22-P-0003-03A --> | <!-- WIS GF32.22-P-0003-03A --> | ||
[[File:W220_airmatic_location_of_electrical_electronic_components.jpg]] | {| | ||
|[[File:W220_airmatic_location_of_electrical_electronic_components.jpg]] | |||
|} | |||
===Location of electrical/electronic components=== | ===Location of electrical/electronic components=== | ||
Line 288: | Line 292: | ||
* Y53 - Left rear axle damping valve unit | * Y53 - Left rear axle damping valve unit | ||
* Y54 - Right rear axle damping valve unit | * Y54 - Right rear axle damping valve unit | ||
=== Compressor and cable related parts === | |||
[[File:W220_airmatic_compressor_and_cable_specification.png|thumb|none|Airmatic compressor and cable related parts in [[EPC]]]] | |||
=== Compressor Relay (K40/7kO) === | === Compressor Relay (K40/7kO) === | ||
Line 293: | Line 301: | ||
The relay starts and stops the Airmatic compressor. | The relay starts and stops the Airmatic compressor. | ||
A faulty relay may cause the compressor to overheat thus damaging it. | A faulty relay may cause the compressor to overheat thus damaging it. | ||
Hella relays have proven to be reliable. Part number | Hella relays have proven to be reliable. Part number 4RA 007 791-011 (A0025421319). | ||
<!-- AR32.22-P-2001I --> | <!-- AR32.22-P-2001I --> | ||
{| | {| | ||
|[[File:W220_Airmatic_Suspension_Compressor_Relay.JPG|thumb|none|Airmatic compressor relay in fuse box.]] | |[[File:W220_Airmatic_Suspension_Compressor_Relay.JPG|thumb|none|Airmatic compressor relay in fuse box.]] | ||
|[[File:W220 Airmatic Relay K40 7kO.jpg|thumb|none|Airmatic comressor relay ( | |[[File:W220 Airmatic Relay K40 7kO.jpg|thumb|none|Airmatic comressor relay (A0025421319).]] | ||
|} | |} | ||
Line 369: | Line 377: | ||
* c - Air drier | * c - Air drier | ||
* d - Outlet valve | * d - Outlet valve | ||
* | * e - Inlet valve | ||
* f - Piston | * f - Piston | ||
|} | |} | ||
Line 401: | Line 409: | ||
A new AIRmatic air filter costs around EUR 10, and it should not take more than 20 minutes to replace. For replacement method see the DIY compressor and filter replacement instructions below. | A new AIRmatic air filter costs around EUR 10, and it should not take more than 20 minutes to replace. For replacement method see the DIY compressor and filter replacement instructions below. | ||
The air filter is protected with a protective boot | The air filter is protected with a protective boot. It may be hard to separate the filter from the rubber grommet housing. The housing may fail when trying to remove it, so make sure you have a replacement housing at hand. Put a dielectric grease on the inside of the housing prior to insertion of the replacement filter to support future removal. | ||
'''Note''': The arrow on the air filter shows the 'UP' direction and not the direction of air flow which is both ways. | '''Note''': The arrow on the air filter shows the 'UP' direction and not the direction of air flow which is both ways. | ||
[[File:Airmatic Air Filter New and Old.JPG|thumb|none|Air filters (new and old).]] | [[File:Airmatic Air Filter New and Old.JPG|thumb|none|Air filters (new and old).]] | ||
{| | {| | ||
|[[File:Airmatic Air Filter 2203200069.JPG|thumb|none|Airmatic air filter ( | |[[File:Airmatic Air Filter 2203200069.JPG|thumb|none|Airmatic air filter A2203200069 (OEM MANN part: WK 32/6).]] | ||
| | | | ||
[[File:W220 AIRmatic Air Filter and Protective Boot.JPG|thumb|none|Air filter and protective boot.]] | [[File:W220 AIRmatic Air Filter and Protective Boot.JPG|thumb|none|Air filter and protective boot.]] | ||
[[File:W220 AIRmatic Air Filter Protective Boot Showing Part Number.JPG|thumb|none|Air filter protective boot (A2203280279).]] | [[File:W220 AIRmatic Air Filter Protective Boot Showing Part Number.JPG|thumb|none|Air filter protective boot ([[facelift]] A2203280279, pre-facelift A2203280179).]] | ||
|{{#ev:youtube|https://www.youtube.com/watch?v=eE9Z604KQmg|320|left|Airmatic filter replacement.|frame}} | |||
|} | |||
====Air Dryer==== | |||
Silica gel is used as a desiccant in compressor unit. It works by a process called adsorption. | |||
The water in the air actually absorbs between the tiny passages as the air passes through them. | |||
The water molecules become trapped so that the air is dried out as it passes through the filter. | |||
This process is reversible. If the silica gel desiccant is heated it will release the trapped water. | |||
This process is called regenerating the desiccant. | |||
Once saturated with water, the gel can be regenerated by heating it to 120 °C (250 °F) for 1–2 hours. | |||
However, silica gel degrades after very few cycles if heated to 110°C or more. | |||
For maximum longevity dry it at just 80°C. It won't take much longer but will last longer and work just as well as a desiccant. | |||
Once the silica gel gets saturated with water, the moisture will get in the system. | |||
Moisture will accelerate oxidation of aluminium parts (e.g., valve block). | |||
Mercedes documentation claims that desiccant used for air drying is maintenance free. | |||
However, for the longevity of our vehicles, it is recommended to change the desiccant along with the air filter at some point. | |||
There are compressor unit repair kits sold on eBay that come with new dust filters and silica gel filling. | |||
Note: The original silica gel drier beads are multi sized and a volume is calculated (gaps of air between the beads). This volume is impossible to calculate and replicate using aftermarket beads, therefore, it is recommended to dry and refit the original beads as exchanging them for new will lower the compressor flow rate (around 10-15%). | |||
<!-- http://www.benzworld.org/forums/w220-s-class/2411265-air-pump-rebuild-new-desiccant.html --> | |||
{| | |||
|[[File:W220_airmatic_compressor_unit_air_dryer_dust_filter.jpg|thumb|none|Air dryer dust filter.]] | |||
|[[File:W220_airmatic_compressor_unit_air_dryer_desiccant_silica_gel.jpg|thumb|none|Air dryer desiccant - silica gel.]] | |||
|{{#ev:youtube|https://www.youtube.com/watch?v=a3-173vjZo0|320|left|Wabco air compressor air dryer desiccant replacement.|frame}} | |||
|} | |} | ||
==== Electrical connectors ==== | |||
* Power supply - A1685453628 (from compressor relay K40/7kO) | |||
* Pressure release valve - A1685452928 (from AIRmatic control module N51) | |||
=== Level Control Valve Unit (Y36/6) === | === Level Control Valve Unit (Y36/6) === | ||
Line 418: | Line 459: | ||
The Level Control Valve Unit (Y36/6) is commonly referred to as the "valve block". | The Level Control Valve Unit (Y36/6) is commonly referred to as the "valve block". | ||
It is a common fault for the valve block to fail open. | |||
==== Parts ==== | |||
It is a common fault for the valve block to fail open. A new valve block unit (A2203200258) costs around EUR 290. | |||
In case of o-ring failure, they can be replaced (see the valve block o-ring repair kits available in the section below). | |||
Cheap Chinese clones made of plastic are available on Aliexpress, but in our experience they started to leak in less than a year of operation and the lifetime of the pressure sensor is around two years. | |||
{| | {| | ||
Line 425: | Line 470: | ||
|[[File:W220_valve_block_colored.jpg|thumb|none|Y36/6 Level control valve unit.]] | |[[File:W220_valve_block_colored.jpg|thumb|none|Y36/6 Level control valve unit.]] | ||
|[[File:W220_A2203200258_valve_block.jpg|thumb|none|Valve block (A2203200258).]] | |[[File:W220_A2203200258_valve_block.jpg|thumb|none|Valve block (A2203200258).]] | ||
|{{#ev:youtube|https://www.youtube.com/watch?v=8n5LWoqv_8M|320|left|Chinese plastic clone (60 USD on Aliexpress)|frame}} | |||
|} | |||
Miessler Automotive has created after-market valve block (EUR 200) claiming | |||
to have better quality than the original, i.e., being absolutely weatherproof without | |||
the risk of corrosion as the original. | |||
{| | |||
|[[File:W220_valve_block_Miessler.jpg|thumb|none|Miessler valve block (VENT5X22W220)]] | |||
|[[File:W220_valve_block_Miessler_back.jpg|thumb|none|Miessler valve block (back)]] | |||
|} | |} | ||
Line 445: | Line 500: | ||
* 4 - Right rear spring strut | * 4 - Right rear spring strut | ||
* 5 - AIRmatic central reservoir | * 5 - AIRmatic central reservoir | ||
* P - Air compressor | * P - Air compressor (opened or closed by pressure release valve in the compressor unit (A9/1)) | ||
|} | |} | ||
Line 452: | Line 507: | ||
|[[File:W220 AIRmatic Valve Unit Y36 6 Air Line Connection Designations.JPG|thumb|none|Line designations.]] | |[[File:W220 AIRmatic Valve Unit Y36 6 Air Line Connection Designations.JPG|thumb|none|Line designations.]] | ||
|} | |} | ||
==== Function of Level Control Valve Unit ==== | ==== Function of Level Control Valve Unit ==== | ||
Line 457: | Line 513: | ||
{| | {| | ||
|[[File:W220_level_control_valve_unit_function.png|600px | |[[File:W220_level_control_valve_unit_function.png|600px]] | ||
| | | | ||
* 40 - Front spring strut | * 40 - Front spring strut | ||
Line 535: | Line 591: | ||
metal housing (d). | metal housing (d). | ||
=== Level Sensor (B22/3, B22/8, B22/9) === | ==== Parts ==== | ||
Pressure sensor is part of the valve block, but in case of a pressure sensor failure, the pressure sensor can be unscrewed (using 27mm wrench) from the valve block and replaced separately. | |||
* OE: A2205420118 | |||
* THERMOTEC KTT130043 (20 EUR) | |||
* NRF 38953 (20 EUR) | |||
* MAXGEAR AC186345 (20 EUR) | |||
[[File:W220_airmatic_valve_block_pressure_sensor.jpg|thumb|none|Pressure sensor detached from the valve block]] | |||
=== Level Sensor (B22/3, B22/8, B22/9) === | |||
<!-- GF32.31-P-4400B Level sensor, location/task/design/function --> | <!-- GF32.31-P-4400B Level sensor, location/task/design/function --> | ||
The Level Sensor (1) function is to detect the vehicle height at the front axle and rear axle and supply the values to the AIRmatic with ADS control module. | The Level Sensor (1) function is to detect the vehicle height at the front axle and rear axle and supply the values to the AIRmatic with ADS control module. | ||
Line 568: | Line 634: | ||
|[[File:W220_repaired_link_at_rear_level_sensor.jpg|thumb|none|Repaired link for rear level sensor.]] | |[[File:W220_repaired_link_at_rear_level_sensor.jpg|thumb|none|Repaired link for rear level sensor.]] | ||
|[[File:W220_self-made_link_at_rear_level_sensor.jpg|thumb|none|Self-made link for rear level sensor.]] | |[[File:W220_self-made_link_at_rear_level_sensor.jpg|thumb|none|Self-made link for rear level sensor.]] | ||
|} | |||
Part Numbers: | |||
* Link (rod) for front left/right level sensor A2203200389 (EUR 28) | |||
* Sensor bracket front left - A2203270840 (EUR 70) | |||
* Sensor bracket front right - A2203270940 (EUR 70) | |||
{| | |||
|[[File:W220_EPC_front_axle_level_sensor.png|thumb|none|Front axle level sensor (from EPC).]] | |||
|[[File:W220_level_sensor_rod_front_A2203200389.jpg|thumb|none|Front level sensor rod left/right (A2203200389).]] | |||
|[[File:W220_front_right_level_sensor.jpg|thumb|none|Front level sensor with rod and right bracket.]] | |||
|} | |} | ||
Line 740: | Line 817: | ||
|} | |} | ||
Front struts on W220s up to about 2004 did have epoxy installed at the factory. Also many of the older style front strut have now been modified with mastic or epoxy added. Note: The epoxy is not the seal for the upper strut. It is a vibration damper to help the narrow neck of the brass valve at the top of the strut avoid cracking and leaking due to vibration. If you have a leak in this older style front strut there is a kit you can buy to fix the leak | Front struts on W220s up to about 2004 did not have epoxy installed at the factory. Also many of the older style front strut have now been modified with mastic or epoxy added. Note: The epoxy is not the seal for the upper strut. It is a vibration damper to help the narrow neck of the brass valve at the top of the strut avoid cracking and leaking due to vibration. If you have a leak in this older style front strut there is a kit you can buy to fix the leak (top seal repair kit A2203202538, see below). Scraping out the old black epoxy and filling it back in will not fix this. The part that leaks is a half metal and rubber cap under the black epoxy and is secured with a metal lock ring. The newer seals have rubber mastic compound poured in the center to seal the circumference of the upper metal cap on the upper part of the front strut and to keep the brass fitting from breaking off. | ||
{| | {| | ||
|[[File:W220_airmatic_front_strut_top_seal_leak.jpg|thumb|none|Front strut top seal leaking.]] | |||
|[[File:W220 Airmatic Front Strut Older Type.jpg|thumb|none|Oldest style front strut without epoxy.]] | |[[File:W220 Airmatic Front Strut Older Type.jpg|thumb|none|Oldest style front strut without epoxy.]] | ||
|[[File:W220 Airmatic Front Strut Newer Type.jpg|thumb|none|Newest style front strut with mastic.]] | |[[File:W220 Airmatic Front Strut Newer Type.jpg|thumb|none|Newest style front strut with mastic.]] | ||
Line 766: | Line 844: | ||
[[File:W220 AIRmatic Residual Pressure Holding Valve 01.JPG|thumb|none|Residual pressure valve.]] | [[File:W220 AIRmatic Residual Pressure Holding Valve 01.JPG|thumb|none|Residual pressure valve.]] | ||
==== Parts ==== | ==== Parts (Spring Strut) ==== | ||
[[File:W220_airmatic_spring_struct_and_mounting_front_rear.png|thumb|none|Airmatic strut (front, rear) related parts in [[EPC]]]] | |||
{| class="wikitable" | |||
! Part | |||
! Part no. | |||
! Image | |||
! Description | |||
|- | |||
|17 | |||
|A2203520027 | |||
TRW JBU167 | |||
|[[File:A2203520027_TRW_JBU167.jpg|100px]] | |||
|Supporting joint. Damper strut mounting. | |||
|- | |||
|25 | |||
|N910105014017 | |||
|[[File:N910105014017.jpg|100px]] | |||
|Hexagon head bolt. Hydropneumatic spring leg to spring control arm M14X1.5X80. | |||
|- | |||
|30 | |||
|N000000003277 | |||
|[[File:N000000003277.jpg|100px]] | |||
|Nut. Hydropneumatic spring leg to spring control arm M14X1.5. | |||
|} | |||
'''OE:''' | '''OE:''' | ||
Line 793: | Line 896: | ||
* Front: 44-042295 | * Front: 44-042295 | ||
* Rear: 44-042301 | * Rear: 44-042301 | ||
'''Miessler Automotive''' | |||
Miessler Automotive sells new struts having the same features as the OEM. | |||
* Front: FBN0-002S-4229 | |||
* Rear: FBN0-002S-4230 | |||
* Front right (4Matic): FBN0-002S-2238 | |||
* Front left (4Matic): FBN0-002S-2138 | |||
'''Arnott:''' | '''Arnott:''' | ||
Line 820: | Line 932: | ||
Note that with all new Arnott AIRmatic struts you lose the electronic damping feature. | Note that with all new Arnott AIRmatic struts you lose the electronic damping feature. | ||
While the new Arnott struts allow to plug in the original wire harness from the car, it simply fools the AIRmatic computer in to thinking the selective damping is functioning. In reality it is not and the shock has constant damping setting corresponding to OE "comfort/convenience" setting ("sport 1" and "sport 2" damping settings are not available). | While the new Arnott struts allow to plug in the original wire harness from the car, it simply fools the AIRmatic computer in to thinking the selective damping is functioning. In reality it is not and the shock has constant damping setting corresponding to OE "comfort/convenience" setting ("sport 1" and "sport 2" damping settings are not available). | ||
{| | |||
|[[File:W220_front_strut_OE_crosscut.png|thumb|none|OE front strut (crosscut).]] | |||
|[[File:W220_front_strut_Arnott_crosscut.png|thumb|none|Arnott new front strut.]] | |||
|} | |||
'''Mechanical springs:''' | '''Mechanical springs:''' | ||
Line 944: | Line 1,061: | ||
| Closed | | Closed | ||
| Closed | | Closed | ||
|} | |||
The "Actuations" menu under the AIRmatic control module in [[DAS]] can be used to force a damping setting for a particular strut regardless of the ride conditions. The "Development data" menu (in German) can be used to force damping setting for all struts (F3 - the hardest setting, F6 - the softest setting). | |||
{| | |||
|[[File:W220_DAS_actuation_of_the_right_rear_damper_valves.png|thumb|none|AIRmatic - Actuations - Damper valves - Right rear damper valves]] | |||
|[[File:W220_DAS_development_data_FN_Daempfstufe.png|thumb|none|AIRmatic - Development data - Actuations - Complete index of actuations - Dämpfstufe (FN_Daempfstufe)]] | |||
|} | |} | ||
Line 978: | Line 1,101: | ||
==Issues and Troubleshooting == | ==Issues and Troubleshooting == | ||
'''Note''': If the AIRmatic leaks substantially it is imperative that it be fixed as soon as possible or else the AIRmatic pump may burn out. If the leak cannot be fixed immediately remove the AIRmatic compressor relay (K40/7kO) to disable the AIRmatic Pump. For the relay and fuse locations see above. However '''BE WARNED''', the vehicle may leak enough to be not drivable when turning the front wheels causes them to touch the top of the wheel arch. | '''Note''': If the AIRmatic leaks substantially it is imperative that it be fixed as soon as possible or else the AIRmatic pump may burn out. If the leak cannot be fixed immediately remove the AIRmatic compressor relay (K40/7kO) to disable the AIRmatic Pump. For the relay and fuse locations see above. However '''BE WARNED''', the vehicle may leak enough to be not drivable when turning the front wheels causes them to touch the top of the wheel arch (for 18" wheels and larger). | ||
=== "AIRMATIC VISIT WORKSHOP!" message on the instrument cluster === | === "AIRMATIC VISIT WORKSHOP!" message on the instrument cluster === | ||
Line 999: | Line 1,122: | ||
|Fault in component Y53y2 (Left rear solenoid valve 2) in assembly Y53 (left rear axle damping valve unit) | |Fault in component Y53y2 (Left rear solenoid valve 2) in assembly Y53 (left rear axle damping valve unit) | ||
|See above. | |See above. | ||
|- | |||
|C1517-128 | |||
|Suspension strut is implausible. | |||
|This error code is shown when the AIRmatic system supplies or releases air from the strut, but does not observe the intended effect (likely level sensor or pressure sensor does not show the expected result). For example, it has been reported to appear in case where hoses on the valve block were mixed up. The AIRmatic system thought that it is pumping air in reservoir, but actually the air was passed to strut (and vice versa). | |||
|} | |} | ||
Line 1,084: | Line 1,211: | ||
====AIRmatic Compressor Unit Failure==== | ====AIRmatic Compressor Unit Failure==== | ||
AIRmatic Compressor Unit (A9/1) failure or partial failure. To test this hypothesis start the car and see if compressor is running (you should hear compressor in the front right fender running). | AIRmatic Compressor Unit (A9/1) failure or partial failure. To test this hypothesis start the car and see if compressor is running (you should hear compressor in the front right fender running). | ||
[[File:W220_AIRmatic_compressor_unit.jpg| | [[File:W220_AIRmatic_compressor_unit.jpg|thumb|none|Compressor Unit]] | ||
If it is not running, check AIRmatic Fuse and relay (see above). A faulty relay may cause compressor to run nonstop which will cause compressor to overheat and blow out the fuse. | If it is not running, check AIRmatic Fuse and relay (see above). A faulty relay may cause compressor to run nonstop which will cause compressor to overheat and blow out the fuse. | ||
====Pressure Lines Leaking==== | ====Pressure Lines Leaking==== | ||
The high-pressure line from the AIRmatic Compressor Unit (A9/1)to the AIRmatic Level Control Valve Unit (Y36/6) develops a leak. In this case replacement line or a repair joiner can be used. | The high-pressure line from the AIRmatic Compressor Unit (A9/1) to the AIRmatic Level Control Valve Unit (Y36/6) develops a leak. In this case replacement line or a repair joiner can be used. | ||
It is possible that the pressure line to the strut develops cracks or micro cracks. | It is possible that the pressure line to the strut develops cracks or micro cracks. | ||
Line 1,101: | Line 1,228: | ||
====Level Control Valve Unit Leaking==== | ====Level Control Valve Unit Leaking==== | ||
The AIRmatic Level Control Valve Unit (Y36/6) or '''valve block''' on top of the AIRmatic Compressor Unit (A9/1) fails (very common) and fails to close some valve. | The AIRmatic Level Control Valve Unit (Y36/6) or '''valve block''' on top of the AIRmatic Compressor Unit (A9/1) fails (very common) and fails to close some valve. | ||
[[File:W220 AIRmatic Valve Unit Y36 6 Air Line Connection Colour Codes.JPG| | |||
[[File:W220 AIRmatic Valve Unit Y36 6 Air Line Connection Colour Codes.JPG|thumb|none|Valve block]] | |||
In this case the pressure will be released back to air compressor and out of the system. | In this case the pressure will be released back to air compressor and out of the system. | ||
Line 1,131: | Line 1,259: | ||
Information reported by level sensors can be viewed using DAS. | Information reported by level sensors can be viewed using DAS. | ||
[[File:W220_Airmatic_actual_values_vehicle_level.jpg|thumb|none|DAS reading of vehicle level.]] | |||
If the vehicle rises, but then falls down again, the level sensors are likely not the cause. | If the vehicle rises, but then falls down again, the level sensors are likely not the cause. | ||
If the vehicle is low, but there is no red error message in the instrument cluster | |||
about the vehicle level being to low, the level sensor (or its linkage) is at fault. | |||
===Vehicle Level Too High=== | ===Vehicle Level Too High=== | ||
[[File:W220_Airmatic_vehicle_too_high.jpg|thumb|none|W220 with too high rear.]] | [[File:W220_Airmatic_vehicle_too_high.jpg|thumb|none|W220 with too high rear.]] | ||
====Level Control Valve Unit Leaking | ====Level Control Valve Unit Leaking==== | ||
It is possible that Level Control Valve Unit (Y36/6) fails to close some | It is possible that Level Control Valve Unit (Y36/6) fails to close some valves in which case the pressure will be released back to strut raising the car too high. | ||
The vehicle | The vehicle will be high only while the car is off, since as soon as vehicle is started the computer will try to adjust the level to the programmed level. | ||
====Compressor Unit Release Valve Stuck==== | |||
When Airmatic ECU decides to lower the vehicle, the corresponding valve in the valve block is opened to release the air out of the system. The air is released through the always-open port ''P'' on the valve block. The compressor unit has electrically operated overpressure/residual pressure valve built in the unit. If this valve is stuck, the air will not be released out of system even if ECU sends the electrical signal to release valve built in the compressor unit. | |||
The problem can be as trivial as broken connector. Usually instrument cluster will show malfunction and AIRmatic control unit will report an error: | |||
{| class="wikitable" | |||
! Error Code | |||
! Description | |||
! Probable cause | |||
|- | |||
|C1338-001 | |||
|Fault in component A9/1y1 (AIRmatic pressure release valve) | |||
|Broken connector (A1685452928) | |||
|} | |||
====Level Sensor Failure==== | ====Level Sensor Failure==== | ||
Line 1,151: | Line 1,298: | ||
===Protective Boot/Bellows Failure=== | ===Protective Boot/Bellows Failure=== | ||
On older and higher mileage vehicles the lower dust cover on an AIRmatic air suspension strut starts to wear and fail. This plastic protective boot/bellows is designed to prevent dirt and contamination getting to the air spring bag/bladder. After around 100,000 miles (130,000Kms) they often show signs of cracking and tearing. Failure to replace means the end is near for the whole strut. | On older and higher mileage vehicles the lower dust cover on an AIRmatic air suspension strut starts to wear and fail. This plastic protective boot/bellows is designed to prevent dirt and contamination getting to the air spring bag/bladder. After around 100,000 miles (130,000Kms) they often show signs of cracking and tearing. Failure to replace means the end is near for the whole strut. | ||
[[File:W220 Airmatic Lower Dust Cover Failure.jpg| | [[File:W220 Airmatic Lower Dust Cover Failure.jpg|thumb|none|Strut with failed protective dust boot.]] | ||
===Upper Mount Rubber Bush Failure=== | ===Upper Mount Rubber Bush Failure=== | ||
A bumping or knocking noise coming from the top of the front suspension may indicate a worn upper mount rubber bushing in the Air Spring. | A bumping or knocking noise coming from the top of the front suspension may indicate a worn upper mount rubber bushing in the Air Spring. | ||
When the Air Springs were manufactured the upper mount rubber bushings were installed compressed. As the mounts weaken with age they can lose their compression and cause a bumping sound. | When the Air Springs were manufactured the upper mount rubber bushings were installed compressed. As the mounts weaken with age they can lose their compression and cause a bumping sound. | ||
The | The image below shows a typical worn upper mount rubber bushing removed from an AIRmatic air suspension strut with around 80,000 to 100,000 miles (130,000KM to 161,000Km). A worn mount will also contribute to many unwanted problems with your air suspension. | ||
{| | |||
[[File:W220 AIRmatic Top Bush Comparison of New and Old.JPG|thumb|none|Top bushing: new vs old.]] | |[[File:W220 AIRmatic Front Strut Upper Mount Iso View.JPG|thumb|none|Upper mount rubber bushing of the front strut.]] | ||
[[File:W220 AirmaticUpper Mount Failure.jpg|thumb|none|Worn upper mount rubber bushing.]] | |||
|[[File:W220 AIRmatic Top Bush Comparison of New and Old.JPG|thumb|none|Top bushing: new (left) vs old (right). Note the difference in height in the side view.]] | |||
|} | |||
Note the Upper Mount Rubber Bushing can be replaced without removing the strut for the car. Do the first steps as shown in the procedure described in section "Dismantling Front Air Spring". | Note the Upper Mount Rubber Bushing can be replaced without removing the strut for the car. Do the first steps as shown in the procedure described in section "Dismantling Front Air Spring". | ||
Line 1,182: | Line 1,330: | ||
* There is a risk of damaging other strut on the same axis. | * There is a risk of damaging other strut on the same axis. | ||
There is a temporary fix for front struts, which can be used to get to the closest workshop: | There is a '''temporary''' fix for front struts, which can be used to get to the '''closest''' workshop: | ||
{| | {| | ||
|[[File:W220_airmatic_front_emegrency_fix_1.jpg|thumb|none|Step 1: Buy wooden blocks and cable ties]] | |[[File:W220_airmatic_front_emegrency_fix_1.jpg|thumb|none|Step 1: Buy wooden blocks and cable ties]] | ||
Line 1,194: | Line 1,342: | ||
The ride will be little bumpy, but not much harsher than it is when pushing the button that stiffens the suspension. | The ride will be little bumpy, but not much harsher than it is when pushing the button that stiffens the suspension. | ||
=== Original limp-home buffers === | '''WARNING:''' Travelling long distances or over excessively bumpy roads with this temporary fix using a block of wood will damage the Transverse Control Arm Top (Upper Control Arm (UCA)). | ||
[[File:W220 Front Suspension UCA Damaged After Limp Home.JPG||600px|thumb|none|UCA on left is OK, UCA on right is badly bent due to travelling over bumpy roads with an emergency block of wood holding the car up]] | |||
Note the much better location of the M-B limp-home buffer A2203271230 (1a) below which puts all the force over the ball joint and not the arm of the UCA. | |||
=== Original M-B limp-home buffers === | |||
<!-- AR32.00-P-1000I --> | <!-- AR32.00-P-1000I --> | ||
{| | {| | ||
Line 1,204: | Line 1,358: | ||
* 1a - Front axle limp-home buffers | * 1a - Front axle limp-home buffers | ||
* 6 - Upper | * 6 - Transverse Control Arm Top (Upper Control Arm (UCA)) | ||
|} | |} | ||
Line 1,219: | Line 1,373: | ||
Slowly lower vehicle and make sure that the torsion bar (77) makes contact with the | Slowly lower vehicle and make sure that the torsion bar (77) makes contact with the | ||
limp-home buffer (1b). | limp-home buffer (1b). | ||
{| | |||
|[[File:W220_airmatic_front_limp_home_buffer_A2203271230.jpg|thumb|none|Front limp-home buffer (A2203271230).]] | |||
|[[File:W220_airmatic_rear_limp_home_buffer_A2203280839.jpg|thumb|none|Rear limp-home buffer (A2203280839).]] | |||
|[[File:W220_airmatic_rear_limp_home_buffer_A2203280839_installed.jpg|thumb|none|Rear limp-home buffer (installed).]] | |||
|} | |||
==DIY tips== | ==DIY tips== | ||
Line 1,241: | Line 1,401: | ||
Before attempting any DIY repairs make sure to read the tips section above. | Before attempting any DIY repairs make sure to read the tips section above. | ||
=== | ===Testing strut for leaks=== | ||
It is common to misdiagnose leaking valve block or line to the strut with leaking strut. | |||
Before replacing the strut, the leak should be verified by directly pumping the air to the strut and observing if the strut loses the air. | |||
For this purpose a strut bypass valve below can be used. | |||
Pumping the strut requires to provide up to 10 BAR pressure. | |||
The usual Chinese 12v car tyre air compressors will fail long before that. | |||
We have achieved good success using Alca 227000 2-Cylinder 12v compressor. | |||
{| | |||
|[[File:W220_Airmatic_strut_bypass_valve.jpg|thumb|none|Strut bypass valve]] | |||
[[File:W220_airmatic_rear_strut_connect_pipe.jpg|thumb|none|Bypass valve connected]] | |||
|[[File:W220_airmatic_rear_struct_direct_pumping.jpg|thumb|none|Direct pumping into strut]] | |||
|} | |||
Parts needed: | |||
* G1/8" Schrader valve (EUR 1) | |||
* G1/8" pneumatic fitting for 2.5*4mm pipe (EUR 1) | |||
* Pipe 2.5*4mm 10m (EUR 6) | |||
* MB connector A0003270369 (EUR 4) | |||
* Compressor able to push 10 BAR at least | |||
===Inspecting AIRmatic Level Control Valve Unit (Y36/6) for leaks=== | |||
Here's how to do a general leak test which will uncover most of the problems caused by faulty valve block. | |||
On the right-hand side of the vehicle remove the wheel and part of the wheel house inner panel in front fender. | |||
<!-- http://www.nicedeals.co.uk/car/diy/8-mercedes/2509-mercedes-w220-s-class-airmatic-pump-replacement --> | |||
[[File:W220_wheel_splashguard.gif|300px]] | |||
[[File:W220_airmatic_pump.gif|300px]] | |||
# Paint or spray the pressure line connections 1, 2, 3, 4, 5, P of the level control valve with leak detecting solution. | # Paint or spray the pressure line connections 1, 2, 3, 4, 5, P of the level control valve with leak detecting solution. | ||
# Inspect for an indication of leaking. Severe leaks are evident immediately. Minor leaks can develop very slowly so be patient. | # Inspect for an indication of leaking. Severe leaks are evident immediately. Minor leaks can develop very slowly so be patient. | ||
# The leak can come also from the body of the valve block (valve block is glued together from two parts). | |||
# Wait for approx. 10-15 minutes after applying the solution and reinspect. This means that minor leaks can be recognized (forming a white cap). | # Wait for approx. 10-15 minutes after applying the solution and reinspect. This means that minor leaks can be recognized (forming a white cap). | ||
Line 1,311: | Line 1,440: | ||
|[[File:W220_Airmatic_valve_unit_testing_for_leaks_spray.jpg|300px]] | |[[File:W220_Airmatic_valve_unit_testing_for_leaks_spray.jpg|300px]] | ||
|[[File:W220_Airmatic_valve_unit_testing_for_leaks_air_compressor_line.jpg|300px]] | |[[File:W220_Airmatic_valve_unit_testing_for_leaks_air_compressor_line.jpg|300px]] | ||
|} | |||
{| | |||
|{{#ev:youtube|https://www.youtube.com/watch?v=YK0wLXm2mEc|320|left|Valve block external leak|frame}} | |||
|} | |} | ||
<!-- http://www.benzworld.org/forums/w220-s-class/2400489-airmatic-level-control-valve-question.html --> | <!-- http://www.benzworld.org/forums/w220-s-class/2400489-airmatic-level-control-valve-question.html --> | ||
Common failure mode of the level control valve unit (Y36/6) is when some valves fail to close | |||
thus releasing the air out of system through the compressor-controlled port 'P' or through other valves back to struts. | |||
To test for a leak in any valves of the valve block: | |||
# Make sure that all valves are under pressure (struts and reservoir have pressure in them). | |||
# Detach the connector of 'P' port and spray the port with leak detection spray. Alternatively the 'P' line can be disconnected at the air compressor end and immersed in a soapy solution (see below). | |||
# | |||
# | |||
# After the test use compressed air to clean the valve. | # After the test use compressed air to clean the valve. | ||
<!-- AR32.22-P-8100I --> | <!-- AR32.22-P-8100I --> | ||
Line 1,328: | Line 1,460: | ||
[[File:W220_airmatic_valve_block_test_3.jpg|200px]] | [[File:W220_airmatic_valve_block_test_3.jpg|200px]] | ||
===Leak Testing Using [[STAR Diagnosis System (SDS) or Diagnosis Assistance System (DAS)]]=== | |||
According to WIS, STAR Diagnosis System (SDS) offers an easy and thorough method for testing the AIRmatic. However, '''be warned''' that a very small leak caused by a cracked or damaged O-ring on one of the air line connectors may still pass the SDS AIRmatic Pneumatic Tests. | |||
Using SDS navigate to AIRmatic Pneumatic Tests. | |||
The following tests are available; | |||
* A9/1 Compressor Test | |||
* Y36/6y1 Left Front Strut Test | |||
* | * Y36/6y2 Right Front Strut Test | ||
* | * Y36/6y3 Left Rear Strut Test | ||
* | * Y36/6y4 Right Rear Strut Test | ||
* | * A9/1y1 Pressure Relief Valve Test | ||
* | * Leak test between compressor and valve block (line between compressor and 'P' port in valve block). | ||
* Leak test between valve block and suspension struts. | |||
* Leak test between valve block and central reservoir. | |||
** As an example this last test does the following; | |||
*** Central reservoir charge valve (in valve block) is opened. | |||
*** All other valves (in valve block) are closed. | |||
*** Compressor is turned on for <60 secs. | |||
*** Compressor is turned off. | |||
*** Compressor keeps the line to 'P' port (in valve block) closed. | |||
*** Central reservoir pressure is monitored for leakage for 120 secs. | |||
*** The Central reservoir pressure must not drop by more than 0.5 bar in that time. | |||
'''1. Leak test between compressor and valve block (line between compressor and 'P' port in valve block).''' | |||
As an example, the following result was obtained for a leak test for a '''FAULTY''' 'P' line to Level Control Valve Unit (Y36/6) or Valve Block. This is similar to the test using soapy solution. | |||
* After all valve block valves were closed the compressor produced 10.56 bar within 10 secs which is '''INSIDE''' the specification of 10 bar within 40 secs. | |||
* After the compressor was turned off the initial compressor pressure ('P' line) = 10.56 bar. | |||
* After the 120 elapsed time the final compressor pressure ('P' line) = 5.30 bar. | |||
* Thus the measured leakage rate was 5.26 bar in 120 secs which is '''OUTSIDE''' the specified 0.5 bar in 120 secs. | |||
* SDS reported that there was a leakage in the valve block or the high pressure line between the compressor and the valve block ('P' port). | |||
A squirt of some soapy solution on the high pressure line between the compressor and the valve block proved that the line and its associated connectors were not leaking. | |||
Thus the fault was a leak in the valve block. Once the 'P' port connector was removed from the valve block, a simple test by applying a soapy finger over the port produced obvious positive pressure of air escaping from the port, thus confirming the diagnosis of a leaky valve in the valve block. | |||
Unfortunately the valve block can not be dismantled for inspection and cleaning thus a new Level Control Valve Unit (Y36/6) was required. | |||
== | As a comparison, after replacing the Level Control Valve Unit (Y36/6) or Valve Block with a '''BRAND NEW''' OEM part, the following result was obtained for a leak test. | ||
* After all valve block valves were closed the compressor produced 10.8431 bar within 10 secs which is withing the specification of 10 bar within 40 secs. | |||
* After the compressor was turned off the initial compressor pressure ('P' line) = 10.8431 bar. | |||
* After the 120 elapsed time the final compressor pressure ('P' line) = 10.8431 bar. | |||
* Thus the measured leakage rate was 0.0 bar in 120 secs which is '''INSIDE''' the specified 0.5 bar in 120 secs. | |||
'''2. Leak test between valve block and central reservoir.''' | |||
As another example the following result was obtained for a leak test between valve block (Level Control Valve Unit (Y36/6)) and central reservoir for a '''FAULTY''' Level Control Valve Unit (Y36/6) or Valve Block. | |||
* | * Initial Central Reservoir pressure = 12.07 bar reached in 60 secs. | ||
* | * After Compressor turned off the Central Reservoir pressure = 10.84 bar. | ||
* | * After 120 secs elapsed time the Central Reservoir pressure = 10.57 bar. | ||
* | * Conclusion: This real world Central Reservoir and its associated supply line after 220,000Km produced a leakage rate of 0.27 bar in 120 secs, which is well within the specified 0.5 bar in 120 secs. | ||
As a comparison, after replacing the Level Control Valve Unit (Y36/6) or Valve Block with a '''BRAND NEW''' OEM part, the following result was obtained for a leak test between valve block (Level Control Valve Unit (Y36/6)) and central reservoir. | |||
* Initial Central Reservoir pressure = 7.549 bar reached in 60 secs. | |||
* After Compressor turned off the Central Reservoir pressure = 7.41177 bar. | |||
* After 120 secs elapsed time the Central Reservoir pressure = 7.41177 bar. | |||
* Conclusion: This real world Central Reservoir and its associated supply line to a brand new Level Control Valve Unit (Y36/6) or Valve Block produced a leakage rate of 0.0 bar in 120 secs, which is well within the specified 0.5 bar in 120 secs. | |||
===Replacing Compressor Unit === | |||
<!-- AR32.22-P-2001I --> | |||
{| | {| | ||
|[[File: | |[[File:W220_Airmatic_Air_Filter_Location.JPG|600px]] | ||
| | | | ||
|} | * 1 - Pressure line connection | ||
* 2 - Intake hose with air filter | |||
* 3 - Connector for air compressor motor | |||
* A9/1 - AIRmatic compressor unit | |||
* A9/1y1 - AIRmatic pressure reduction valve | |||
|} | |||
# If possible depressurise the AIRmatic system using STAR DAS. | |||
# Disconnect battery. | |||
# Remove engine compartment paneling (right front part only). | |||
# Unscrew pressure line connection (1) from AIRmatic compressor unit (A9/1). | |||
# Detach connector on AIRmatic pressure reduction valve (A9/1y1). | |||
# Disconnect connector for air compressor motor (3). | |||
# Pull intake hose with air filter (2) out of longitudinal member. | |||
# If the AIRmatic air filter (2) is replaced, '''the arrow on the air filter (2) must point upwards'''. | |||
# Unscrew nuts (arrows) and remove AIRmatic compressor unit (A9/1). | |||
# Detach air compressor relay (K40/7kO). Only when installing a new air compressor. When replacing the air compressor the air compressor relay (K40/7kO) should always be exchanged as the switching contacts may be damaged. | |||
# Install in the reverse order. | |||
{| | {| | ||
|[[File: | |[[File:W220 AIRmatic Compressor Connection Points.JPG|thumb|none|Airmatic compressor connection points.]] | ||
| | |{{#ev:youtube|https://www.youtube.com/watch?v=gkXkhy7FD8A|320|left|Airmatic compressor replacement (by Arnott).|frame}} | ||
|} | |} | ||
=== | === Compressor Unit Repair === | ||
If the compressor unit is not able to provide pressure, the most common fault is worn piston ring or cylinder head inside the air compressor. | |||
The piston ring within the compressor unit of your air suspension system deteriorates over time. | |||
The OEM piston ring is made from a soft plastic that wears quickly, this wear substantially reduces the output of your compressor leading to noisy, | |||
slow rising or non-rising suspension. There are available piston rings with improved design. | |||
Few notes to take into account: | |||
* The replacement of piston ring will not help if the cylinder head is damaged/worn. Inspect head for damage and clean it from dust. There are also compressor repair kits that include new cylinder head. | |||
* It is not uncommon for the torx bolts attaching piston head to the compressor to break. Make sure to order spare bolts with the kit and be prepared to drill out the old remains. | |||
* While at it, don't forget to replace air dryer desiccant (silica gel) and dust filter. | |||
{| | {| | ||
| | |{{#ev:youtube|https://www.youtube.com/watch?v=p2QIh6WAlUU|320|left|Compressor unit pressure test using DAS (good vs bad).|frame}} | ||
| | |{{#ev:youtube|https://www.youtube.com/watch?v=Mp-qoqWuEg4|320|left|Wabco air suspension compressor piston ring repair.|frame}} | ||
|{{#ev:youtube|https://www.youtube.com/watch?v=rMfw2Sbjtbs|320|left|Wabco air suspension compressor piston ring replacement.|frame}} | |||
| | |} | ||
|} | |||
=== Valve Block Repair === | |||
The most common faults and diagnosis: | |||
* Fault in electrical solenoid valve. Can be tested by supplying 12v voltage to the pins of electrical connector. In case of failure the repair is not possible (all valve solenoids are part of one big monolith). | |||
==== | * Due to oxidation process the valve block separates and lets the air through (see picture below). Possible to clean the oxidation layer and reattach the halves. | ||
* Valves do not close tight, letting the air through. Oxidation layer can be cleaned with some reagent. O-rings can be changed (see below). | |||
* | * Bad pressure sensor (usually misdiagnosed). Pressure sensor can be replaced separately. | ||
* | * Rusty or broken electrical contact pins of pressure sensor or valve control. | ||
* | {| | ||
|[[File:W220_airmatic_valve_block_repair.jpg|thumb|none|Oxidation between block halves]] | |||
|[[File:W220_airmatic_valve_block_metal_cleaned.jpg|thumb|none|Before and after cleaning]] | |||
|[[File:W220_airmatic_valve_block_oxidation_in_ports.jpg|thumb|none|Oxidation in ports]] | |||
|} | |||
==== O-ring repair kit ==== | |||
There are sellers on eBay who sell valve block O-ring repair kit with set of 18 O-rings (~30 EUR). | |||
<!-- https://www.benzworld.org/threads/w220-airmatic-valve-block-rebuild-o-ring-specs.3082474/ --> | |||
{| | |||
|[[File:W220_airmatic_valve_block_o-rings.jpg|thumb|none|Valve block O-ring repair kit]] | |||
|[[File:W220_valve_block_orings_measure.jpg|thumb|none|O-rings measured]] | |||
| | |||
* 1x O-ring for the groove of the plastic piece of the block (2mm thick, 30.4mm long, ID 94mm, OD 98mm) | |||
* 1x O-ring for the pressure sensor (2mm thick, ID 9mm, OD 13mm) | |||
* 5x O-ring for the upper solenoid groove (1.5mm thick, ID 3.5mm, OD 6.5mm) | |||
* 5x O-ring for the lower solenoid groove (1.5mm thick, ID 7.5mm, OD 10.5mm) | |||
* 6x O-ring for the pressure line hoses (1.5mm thick, ID 6.5, OD 9.5mm) | |||
|} | |||
<!-- http://forums.mercedesclub.org.uk/index.php?threads/w220-airmatic-valve-block-leak-tips.163935/ --> | |||
Instructions: | |||
# Two mounting assemblies need to be removed to open the valve block casing. The removal of those two mounting bolts may require some PB Blaster penetrating fluid, as the blocks can have very heavy corrosion on those mounting bolts. | |||
#: This is one of the two mounting bolt holes. | |||
#: [[File:W220 Airmatic Valve Body Assembly Bolts.jpg|thumb|none|Valve block mounting bolt]] | |||
# There are also two lugs on each side used to hold the Solenoid Pack / Cover in place. | |||
#: [[File:W220 Airmatic Valve Block Cover Lugs.JPG|thumb|none|Valve block lugs]] | |||
# Use four small electrical screwdrivers or wooden or plastic wedges to hold the plastic solenoid pack's lugs up. | |||
#: [[File:W220 Airmatic Valve Block Cover Removal Procedure.JPG|thumb|none|Valve block Cover Removal Using Screw Drivers]] | |||
# Douse with the whole assembly with WD40 or similar and wriggle, wriggle and wriggle until the two halves of the valve block come free. | |||
# When reassembling the two halves of the valve block, add only the smaller o-rings to the solenoid posts, and put the larger o-rings into the recesses on the underside of the metal block and ensure they are well seated. This helps with reassembly to ensure the larger solenoid o-rings do not get damaged or misaligned when putting back together. You may find the larger o-rings getting nipped/cut if reassembled with them on the posts. | |||
# On the underside of the metal block around the ports which the solenoid pins engage, there are some very small slots which marry up with some very small plastic moldings on the solenoid block. Ensure these slots are cleaned of any deposits. You can use a pin and a razor blade to tease out the deposits. Doing this will help ensure a nice snug fit when putting back together. | |||
# Use a dielectric grease sparingly on the o-rings. | |||
# Ensure all deposits are cleared off, and use an airline to blow through all the passages. | |||
# You may need to use a vice carefully to press the solenoid block and metal block back together. Ensure the plastic cover clips well over the metal lugs on the metal block. | |||
{| | |||
|[[File:W220_airmatic_valve_block_separated.jpg|thumb|none|Valve block separated]] | |||
|[[File:W220_airmatic_valve_block_removed_old_orings.jpg|thumb|none|Old O-rings removed]] | |||
|[[File:W220_airmatic_valve_block_new_seal_to_solenoid_block.jpg|thumb|none|New seal for solenoid block halves]] | |||
|} | |||
=== | === Line Repair === | ||
<!-- http://www.mbca.org/sites/default/files/7007586_Repairing%20AIRmatic%20pressure%20line.pdf --> | |||
<!-- http://www.benzworld.org/forums/w220-s-class/2105577-airmatic-wtf-4.html --> | |||
<!-- http://www.benzworld.org/forums/w220-s-class/ | |||
For the location and routing of the AIRmatic air lines see above. | |||
If you have diagnosed a leak in any of the AIRmatic pneumatic lines, the repair options are to: | |||
*Cut out the failed section and reconnect using an in-line joiner. | |||
*Replace the failed section of air line with a M-B repair kit (5 ft length only available). | |||
*Replace the complete air line with an aftermarket high pressure flexible nylon pneumatic line. | |||
*Bypass the complete air line with an aftermarket high pressure flexible nylon pneumatic line. | |||
The air lines to the rear struts go through the interior and it may be difficult to find the leak unless the crack is large enough so that the crack can be located thanks to a loud hissing sound. Alternative line can be run from front valve block to the rear to test if the line is faulty. | |||
{| | {| | ||
| | |[[File:W220_Airmatic_air_line_parallel_outside.jpg|thumb|none|Alternative line running to the rear.]] | ||
| | |[[File:W220_Airmatic_air_line_parallel_inside.jpg|thumb|none|Alternative line connected to the rear strut.]] | ||
|} | |} | ||
M-B sells the AIRmatic air line (pipe/hose/tube) in 5 ft lengths, maximum. From the factory, the air line is built using a continuous length of line with no joins. The M-B 5 ft lengths are just for repairs, so connectors will be needed. | |||
{| | |||
|[[File:A2203271045.jpg|thumb|none|Repair section of air line (A2203271045). Price EUR 14.]] | |||
[[File: | |[[File:AIRmatic Aftermarket Nylon Air Line.JPG|thumb|none|Aftermarket nylon air line.]] | ||
|} | |||
However, you can buy aftermarket 4x2.5mm nylon high pressure flexible pneumatic lines of any length which are much cheaper than OEM lines (search keyword "4mm Hose Flexible Nylon Natural / Tube Pneumatic Air Line / 5m Roll"). Various colours are available and can be used to match the OEM colour code. | |||
M-B also sells an air line repair connector (junction/fitting) A0003270169 which can be used to re-connect an air line after cutting out the broken section. However, there are also available cheap and reliable plastic "push in" connectors which can be used to easily connect air lines without any tools. | |||
{| | {| | ||
| | |[[File:A0003270169.jpg|thumb|none|Air line repair connector (A0003270169). Price EUR 45.]] | ||
| | |[[File:A0003270169_aftermarket_equivalent.jpg|thumb|none|4mm "push in" pneumatic fitting. Alternative to A0003270169. Price EUR 3.]] | ||
|[[File:W220_A0003270369_connector.jpg|thumb|none|Connector to connect air hose to struts, reservoir and valve block (A0003270369). Price EUR 4.]] | |||
|} | |} | ||
=== | === Leaking Front Strut Air Spring - Repair Options === | ||
<!-- SI32.22-P-0004A --> | |||
'''Leaking front strut air spring''' | |||
Air spring of the front suspension strut is shown in the next figure. | |||
The lower flared conical part of the air spring protective boot/bellows (n) is the "air spring plunger". | |||
The plunger mates to the "support bushing/bearing" which is the conical shaped seat on the damper unit. | |||
[[File:W220_airmatic_front_air_spring_repair_kit.jpg|thumb|none|Air spring of front strut.]] | |||
A common issue when a Front Suspension Strut deflates completely and the car is then jacked up so that the strut is fully extended is that the Air Spring Plunger separates from the Damper Support Bearing. | |||
'''Note:''' Air suspension struts on which the Air Spring Plunger (7) is separated from the Support Bearing can sometimes be filled with air again without problems. They do not necessarily need to be exchanged for a new suspension strut. However the strut must be filled while the protective boot/bellows (n) is aligned to the Damper Support Bearing. The method is to pressurize the suspension strut using STAR Diagnosis and at the same time press the Air Spring protective boot/bellows upwards as far as it will go to remove any crinkles. Then pull it smoothly and evenly downwards and press onto the support bearing. No air must escape from the plunger to support bearing contact surface otherwise pressure can not be built up in the Air Spring. | |||
{| | |||
|[[File:W220_airmatic_front_strut_repearable.jpg|thumb|none|Repairable front strut damage (leaking air between the air spring plunger (7) and the support bearing).]] | |||
|[[File:W220_repair_front_strut_1.png|thumb|none|Picture 1: Air spring plunger (7) separated from the support bearing (conical shape at the bottom).]] | |||
|[[File:W220_repair_front_strut_2.png|thumb|none|Picture 2: Grasp the air spring plunger (7) with the hand.]] | |||
|[[File:W220_repair_front_strut_3.png|thumb|none|Picture 3: Pull the air spring plunger (7) downwards by hand and press onto the support bearing.]] | |||
|} | |||
For an AIRmatic strut to deflate completely there may be a catastrophic failure of some internal component such as the air bag/bladder (h), but it can also mean that the residual pressure holding valve (k) is leaking so that the strut deflates over time. This residual pressure holding valve (k) normally blocks off the pressure chamber in the air spring from the supply line and closes at or below a residual pressure of 4-5 bar. For a leaking residual pressure holding valve (k) to cause a full deflation, the air supply line or the relevant valve in the Level Control Valve Unit (Y36/6) would also need to be leaking. | |||
A leaking Level Control Valve Unit (Y36/6) on its own should not cause the strut to deflate completely as the residual pressure holding valve (k) should be fully closed below 4-5 bar. | |||
''' | ''' Leak test ''' | ||
Before replacing a supposed leaky AIRmatic strut, always carry out a leak test on the head bearing using soapy water. Proceed as follows: | |||
* Fill the air spring (using the DAS or other means), and in the process pull the air spring plunger (7) downwards firmly by hand so that the air does not escape between the air spring plunger and the Damper support bearing (picture 2 and 3). | |||
* Once the suspension strut is filled, carry out the leak test on the head bearing and repair if necessary. A repair kit is available for this purpose. | |||
* After using the repair kit proceed as described above when filling the air suspension strut (picture 2 and 3) ie pull the air spring plunger (7) firmly downwards by hand so that the air does not escape between the air spring plunger and the support bearing. | |||
''' | ''' Repair options ''' | ||
If the head bearing is not leaking and the plunger is fully seated on the support bearing then the options are to; | |||
* Replace the complete AIRmatic strut. | |||
* Replace just the Air Spring of the AIRmatic Suspension Strut. (Note: This is the cheaper option but requires dismantling the failed Suspension Strut. It is a good option if the damper unit is in good condition. Refurbished Air Springs are available from Suspension Workshops. | |||
=== Remove/install front suspension strut === | |||
If a replacement front axle spring strut (40) has been procured, it is quite an easy task to swap them over. | |||
<!-- AR32.25-P-1017I, Remove/install the suspension strut, 11.11.09 | |||
MODEL 220 / / / / / (except 220.083 /084 /087 /183 /184 /187) except CODE (487) Active Body Control (ABC) | |||
--> | |||
==== Reassembly Front Air Suspension Strut (40)==== | {| | ||
# Fasten the air bag/bladder (h) to the strut top using the 1st crimp ring. | |[[File:W220_replace_front_suspension_strut.jpg|600px]] | ||
#:[[File:W220 Airmatic Front Spring Strut 01.jpg|300px | | | ||
#:The next Figures show the steel support ring for the lower strut tube (a), which provides support for the 2nd or lower crimp ring. | * 17 - Spring control arm | ||
#:[[File:W220 Airmatic Front Spring Strut 02.jpg|300px | * 40 - Suspension strut | ||
# Install the strut tube (a) into the air bag/bladder and secure with the 2nd crimp ring. | * 40a - Pressure line connection | ||
#:The next Figure shows the rubber air bag/bladder which is mounted on the outside of the strut tube (a) and is held in place by metal crimp rings. | * 40b - Nuts (3) | ||
#:[[File:W220 Airmatic Front Spring Strut 03.jpg|300px | * 40c - Bolts (2 pcs.) | ||
#:Notes: | * X62/6 - Right front axle multiple circuit junction connector, major assembly compartment | ||
#:* The bottom end or plunger of the lower strut tube (a) is tapered which is for sealing to the support bearing on the damper unit. | * X62/7 - Left front axle multiple circuit junction connector, major assembly compartment | ||
#:* Note: the Airmatic strut can leak air from the bottom of the lower section if not seated against the rubber of the damper unit correctly. | * Y51 - Left front axle damping valve unit | ||
# Check the Seal between the damper and the air spring. | * Y52 Right front axle damping valve unit | ||
#:The next Figure shows the bottom air spring to damper seal open and fully seated. | * a - Residual pressure valve | ||
#:[[File:W220 Airmatic Front Spring Strut 04.jpg|300px | |} | ||
# Install top alloy dust cover. | |||
#:The next Figure shows the top dust seal alloy cover which is crimped to the strut top. | # Position wheels straight ahead | ||
#:[[File:W220 Airmatic Front Spring Strut 05.jpg|300px | # ''Jack up the rear or just one side of the car as required. Support the car on stands.'' | ||
# Install the protective boot/bellows to the top dust seal alloy cover. | # ''Remove [[fuses|f32]]/40A (AIRmatic compressor fuse) from the relay box in engine compartment right. This is not strictly necessary, as the compressor should not engage if engine is not running.'' | ||
# Thoroughly clean the damper unit before it is fitted into the air spring. | # Empty suspension strut (40) affected using [[DAS]]. ''(Note: it is not strictly necessary to do this step - just be careful when opening the pressure line to release any residual air slowly.)'' | ||
# Unscrew pressure line connection (40a). ''Remove the pressure airline from the head of the strut using 10mm open ended spanner.'' Residual pressure in suspension strut up to 3.5 bar. Plug the pressure line for the duration of the repair operations. Installation: Check pressure line O-ring and replace if necessary. | |||
# Unscrew nuts (40b) on front end. ''Remove the three upper mounting nuts (13mm) at the strut head.'' Installation: Fit nuts (40b) then refill suspension strut in fully-assembled vehicle before torquing to specification ''(lightly tighten the three strut upper mounting nuts - they will be torqued fully once the car is ready to drive''). | |||
# Disconnect left front axle multiple circuit junction connector, major assembly compartment (X62/7) right front axle multiple circuit junction connector, major assembly compartment (X62/6). Connectors of damping valve unit and rpm sensor. Press against spring (arrow) to remove. ''(Note: WIS says to press down on the spring retaining clip to release the multi-electrical connectors.) If necessary the multi-electrical plugs X62/6 or X62/7 can be released by praising the spring retaining clip upwards. Separate the front strut multi electrical connector into two connectors thus releasing the front strut so that it can be removed.'' | |||
{| | |||
|[[File:W220 AIRmatic Front Strut Multi Electrical Connectors.JPG|thumb|none|Multi-electrical connectors and their spring retaining clip.]] | |||
|[[File:W220 AIRmatic Front Strut Multi Electrical Connectors Release Method.JPG|thumb|none|Multi-electrical connector release method.]] | |||
|[[File:W220 AIRmatic Front Strut Multi Electrical Connector Separated.JPG|thumb|none|Multi electrical connector before and after separating.]] | |||
|} | |||
<ol start="8"> | |||
<li>Remove bolts (40c) from spring strut (40). Installation: After installing, the bolts (40c) must close at least flush with the suspension strut (40) or be seated slightly lower in it. | |||
''Note: The AIRmatic front strut is attached to the ball joint of the lower suspension arm with two stub screws (5mm hex Allen key screws) on the bottom of the spring strut. | |||
{| | |||
|[[File:W220_airmatic_front_strut_ball_joint_stub_unscrew.jpg|300px]] | |||
|[[File:W220_airmatic_front_strut_ball_joint.jpg|300px]] | |||
|[[File:W220_airmatic_front_strut_ball_joint_stub_screws.jpg|300px]] | |||
|} | |||
* ''If required, apply heat to the bottom allen stub screws. Several people have reported difficult screw removal resulting in several broken hex wrenches, frustration or even stripped set screws that had to be drilled out. A very effective method to remove the screws is to use heat from a blow torch. A micro torch provides a nice small sharp flame that is easily controlled as to not cause any collateral damage.'' <!-- http://www.benzworld.org/forums/w220-s-class/2194369-airmatic-strut-set-screw-removal-heat.html --> | |||
{| | |||
|[[File:Welding_micro_torch.jpg|300px]] [[File:W220_airmatic_front_strut_ball_joint_stub_screw_torch.jpg|300px]] | |||
|[[File:W220_airmatic_front_strut_ball_joint_stub_unscrew_hex_wrench.jpg|300px]] | |||
|} | |||
* ''Loosen the two bottom allen stub screws (5mm hex Allen key). Do not fully remove the stub screws, just unscrew them so that about five threads are showing.'' | |||
{| | |||
|[[File:W220 AIRmatic Damper Stub Screws Partly Installed.JPG|300px]] | |||
|} | |||
* ''Loctite can be added to the exposed threads before installation. Note: It is very easy to strip the thread when starting the stub screws in dirty holes on an old damper unit. Not completely removing the stub screws during disassembly eliminates this problem. If a stub screw mangles the start of a thread, remove the Air Strut to a work bench and thoroughly clean the threads on '''both''' holes. They will be full of old Loctite sealer. Then screw a stub screw into the 'good' side and keep screwing it all the way through until it comes out the far side, and in the process reshaping the mangled thread. Do this a couple of times and the stub screw should then start properly. It is far easier to start the stub screws on a work bench than when in the car.'' | |||
</ol> | |||
<ol start="9"> | |||
<li>Slacken suspension strut (40) on ball joint of spring control arm (17) using a suitable lever. Check cup seal of ball joint in spring control arm (17) for damage. | |||
''Undo the upper control arm ball joint nut (17mm) until it reaches the end of its thread and leave in place to protect the thread. | |||
Use a ball joint separator tool to remove the upper control arm ball joint.'' | |||
[[File:Ball Joint Separater Tool.JPG|thumb|none|Ball joint separator tool.]] | |||
</ol> | |||
<ol start="10"> | |||
<li> Remove spring strut (40) downwards towards the side. Installation: When installing tighten the upper nuts (40b) first. | |||
</ol> | |||
<ol start="11"> | |||
<li>Fill suspension struts (40) in question using [[DAS]]. Pressurize to 5 bar. During filling the wheels must not contact the ground, as when filling in the deflected condition the air spring bellows in the suspension strut (40) is destroyed. ''In other words: '''Never completely lower the vehicle if the air shocks are not pressurized.''' Lower the jack partly until the car is at normal vehicle height (lower vehicle until distance axle center to lower edge of fender is about 400mm). Start the engine and wait for at least two minutes for everything to stabilize.'' | |||
</ol> | |||
<ol start="12"> | |||
<li>Check AIRmatic for leaks. | |||
</ol> | |||
<ol start="13"> | |||
<li> Install in the reverse order | |||
</ol> | |||
Torque specifications: | |||
* Nut, front suspension strut to front end: 20 Nm | |||
* Bolt, front suspension strut to spring control arm: 20 Nm | |||
* Air suspension pressure line to front suspension strut: 5 Nm | |||
====Tutorials==== | |||
Excellent replacement tutorials for the front struts are available here: | |||
{| | |||
|{{#ev:youtube|https://youtube.com/watch?v=5guGcaMabxw&si=EnSIkaIECMiOmarE|320|left|Front Air shock replacement (By Masood)|frame}} | |||
|{{#ev:youtube|https://www.youtube.com/watch?v=WJ8Q3DuKH8M|320|left|Front air shock replacement (by Arnott)|frame}} | |||
|{{#ev:youtube|https://www.youtube.com/watch?v=hiYy3fgpl0k|320|left|Front air shock replacement (by BILSTEIN)|frame}} | |||
|{{#ev:youtube|https://www.youtube.com/watch?v=YdSWq1RDuo0|320|left|Front air shock replacement (by David Prokity)|frame}} | |||
|{{#ev:youtube|https://www.youtube.com/watch?v=kxsLN-yWCyo|320|left|Front air shock replacement using jacks|frame}} | |||
|} | |||
===Remove/install rear suspension strut === | |||
''Replacing rear strut is more time consuming than replacing front strut. | |||
<!-- AR32.25-P-1016I, Remove/install rear suspension strut, 31.8.11 | |||
MODEL 220 except CODE (487) Active Body Control (ABC) --> | |||
{| | |||
|[[File:W220_airmatic_remove_install_rear_suspension_strut.jpg|400px]] | |||
| | |||
* 1 - Screw connection | |||
* 2 - Screw connection | |||
* 41 - Rear suspension strut | |||
* 41a - Pressure line connection | |||
* 41a - Nuts (3) | |||
* 72 - Spring control arm | |||
* 72c - Spring control arm covering | |||
* 72d - Bolts (4 pcs.) | |||
* Y53 - Left rear axle damping valve unit | |||
* Y53x1 - Damping valve unit connector | |||
* Y54 - Right rear axle damping valve unit | |||
* Y54x1 - Damping valve unit connector | |||
|} | |||
{| | |||
|[[File:W220_airmatic_remove_install_rear_suspension_strut_2.jpg|400px]] | |||
| | |||
* 1 - Screw connection | |||
* 2 - Screw connection | |||
* 3 - Screw connection | |||
* 4 - Thrust arm | |||
* 72 - Spring control arm | |||
|} | |||
Removal: | |||
# Depressurize suspension strut concerned (41) using [[DAS]]. ''(Note: it is not strictly necessary to do this step - just be careful when opening the pressure line to release any residual air slowly.)'' | |||
# ''Remove [[fuses|f32]]/40A (AIRmatic compressor fuse) from the relay box in engine compartment right. This is not strictly necessary, as the compressor should not engage if engine is not running.'' | |||
# Jack up one side of the car as required. Support the car on stands. | |||
# Remove rear wheel. | |||
# Remove cover (arrow) in parcel shelf. ''To avoid damage to the trim on the C-pillar it is best to remove it as it '''certainly will be damaged (bruised/compressed and possibly dirtied)''' if not removed. To remove C-pillar unscrew T30 bolt under SRS tab and pull it off.'' | |||
#: [[File:W220 Damage to C-Pillar Trim Removing AIRmatic Rear Strut with Annotation.JPG|thumb|none|Damaged C-pillar]] | |||
#: [[File:W220_right_C-pillar_removed.jpg|thumb|none|C-pillar removed]] | |||
# Unscrew pressure line connection (41a) ''using 10mm open ended spanner''. '''''Be warned''': pressure in the line between the valve block and the suspension strut can be very high so if pressure has not been released using [[DAS]], '''slowly''' unscrew the valve allowing the residual pressure to escape. (The residual pressure valve on the top of the strut prevents the release of the last bit of pressure. Residual pressure in suspension strut is up to 3.5 bar. This means that the strut will still exert considerable force on the suspension components.)'' | |||
# Plug the pressure line for the duration of the repair operations ''(just to make sure that dirt does not get in)''. | |||
# Unscrew nuts (41b) ''using the smallest 13mm socket and driver available''. | |||
# Pull off grommet and disconnect electrical connector of damping valve unit (Y53x1/ Y54x1) | |||
# Remove bolts ''(or plastic rivets)'' (72d) on spring control arm cover (72c). ''Remove spring control arm cover (72c).'' | |||
# ''Detach brake caliper from the wheel. Disconnect brake wear sensor and remove brake wear sensor bracket (right side only). The removal of brake caliper is not strictly necessary if vehicle is lifted high and hence there is enough space to pull out the strut downwards.'' | |||
# ''Remove stabilizer bar link bottom nut using 16mm socket and 22mm wrench. Detach the bottom part of the stabilizer bar.'' | |||
#: [[File:W220 Stabiliser Bar Link Removing Bottom Nut.jpg|thumb|none|Removal of stabilizer bar link bottom]] | |||
# Remove bolted connection (2) of suspension strut (41) on spring control arm (72) using 21mm socket from both sides. The residual pressure in the strut will prevent the bolt from being removed. Use unscrewing (instead of pulling) to remove the bolt. | |||
#: [[File:W220 Removing rear strut to spring control arm connection.jpg|thumb|none|Removing strut to spring control arm connection.]] | |||
# Remove bolted connection (1) of thrust arm (4) on rear axle carrier. ''In practice, this step is not necessary as even without loosening this bolt the string control arm should easily swing out of the way for the strut removal. | |||
#: [[File:W220 Spring Control Arm to Axle Carrier Inner bolted connection.jpg|thumb|none|Loosening the inner bolted connection of spring control arm to axle carrier]] | |||
# Remove bolted connection of spring control arm (72) on rear wheel carrier (using 21mm socket from one side and Torx E18 socket from the other). The residual pressure in the strut will prevent the bolt from being removed. Use unscrewing (instead of pulling) to remove the bolt. | |||
#: [[File:W220 Undoing spring control arm to wheel carrier bolted connection.jpg|thumb|none|Undoing spring control arm to wheel carrier bolted connection]] | |||
# Pull down track control arm (72) and remove strut assembly (41) by lowering it and pulling it out to the side. | |||
Installation: | |||
# Install strut by ''loosely'' fitting nuts (41b). (The vehicle must be in the ready to drive mode when torquing these three nuts.) | |||
# Install bolted connection (2) of suspension strut (41) on spring control arm (72). (The vehicle must be in the ready to drive mode when torquing this bolt.) | |||
# Install bolted connection (1) of thrust arm (4) on rear axle carrier (if this bolt was loosened or removed). (The vehicle must be in the ready to drive mode when torquing this bolt.) | |||
# Reattach stabilizer bar link bottom nut | |||
# Install bolted connection of spring control arm (72) and wheel carrier by wriggling the wheel carrier (use a jack to raise spring control arm as needed). (The vehicle must be in the ready to drive mode when torquing this bolt.) | |||
# Route strut's electrical line and reconnect connector of damping valve unit (Y53x1/ Y54x1) | |||
# Attach spring control arm cover (72c) | |||
# Reattach brake caliper (if was removed) | |||
# Reattach wheel | |||
# Screw pressure line connection (41a) | |||
# Fill suspension struts affected using [[DAS]]. Pressurize to 5 bar. '''''Warning:''''' During recharging the wheels should never be in contact with the floor; refilling with the suspension compressed leads to destruction of the air suspension bellows in the strut (41). If [[DAS]] is not available, start the car and check that the strut gets pressurized. If the strut is not being pressurized, stop the car, lock, unlock and start the car again. Operate Level Control Switch (N72/1s2) to force strut height adjustment. | |||
# Release the car from the jack slowly to check that the strut has enough pressure. Do not release the wheels fully before the struct has enough pressure. | |||
# Check that the car is on the ground and the vehicle is fully supported on the new strut. | |||
# Torque three fitting nuts (41b). | |||
# Attach cover (arrow) in parcel shelf. Reattach C-pillar. | |||
# Torque bolted connection (2) of suspension strut (41) on spring control arm (72) | |||
# Torque bolted connection (1) of thrust arm (4) on rear axle carrier (if this bolt was loosened or removed) | |||
# Torque bolted connection of spring control arm (72) and wheel carrier | |||
# Check for leaks | |||
Torque specifications: | |||
* Suspension struts: Nut, rear suspension strut to body: 20 Nm | |||
* Suspension struts: Air suspension pressure line to rear air spring: 5 Nm | |||
* Suspension struts: Nut, rear strut to spring control arm: 110 Nm | |||
* Spring control arm: Self-locking nut, to rear subframe: 50 Nm + 90 degrees | |||
* Spring control arm: Self-locking nut, to rear axle carrier: 70 Nm | |||
* Stabilizer bar link bottom nut: 40 Nm | |||
====Tutorials==== | |||
Excellent replacement tutorials for the rear struts are available here: | |||
{| | |||
|{{#ev:youtube|https://www.youtube.com/watch?v=jFmwLCCEAkI|320|left|Rear air shock replacement (by Arnott)|frame}} | |||
|{{#ev:youtube|https://www.youtube.com/watch?v=1f8bDYEalW4|320|left|Rear air shock replacement (by BILSTEIN)|frame}} | |||
|{{#ev:youtube|https://www.youtube.com/watch?v=K0WVj3Brfe8|320|left|Rear air shock replacement (by Masood)|frame}} | |||
|{{#ev:youtube|https://www.youtube.com/watch?v=SgdEH0uTDsM|320|left|Rear air shock replacement using jacks|frame}} | |||
|} | |||
===Replacing the Air Spring in an AIRmatic Strut=== | |||
As already described, a very common reason for a leaking strut is damage in the strut's rubber air bag/bladder (h). | |||
It is possible to purchase on eBay a refurbished front and rear air spring which is the top part of an air suspension strut for around EUR 120 and mount it to the original damper unit (the lower part of an air suspension strut). This requires the strut to be removed from the car and the air spring to be separated from the damper unit by partly dismantling the air spring. '''Note:''' Replacing only the strut's rubber air bag/bladder (h) of the air suspension strut is not suitable for a DIY project as it requires an hydraulic crimping tool. | |||
==== Dismantling Front Air Spring==== | |||
<!-- http://www.benzworld.org/forums/w220-s-class/2636330-airmatic-pic.html --> | |||
<ol> | |||
<li> Remove the complete front axle AIRmatic spring strut (40) from the vehicle. | |||
<li> Remove the epoxy/mastic using a hammer and a screw driver. ('''TIP''': If you are doing this with the strut still in the car, avoid getting pieces of epoxy/mastic in the engine.) | |||
{| | |||
|[[File:AIRmatic Removing Top Seal.JPG|thumb|none|Removing top seal of front strut.]] | |||
|[[File:AIRmatic Top After Removing Mastic.JPG|thumb|none|Top seal removed.]] | |||
|} | |||
<li> Using a special tool (see below) unscrew the residual pressure holding valve (k). | |||
{| | |||
|[[File:AIRmatic Residual Pressure Holding Valve Removed.JPG|thumb|none|Tool to unscrew the residual pressure valve.]] | |||
|[[File:W220 AIRmatic Residual Pressure Holding Valve 01.JPG|thumb|none|Residual pressure holding valve (removed).]] | |||
|} | |||
<li> If required close the opening of the residual pressure holding valve (k) with a short bolt M8, so that no dirt can penetrate into the air suspension strut. | |||
<li> Using a special tool (see below) fit the tool to the Strut. Tighten the central nut to the plate from the inside and this will wind down the bolt pushing the Air Spring top metal disc inwards slightly releasing the snap ring. | |||
{| | |||
|[[File:W220 strut top seal tool 02.jpg|thumb|none|Strut top seal tool.]] | |||
|[[File:W220 strut top seal tool 03.jpg|thumb|none|Strut top seal tool.]] | |||
|} | |||
<li> Remove the snap ring. ('''TIP''': Use a small screwdriver to help remove the circlip lock snap ring but make sure it does not cause any scratches and burrs, otherwise the sealing of the new lock ring may be compromised. Remove any sharp edges or burrs if required.) (Note: a new circlip lock snap ring is provided in the top seal kit, see below.) | |||
<li> Remove the tool. | |||
<li> Remove the top seal metal disc cover with its 'O' ring. (Note: Run a small screwdriver around the edge of the disc and then keep manipulating the disc until it starts to come free. Use a small screw driver to lever the disc out. A very strong magnet can help.) (Note: a new top seal metal disc cover and a new 'O' ring are provided in the top seal kit, see below. A new top seal metal disc cover and a new 'O' ring are often provided with a new/refurbished air spring.) | |||
{| | |||
|[[File:W220 AIRmatic Front Strut Snap Ring Removed.JPG|thumb|none|Snap ring.]] | |||
|[[File:W220 AIRmatic Front Strut Metal Disc Removed.JPG|thumb|none|Metal disc cover.]] | |||
|[[File:W220 AIRmatic Front Strut Top Seal Cover Outside View.JPG|thumb|none|Outside view of metal disc (A2203280621).]] | |||
|[[File:W220 AIRmatic Front Strut Top Seal Cover Inside View.JPG|thumb|none|Inside view of metal disc (A2203280621).]] | |||
|} | |||
<li> Inspect the inside of the top of the Front Strut for any sharp edges or burrs and remove if required. | |||
<li> Drill a 4mm hole and if necessary insert a screw or similar device part way into the nylon plug which can then be pulled out. (Note: a new nylon plug is available with part number TBD.) | |||
{| | |||
|[[File:W220 AIRmatic Front Strut After Removing Metal Disc.JPG|thumb|none|Strut after removing metal disc.]] | |||
|[[File:W220 AIRmatic Front Strut Plastic Plug Removed.JPG|thumb|none|Plastic plug removed.]] | |||
|[[File:W220 Front Spring Strut Nylon Cover.jpg|thumb|none|Nylon cover.]] | |||
|[[File:W220 AIRmatic Front Strut After Removing Plastic Plug.JPG|thumb|none|Strut after removing plastic nylon plug.]] | |||
|} | |||
<li> Use an air impact driver to undo the lock nut on the top of the damper piston rod (e). (Note: unfortunately it is essential to use an impact wrench as the piston rod in the damper unit can not be restrained from turning. The impact wrench shocks the nut undone.) | |||
<li> Remove the complete air spring from the damper unit. | |||
[[File:W220 AIRmatic Front Strut Air Spring Separated from Damper Unit.JPG|thumb|none|Strut spring separated from damper unit.]] | |||
<li> From the '''inside''' of the Air Spring use a long piece of rod or tubing to press out the upper mount rubber bush. | |||
{| | |||
|[[File:W220 AIRmatic Front Strut Upper Mount Iso View.JPG|thumb|none|]] | |||
|[[File:W220 AIRmatic Front Strut Upper Mount Top View.JPG|thumb|none|]] | |||
|[[File:W220 AIRmatic Front Strut Upper Mount Side View.JPG|thumb|none|]] | |||
|[[File:W220 AIRmatic Front Strut Upper Mount Back View.JPG|thumb|none|]] | |||
|} | |||
{| | |||
|[[File:W220 AIRmatic View of Front Strut Air Spring with Upper Mount Removed.JPG|thumb|none|Outside view of the strut with bush removed.]] | |||
|[[File:W220 Front Spring Strut Top Plate Inside View.jpg|thumb|none|Inside view of the strut with bush removed.]] | |||
|} | |||
*The yellow arrow points to the hole going through the upper mount rubber bush for the damper piston rod (e). | |||
*The blue arrow points to the inside of the Air Spring for the rubber air bellows (h). | |||
*The red circle shows the threaded brass air inlet to the Air Spring. | |||
</ol> | |||
==== Reassembly Front Air Suspension Strut (40)==== | |||
# Fasten the air bag/bladder (h) to the strut top using the 1st crimp ring. | |||
#:[[File:W220 Airmatic Front Spring Strut 01.jpg|300px]] | |||
#:The next Figures show the steel support ring for the lower strut tube (a), which provides support for the 2nd or lower crimp ring. | |||
#:[[File:W220 Airmatic Front Spring Strut 02.jpg|300px]] | |||
# Install the strut tube (a) into the air bag/bladder and secure with the 2nd crimp ring. | |||
#:The next Figure shows the rubber air bag/bladder which is mounted on the outside of the strut tube (a) and is held in place by metal crimp rings. | |||
#:[[File:W220 Airmatic Front Spring Strut 03.jpg|300px]] | |||
#:Notes: | |||
#:* The bottom end or plunger of the lower strut tube (a) is tapered which is for sealing to the support bearing on the damper unit. | |||
#:* Note: the Airmatic strut can leak air from the bottom of the lower section if not seated against the rubber of the damper unit correctly. | |||
# Check the Seal between the damper and the air spring. | |||
#:The next Figure shows the bottom air spring to damper seal open and fully seated. | |||
#:[[File:W220 Airmatic Front Spring Strut 04.jpg|300px]] | |||
# Install top alloy dust cover. | |||
#:The next Figure shows the top dust seal alloy cover which is crimped to the strut top. | |||
#:[[File:W220 Airmatic Front Spring Strut 05.jpg|300px]] | |||
# Install the protective boot/bellows to the top dust seal alloy cover. | |||
# Thoroughly clean the damper unit before it is fitted into the air spring. | |||
#:The next Figure shows a close-up of the strut damper with the bump stop buffer (i) and bump stop cover. The damper is fitted after the air spring has been assembled. It slides through the strut top and then has the upper mount rubber bush and nut fitted followed by the nylon cover and then the top metal disc cover and lock ring. Note the large conical rubber support bearing which provides the air spring to damper seal. | #:The next Figure shows a close-up of the strut damper with the bump stop buffer (i) and bump stop cover. The damper is fitted after the air spring has been assembled. It slides through the strut top and then has the upper mount rubber bush and nut fitted followed by the nylon cover and then the top metal disc cover and lock ring. Note the large conical rubber support bearing which provides the air spring to damper seal. | ||
#:[[File:W220 Airmatic Front Spring Strut 07.jpg|300px | #:[[File:W220 Airmatic Front Spring Strut 07.jpg|300px]] | ||
# Prepare the strut top plate to take the Damper Unit. | # Prepare the strut top plate to take the Damper Unit. | ||
#:The next three figures show; | #:The next three figures show; | ||
#:* (left image) the strut top plate with the hole for the damper, | #:* (left image) the strut top plate with the hole for the damper, | ||
#:* (center image) the strut top plate with the upper mount rubber bush in place waiting for the nyloc nut, (Note: an impact wrench is used to tighten the nut (with Loctite applied) to the damper piston rod.) | #:* (center image) the strut top plate with the upper mount rubber bush in place waiting for the nyloc nut, (Note: an impact wrench is used to tighten the nut (with Loctite applied) to the damper piston rod.) | ||
#:* (right image) the strut top with the nylon cover placed over the nut. | #:* (right image) the strut top with the nylon cover placed over the nut. | ||
#:[[File:W220 Airmatic Front Spring Strut 08.jpg|500px | #:[[File:W220 Airmatic Front Spring Strut 08.jpg|500px]] | ||
# The next two figures show the metal disc cover with the 'O' ring installed ('''TIP''': use silicon grease to ensure it is leak free) and the lock ring ready to be fitted using the strut top seal tool. | # The next two figures show the metal disc cover with the 'O' ring installed ('''TIP''': use silicon grease to ensure it is leak free) and the lock ring ready to be fitted using the strut top seal tool. | ||
#:[[File:W220 Airmatic Front Spring Strut 09.jpg|300px | #:[[File:W220 Airmatic Front Spring Strut 09.jpg|300px]] | ||
# Install the residual pressure holding valve (k) using the commercial tool or DIY modified spanner. | # Install the residual pressure holding valve (k) using the commercial tool or DIY modified spanner. | ||
# Support the strut vertically and fill the top of the strut with a black butyl mastic to reduce vibration damage to the air inlet valve. | # Support the strut vertically and fill the top of the strut with a black butyl mastic to reduce vibration damage to the air inlet valve. | ||
#:'''TIP''': If a pour-able butyl mastic can not be sourced, Sika manufacture a range of butyl mastic sealers which can be extruded in thin layers (5mm thick). Use a spatula to smooth the layer evenly and then leave it to set. Repeat the layering process until the cavity is filled. The result is not as neat as the OEM but it does the job. If required the extruded layers technique can be done with the Air Strut installed in the car as the compound is quite viscous and will not run. | #:'''TIP''': If a pour-able butyl mastic can not be sourced, Sika manufacture a range of butyl mastic sealers which can be extruded in thin layers (5mm thick). Use a spatula to smooth the layer evenly and then leave it to set. Repeat the layering process until the cavity is filled. The result is not as neat as the OEM but it does the job. If required the extruded layers technique can be done with the Air Strut installed in the car as the compound is quite viscous and will not run. | ||
[[File:W220 AIRmatic Repaired Front Strut Filled with Butyl Mastic.JPG|300px | [[File:W220 AIRmatic Repaired Front Strut Filled with Butyl Mastic.JPG|300px]] | ||
==== Tools Required for Replacing Air Spring in Front Air Suspension Strut (40)==== | |||
<ul> | |||
<li> AIRmatic residual pressure holding valve tool. Used to remove and install the brass residual pressure holding valves at each of the air inlets to the front air suspension struts. DIY tool can be made by modifying either a ½” or 3/8" spanner by grinding it down to fit the residual pressure holding valve. | |||
==== Tools Required for Replacing Air Spring in Front Air Suspension Strut (40)==== | {| | ||
|[[File:W220 AIRmatic Residual Pressure Holding Valve Commercial Removal Tool.JPG|thumb|none|Commercial 1/4" drive tool.]] | |||
[[File:W220 AIRmatic Residual Pressure Holding Valve | |[[File:W220 strut top seal tool 04.jpg|300px|thumb|none|1/2" spanner.]] | ||
[[File:AIRmatic DIY Residual Pressure Holding Valve Removal Tool.JPG|thumb|none|DIY residual pressure tool.]] | |||
[[File:W220 strut top seal tool | |[[File:W220 AIRmatic Residual Pressure Holding Valve Dimensions.JPG|thumb|none|Critical dimensions of the residual pressure holding valve.]] | ||
|} | |||
</ul> | |||
<ul> | |||
<li> Front strut top seal remover tool. | |||
[[File:W220_airmatic_front_strut_top_seal_tool.jpg|thumb|none|Commercial strut top seal tool.]] | |||
</ul> | |||
<ul> | |||
<li> DIY home-made strut top seal tool can be made from a 150mm x 150mm piece of 6mm (1/4") steel plate. | |||
{| | |||
|[[File:DIY AIRmatic Front Top Seal Tool Dimensions.JPG|thumb|none|mark-up dimensions for the DIY front strut top seal remover tool.]] | |||
|[[File:W220 strut top seal tool 01.jpg|thumb|none|Parts for DIY strut top seal tool.]] | |||
|} | |||
#Accurately mark up the steel plate as per the figure above which shows the mark-up dimensions for the DIY AIRmatic front strut top seal remover tool. | |||
##Draw the two diagonals to establish the centre of the plate. | |||
##Mark with a centre pop. | |||
##Set a divider to 61.5mm radius. | |||
##Draw a circle with the divider around the centre pop producing the pitch circle diameter of 123mm. | |||
##Centre pop the first hole on one of the diagonals. | |||
##Use the divider still set to a radius of 61.5mm and mark six arcs around the circumference of the PCD. This divides the PCD into six equal chords. (Alternatively set the divider to 106.5mm and scribe across the PCD in two places.) | |||
##Centre pop the required intersections for the other two 8mm holes. | |||
##Visually check that the centre pop marks match the pitch circle diameter (pcd) of the strut top plate mounting bolts. | |||
##Drill the three off 8mm holes. | |||
##Drill one 10mm hole in the center. | |||
##Obtain three off 120mm long 8mm bolts for the three 8mm holes. | |||
##Use three 8mm joiner nuts to attach the 8mm bolts to the strut top. (Alternatively four off 8mm nuts can be welded together to make one off 'long' nut.) | |||
##Obtain one off 150mm long 10mm bolt for the center 10mm hole. | |||
##Thread a nut right to the top of the 10mm bolt and add a flat washer with a little bit of grease. | |||
</ul> | |||
* Impact driver (Note: is absolutely essential for removing the nut at the top of the damper unit.) | |||
<ul> | |||
<li> Top seal repair kit. Includes: steel cap, brass valve and spring clip. Part number A2203202538 (~EUR 125). | |||
[[File:AIRmatic Top Seal Repair Kit A2203202538.JPG|thumb|none|Top seal repair kit (A2203202538).]] | |||
</ul> | |||
====Tutorials==== | |||
Excellent replacement tutorials for the front and rear struts are available here: | |||
{| | |||
|{{#ev:youtube|https://www.youtube.com/watch?v=zACt4F7TvYY|320|left|W220 front strut separation.|frame}} | |||
|{{#ev:youtube|https://www.youtube.com/watch?v=9VzGNQowXo0|320|left|W220 rear strut assembly.|frame}} | |||
|} | |||
===Remove/install front axle level sensors=== | |||
<!-- AR82.10-P-0004I, Remove/install front axle level sensors, 8.12.97 | |||
MODEL 215, MODEL 220 --> | |||
{| | |||
|[[File:W220_Remove_install_front_axle_level_sensors.jpg|400px]] | |||
| | |||
* 6 - Upper track control arm | |||
* 86 - Connecting rod | |||
* 86a - Retaining plate | |||
* 86c - Nut | |||
* 86d - Bolts (2 ea.) | |||
* B22/8 - Left front level sensor | |||
* B22/9 - Right front level sensor | |||
* e - Hole | |||
* f - Hole for level sensor connecting rod | |||
|} | |||
Remove/Install: | |||
# Replace self-locking nuts and bolts | |||
# Remove front wheels | |||
# Disconnect connectors at front left and right level sensors (B22/8, B22/9) | |||
# Unscrew nut (86c) on connecting rod (86) from front left and right level sensors (B22/8, B22/9) | |||
# Unscrew nut (86b) on connecting rod (86) from upper wishbone (6) and remove connecting rod (86). Installation:Attach connecting rod (86) to the outermost hole (f) on the upper wishbone (6). | |||
# Unscrew bolts (86d) on retaining plate (86a) and remove front left and right level sensors (B22/8, B22/9) | |||
# Install in the reverse order | |||
# After replacing the level sensors, calibrate vehicle level with Star Diagnosis (level calibration) | |||
Torque specification: | |||
* Nut, level sensor connecting rod to upper wishbone: 10 Nm | |||
* Nut, connecting rod to level sensor: 5 Nm | |||
* Bolt/nut of level sensor to retaining plate: 4 Nm | |||
===Remove/install rear axle level sensor=== | |||
<!-- AR82.10-P-0005I, Remove/install rear axle level sensor, 19.1.10 | |||
MODEL 220 except CODE (487) Active Body Control (ABC) --> | |||
{| | |||
|[[File:W220_Remove_install_rear_axle_level_sensor.png|400px]] | |||
| | |||
* 81 - Torsion bar link | |||
* 85 - Control rod | |||
* 85a - Retaining plate | |||
* 85b - Nuts (3) | |||
* 85c - Bolts (2 pcs.) | |||
* 85D - Nut | |||
* 85E - Nut | |||
* B22/3 - Rear axle level sensor | |||
|} | |||
Remove/Install: | |||
# Replace self-locking nuts and bolts | |||
# Disconnect plug from rear axle level sensor (B22/3) | |||
# Unscrew nut (85e) of control rod (85) from stabilizer bar intermediate lever (81) | |||
# Unscrew nut (85d) of control rod (85) at level sensor (B22/3) and remove control rod (85). Do not separate control rod (85) or change the adjustment. | |||
# Remove bolts (85c) of retaining plate (85a) at level sensor (B22/3) and remove level sensor (B22/3) | |||
# Install in the reverse order | |||
# Calibrate vehicle level using Star Diagnosis after replacing the level sensor | |||
* | Torque specification: | ||
* | * Nut, level sensor link rod to torsion bar intermediate lever: 10 Nm | ||
* Nut, control rod to level sensor: 5 Nm | |||
* Bolt, level sensor to retaining plate: 4 Nm | |||
* Nut, retaining plate to frame floor: 8 Nm | |||
===Airmatic Adjusting Levels Using [[STAR Diagnosis System (SDS) or Diagnosis Assistance System (DAS)]]=== | |||
See Section [[Airmatic Adjusting Levels Using DAS]] |
Latest revision as of 21:48, 7 April 2023
Introduction
All W220 vehicles come with Airmatic pneumatic suspension system, unless vehicle has option code 487 - ABC SUSPENSION (ACTIVE BODY CONTROL) in which case the vehicle is equipped with Active Body Control (ABC) hydraulic suspension system with additional computer control. ABC system provides greater roll control and eliminates any "nosedive" even with heavy braking (not that there is much of either with Airmatic). Both suspension systems are responsible for the superb ride and handling of the W220 and being complex systems will require maintenance.
Airmatic systems on earlier cars tended to fail more often than on the '03 and later - the '04s and on are less problematic. However, there is no such thing a "bulletproof" pneumatic suspension system. Seals and pumps will wear, and struts will have to be replaced. You'd have to do the same thing with standard shocks, too - but Airmatic will be more expensive. The best protection is to become familiar with the early signs of Airmatic problems, and fix them right away. Letting them go runs the cost up.
They are not especially problematic, but like any complex system, they break - and any luxury car is expensive to repair. Keep in mind that if the garage you use does not have STAR Diagnostics and can not interpret the values both in sensor voltage and other tests, then don't waste your time and money. Find someone who can. DIY is possible but preferably requires use of STAR Diagnostics with some prior experience and always lots of patience.
One common failure point which was initially subject to inspection and free replacement, was the high-pressure line from the pump to the valve body.
Another common weakness in the pre '03-ish W220's compared to those from a few years later, is the seals at the tops of the front suspension struts. The older design can leak air over time. The newer models and ones with new replacement parts do not leak. Cars that were under warranty could have these seals replaced with that coverage.
Other issues are discussed below.
The EMERGENCY Procedure, or what to do if your car is sitting on the ground, is shown below.
Some of the air suspension components covered in this page are also used in W211, W216, W219, W221, W240 and W639 MB chassis vehicles.
Description
The W220 AIRmatic system is a fully supporting air suspension system which provides both static and dynamic support by means of four air struts located at the wheels. Each strut has an air spring containing an air bag (bladder) and a dampener built-in to the one unit. The struts get air via a valve distribution unit from an air compressor located behind the front bumper close to the front right wheel well. On the opposite side is the central reservoir which stores air pressure for use when the pump is not running. The valve unit is connected to a computer which monitors the air pressure, the vehicle weight, the vehicle height requirement and vehicle stance (angle) and then sets the ride height accordingly.
Features
- Level control both manual and speed sensitive.
- Electronic level control which maintains a constant even level at the front and rear axles according to the driving and vehicle load conditions.
- When the vehicle is stationary the level is readjusted if there is a difference of more than +/- 10mm after a door or the trunk lid is opened.
- While driving the level is readjusted if there is a difference of more than +/- 20mm. The level is adjusted to +/- 10 mm every 15 minutes.
- Active Damping System (ADS) which changes the damping forces according to the road conditions and the driver's driving style. The road conditions are determined by vertical acceleration sensors in the body of the vehicle. The horizontal acceleration is determined by measuring the vehicle speed and turn angle.
Advantages
Higher level of driving safety and ride comfort due to:
- Adapting damping to road conditions and driving style.
- Low location of centre of gravity as vehicle lowers above 70KPH.
- Low aerodynamic drag and fuel consumption as vehicle lowers above 70KPH.
- Less tendency for vehicle to lift at speed.
Individual adaptation due to:
- Raising vehicle level for poor road surfaces and when negotiating driveways.
- Two possible damping levels for comfort or sport driving styles in vehicles produced up to 08/99.
- Three possible damping levels for comfort, sport or extreme sport driving styles in vehicles produced after 09/99.
Driver information due to:
- Vehicle level displayed by indicator lamps and switches.
- Warning messages in multi-function display if vehicle is too low.
Function
The functions of the AIRmatic with Adaptive Damping System (ADS) control module are divided as follows:
- Signal conditioning
- Function logic component
- Safety circuit
Signal conditioning
The following input signals are processed by the function logic component and used for calculations or to provide information:
- Calculation of body vertical acceleration
- Signal from body acceleration sensors
- Calculation of vehicle speed
- Wheel speed signal
- Speed status signal
- Calculation of longitudinal and lateral acceleration
- Wheel speed signal
- Signal from steering angle sensor
- Calculation of compressor control
- Outside temperature, outside air pressure signal
- Reservoir pressure signal
- Vehicle speed signal
- Vehicle level signal
- Duty cycle
- Calculation for valve control
- Level signal from left front axle, right front axle
- Rear axle level signal
- Calculation for control of main reservoir charge valve
- Level signal from left front axle, right front axle
- Rear axle
- Pressure signal
- Calculation of vehicle level
- Signal from level sensors
- Information signals (control)
- Signal from stop lamp switch
- Signal from comfort and sport switch
- Signal from level control switch
- Signal from door contact switch, trunk, remote control
Function logic component
The conditioned input signals are processed in the logic component and converted into output signals.
- Signal from body acceleration sensors (B24/3, B24/8, B24/9):
- The vertical acceleration of the vehicle is calculated using the signals from the body acceleration sensors.
- Front wheel speed signal, left and right:
- Using the wheel speed signal, the ESP control module calculates
- Vehicle speed
- Longitudinal acceleration
- Vehicle status. A distinction is made between a moving and a stationary vehicle. Incorrect wheel speed signals are also detected.
- Steering angle sensor signal (N49):
- The lateral acceleration of the vehicle is calculated using the steering angle sensor signal and the wheel speed signal.
- Signal from level sensors (B22/8, B22/9, B22/3):
- Both front axle level sensors each supply 2 signals. The sensors detect and transfer the distance between the wheel center and the body at both the left and right-hand side of the vehicle.
- The rear axle level sensor supplies 2 signals. The sensor detects and transfers the distance between the wheel center and the body (average calculated from left and right wheel).
- Brake lamp switch signal (S9/1):
- When the driver presses the brake pedal, a signal is received by the ADS logic component and the damping at all wheels is set to "hard". The pitch motion of the vehicle when braking can therefore be reduced.
- Comfort and sport switch signal (N72/1s3):
- The comfort and sport switch signal informs the system about the selection made by the driver between one comfort-oriented and 2 sporty damping maps. The "comfort" setting maintains the damping within the comfortable range as far as the driving style and road conditions will allow. The "Sport 1" setting makes the damping somewhat "harder". The "Sport 2" setting immediately sets the damping force to "hard". The driver's preferred settings are stored until changed by the driver (even with Ignition OFF).
- Signal from level adjustment switch (N72/1s2):
- The control module uses the signals from the level adjustment switch to determine the driver's preferences for the vehicle level:
- Normal level
- Raised level
- The control module uses the signals from the level adjustment switch to determine the driver's preferences for the vehicle level:
- ADS II
- The control module uses the vertical body acceleration, longitudinal and lateral acceleration of the vehicle and the ground speed to determine the optimum level of damping. 4 different damping forces can be set at each wheel by controlling the damping valves located at each wheel. Phased in as of 09/00, the damping is set to the Sport 1 damping level if the vehicle speed is >160 km/h.
- Level control and adjustment
- The control module uses the setting of the level adjustment switch selected by the driver and the ground speed of the vehicle to control the appropriate level control valves and to set the correct vehicle level according to the vehicle load.
- The AIRmatic system is equipped with a pressure reservoir to keep the level control time as short as possible (e.g. after loading). The reservoir pressure is used only when required in order to prevent filling the reservoir too often. This happens, for example if the vehicle level falls below a critical level when loading the vehicle or if the driver has set the vehicle level to "raised level". Pressure from the reservoir is also used when the vehicle is stationary to minimize noise. With normal control when the vehicle is moving, the spring struts are supplied directly by the air compressor.
- Main reservoir pressure control
- The main control parameters are the pressure in the main reservoir, the outside air pressure and the vehicle speed.
- Compressor control
- The compressor is controlled via a relay. Since the compressor is not designed for continuous operation, the absolute running time and cooling phase are monitored to avoid overloading the compressor.
- Wake-up function
A parked vehicle is "woken up" before the engine is started. That is to say, the AIRmatic with ADS control module receives signals from the door contact switches, the trunk switch and infrared remote control indicating that the driver may soon start the engine and drive the vehicle. The current vehicle level is checked immediately and corrected if required. The vehicle level at the front axle is considered to be critical, for instance, if the full wheel angle can no longer be guaranteed. In this case a message appears on the multifunction display in the instrument cluster to warn the driver: "Stop car too low". If the control module is woken (for example by opening one of the doors), there follows a period of spare time before the driver actually starts the engine during which the vehicle level is corrected. This reduces the waiting time required to correct the vehicle level and the vehicle is ready for driving more promptly. Pressure in the main reservoir is used to raise the stationary vehicle. The compressor is only used if the pressure reservoir is empty. It must be ensured that the battery voltage is sufficient to then start the engine.
- Locking function
If the control module detects that all wheels are unloaded when the vehicle is stationary, the valves of the spring struts are closed. The vehicle therefore remains at the current level. This is essential, for example, when changing a wheel or during repair work (lifting platform).
Safety circuit
The AIRmatic with ADS control module monitors all the important components of the system after they are switched on and during operation. The safety circuit detects faulty signals from sensors, faults in the control module and in the electric line system. If a fault is detected, the system is switched off and a message is displayed on the multifunction display in the instrument cluster to warn the driver. The damper valves for ADS are no longer controlled and remain set to the "hard" damping level (driving safety level). In addition, a fault code is stored in the control module. The level control is partially switched off depending on the fault that occurred. The system always strives to maintain the selected vehicle level. Moreover, the safety circuit continuously monitors the battery voltage. If the voltage falls below 10.5 V or exceeds 17.5 V, the system is switched off until the voltage returns to the specified range.
Pressure Supply Function
- 42 - AIRmatic Central Reservoir
- A9/1 - AIRmatic Compressor Unit
- Y36/6 - Level Control Valve Unit
In normal driving mode, AIRmatic works with a pressure of between 6 and 10 bar (600 and 1,000 KPa or 87 and 145 psi) depending on the load. An electrical compressor is used to supply pressure. This is installed in the AIRmatic Compressor Unit (A9/1).
In addition the system has an AIRmatic Central Reservoir (42) which stores the compressed-air. The AIRmatic Central Reservoir (42) pressure is between 13 and 16 bar (1,300 and 1,600 KPa or 189 and 232 psi) (at sea level).
The AIRmatic system is either supplied with pressure via the AIRmatic Central Reservoir (42) or via the AIRmatic Compressor Unit (A9/1).
Level Control Function
The AIRmatic at the front and rear axle is a fully supporting suspension system. It keeps the vehicle level constant when the engine is running irrespective of the load. At the same time air from the air compressor is delivered to the spring struts via the valve unit until the vehicle level has been adjusted. The vehicle level at the front axle is recorded by two level sensors at the front axle and conveyed to the AIRmatic with ADS control module. The level at the individual spring struts is controlled by four level valves in the valve unit and a pressure relief valve on the AIRmatic compressor unit.
An AIRmatic central reservoir for compressed air also enables the vehicle level to be controlled when the engine is not running. In addition the adjustment of the vehicle level is decoupled from the air compressor.
Shut-off position function
If the unloading of all the wheels when the vehicle is stationary is recognized by the control module, the spring strut valves are closed. The vehicle therefore remains at the current level. This is required when changing a wheel or for repair work (hoist) for example.
Normal function (engine running)
When the vehicle is stationary the level is readjusted if there is a difference of more than +/- 10 mm after a door or the trunk lid is opened.
While driving the level is readjusted if there is a difference of more than +/- 20 mm. The level is adjusted to +/- 10 mm every 15 minutes.
Depending on the situation, pressure can be generated by the compressor or the pressure supply of the AIRmatic central reservoir can be used to raise the vehicle. When the vehicle is stationary the pressure from the reservoir is used for noise reasons. Pressure can also be supplied from the compressor and AIRmatic central reservoir at the same time when there is a particularly high pressure demand.
The lowering of the vehicle level is recognized by the control module from the level sensors when loading the vehicle. By actuating solenoid valves air is delivered to the spring struts of the particular front wheel or rear axle until the vehicle has reached its specified value. In addition the pressure relief valve is opened to actuate the respective wheel valve when unloading the vehicle.
Wake-up function (operating period approx. 1 minute)
The AIRmatic with ADS control module is "woken up" using the remote control, door contact switches or trunk illumination switch in order to check the current vehicle level for critical conditions (level too low) and if necessary to raise the vehicle or lower it when unloading. If the vehicle level is lowered by more than 30 mm, it is raised to the normal level by the reservoir (only with a reservoir pressure > 11 bar). At a vehicle level of < -65 mm and even at a reservoir pressure of <11 bar it is raised out of the "critical range" by the compressor to -63 mm (condition: battery voltage > 12.4 V).
If the vehicle level is raised by more than 10 mm when unloading, it is lowered to the normal level by relieving the pressure.
The vehicle cannot be raised by the level control switch.
Function in vehicle condition "Ignition ON"
The same function as for the wake-up function, but without time limit.
Run-on function (operating period approx. 1 minute)
After "ignition OFF" the control module performs changes in the level in order to be able to readjust the vehicle level (raise or lower) during any loading or unloading operations. (The same function as for the wake-up function).
Components
![]() |
Location of electrical/electronic components
- A9/1 - AIRmatic compressor unit
- A1p13 - Multifunction display
- B7 - AIRmatic pressure sensor
- B22/3 - Rear axle level sensor
- B22/8 - Left front level sensor
- B22/9 - Right front level sensor
- B24/3 - Left front body acceleration sensor
- B24/4 - Right front body acceleration sensor
- B24/6 - Right rear body acceleration sensor
- K40/7 - Right front fuse and relay module
- kO - AIRmatic compressor relay
- N49 - Steering angle sensor
- N51 - AIRmatic with ADS control module
- N72/1s2 - Level control switch
- N72/1s3 - Comfort and sport switch
- S9/1 - Stop lamp switch
- X11/4 - Data link connector
- Y36/6 - Level control valve unit
- Y51 - Left front axle damping valve unit
- Y52 - Right front axle damping valve unit
- Y53 - Left rear axle damping valve unit
- Y54 - Right rear axle damping valve unit
Location of pneumatic/hydraulic components
- 40 - Front spring strut
- 41 - Rear spring strut
- 42 - AIRmatic central reservoir
- A9/1 - AIRmatic compressor unit
- Y36/6 - Level control valve unit
- Y51 - Left front axle damping valve unit
- Y52 - Right front axle damping valve unit
- Y53 - Left rear axle damping valve unit
- Y54 - Right rear axle damping valve unit
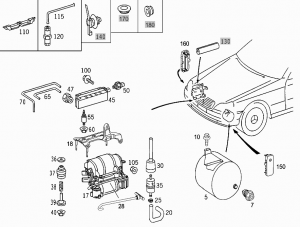
Compressor Relay (K40/7kO)
The Airmatic Compressor Relay (K40/7kO) is located in right fuse box, location 'O' (the first one next to the three 40 amp fuses). The relay starts and stops the Airmatic compressor. A faulty relay may cause the compressor to overheat thus damaging it. Hella relays have proven to be reliable. Part number 4RA 007 791-011 (A0025421319).
![]() |
Compressor Relay Fuse (K40/7f32)
The compressor relay is powered by 40A fuse 32 located in the right fuse box.
![]() |
Compressor Unit (A9/1)
The electric compressor generates the pressure required to lift the vehicle. The pressure relief valve integrated in the AIRmatic Compressor Unit (A9/1) is used to lower the vehicle.
![]() |
![]() |
![]() |
|
Design of Compressor Unit
|
The main part of the AIRmatic Compressor Unit (A9/1) is the compressor motor (m1). The other parts are the pressure relief valve, overpressure/residual pressure valve (b) and the air drier (c).
The air filter/cleaner (a) is located outside the compressor unit. It is connected to the unit by a hose. The air released when the vehicle is lowered is returned to the air filter/cleaner via the line (g) where it is then guided back out through the filter.
The compressor unit is mounted to a mounting plate (h).
The AIRmatic Level Control Valve Unit (Y36/6) is fixed at the top of the same mounting plate as the compressor unit and is connected to the compressor by a pressure line.
The valve unit is attached to the AIRmatic pressure sensor (B7).
Function of AIRmatic Compressor Unit
![]() |
|
The air compressor is driven by the compressor motor (m1). The air to be compressed is sucked out of the vehicle longitudinal member through an air filter/cleaner and into the chamber underneath the piston. With the downward movement of the piston, the air passes through the inlet valve (e) in the piston crown into the clearance volume. With the upward movement of the piston, the inlet valve closes and the air is compressed. The compressed air is forced on via the outlet valve (d) into the air drier (c).
The silicate filling in the drier removes moisture from the air. From the air drier the dehumidified and compressed air then passes from the air drier into the central reservoir or directly to the suspension struts as required.
The pressure relief valve installed in the compressor unit (y1) is required for discharging air when lowering the vehicle. The discharged air is conducted through the air filter/cleaner back into the atmosphere. This also cleans the air filter/cleaner.
The air drier is maintenance free. The moisture is delivered back into the air when reducing the pressure.
Air Filter
It is difficult to get reliable information about the scheduled maintenance interval on the AIRmatic air filter. W220 community recommends to replace the air filter from time to time to prevent damage to the AIRmatic compressor. The filter can fill up with debris and salt which may block the air filter/cleaner. A new AIRmatic air filter costs around EUR 10, and it should not take more than 20 minutes to replace. For replacement method see the DIY compressor and filter replacement instructions below.
The air filter is protected with a protective boot. It may be hard to separate the filter from the rubber grommet housing. The housing may fail when trying to remove it, so make sure you have a replacement housing at hand. Put a dielectric grease on the inside of the housing prior to insertion of the replacement filter to support future removal.
Note: The arrow on the air filter shows the 'UP' direction and not the direction of air flow which is both ways.
|
Air Dryer
Silica gel is used as a desiccant in compressor unit. It works by a process called adsorption. The water in the air actually absorbs between the tiny passages as the air passes through them. The water molecules become trapped so that the air is dried out as it passes through the filter. This process is reversible. If the silica gel desiccant is heated it will release the trapped water. This process is called regenerating the desiccant. Once saturated with water, the gel can be regenerated by heating it to 120 °C (250 °F) for 1–2 hours. However, silica gel degrades after very few cycles if heated to 110°C or more. For maximum longevity dry it at just 80°C. It won't take much longer but will last longer and work just as well as a desiccant.
Once the silica gel gets saturated with water, the moisture will get in the system. Moisture will accelerate oxidation of aluminium parts (e.g., valve block).
Mercedes documentation claims that desiccant used for air drying is maintenance free. However, for the longevity of our vehicles, it is recommended to change the desiccant along with the air filter at some point. There are compressor unit repair kits sold on eBay that come with new dust filters and silica gel filling.
Note: The original silica gel drier beads are multi sized and a volume is calculated (gaps of air between the beads). This volume is impossible to calculate and replicate using aftermarket beads, therefore, it is recommended to dry and refit the original beads as exchanging them for new will lower the compressor flow rate (around 10-15%).
![]() |
![]() |
Electrical connectors
- Power supply - A1685453628 (from compressor relay K40/7kO)
- Pressure release valve - A1685452928 (from AIRmatic control module N51)
Level Control Valve Unit (Y36/6)
Located on the AIRmatic Compressor Unit in the right front fender, the Level Control Valve Unit (Y36/6) is the central control unit for the level control, level adjustment and suspension. It supplies the AIRmatic front and rear spring struts (40, 41) and the AIRmatic Central Reservoir (42) with compressed-air.
The Level Control Valve Unit (Y36/6) is commonly referred to as the "valve block".
Parts
It is a common fault for the valve block to fail open. A new valve block unit (A2203200258) costs around EUR 290. In case of o-ring failure, they can be replaced (see the valve block o-ring repair kits available in the section below). Cheap Chinese clones made of plastic are available on Aliexpress, but in our experience they started to leak in less than a year of operation and the lifetime of the pressure sensor is around two years.
![]() |
![]() |
![]() |
Miessler Automotive has created after-market valve block (EUR 200) claiming to have better quality than the original, i.e., being absolutely weatherproof without the risk of corrosion as the original.
![]() |
![]() |
Design of Level Control Valve Unit (Y36/6)
The AIRmatic Level Control Valve Unit (Y36/6) is attached to the same retaining plate as the AIRmatic Compressor Unit (A9/1). It has a solenoid valve for each wheel (y1, y2, y3 and y4) for raising or lowering the vehicle. The AIRmatic central reservoir charge (y5) is also installed in the valve unit. The AIRmatic pressure sensor (B7) is located on the end face of the valve unit.
Function of Level Control Valve Unit
For reasons of safety only one valve is ever actuated at the same time. If an axle is too low, cycling takes place between the left and right level valve.
Raising the vehicle
The front left, front right, rear left and rear right level valves (y1, y2, y3, y4) are opened as required and the compressed-air stored in the central reservoir or generated by the air compressor motor flows from the level control valve unit (Y36/6) to the individual spring struts.
As soon as the required vehicle level is reached at a front wheel, the respective level valve (y1 or y2) closes, the other valve still remains open until the same vehicle level has also been adjusted at the other wheel.
At the rear axle both level control valves (y3 and y4) close when the vehicle level averaged between the right and left wheel corresponds to the specified level set by the control module.
Lowering the vehicle
All the wheel level control valves (y1, y2, y3 and y4) are open in the level control valve unit (Y36/6).
In addition the AIRmatic pressure release valve (y1) in the AIRmatic compressor unit (A9/1) is open and the compressed-air is reduced via this valve.
At the same time the level valves of the individual wheels remain open until the desired vehicle level is reached at each front wheel and at the rear axle.
AIRmatic Pressure Sensor (B7)
The AIRmatic Pressure Sensor (B7) is located in the right front fender on the AIRmatic Level Control Valve Unit. It measures the system pressure and is used to carry out plausibility checks.
![]() |
![]() |
Function of Pressure Sensor (B7)
A sensor element compares the fluid pressure (b) to be measured with a reference pressure (g) in the sensor. The pressure (b) is transmitted to the actual sensor element (h) by means of a metal protective diaphragm (k) and a silicone oil layer (i).
An electronics module (a) which supplies the pressure signal in the form of an analog voltage to the control module, is located on the metal housing (d).
Parts
Pressure sensor is part of the valve block, but in case of a pressure sensor failure, the pressure sensor can be unscrewed (using 27mm wrench) from the valve block and replaced separately.
- OE: A2205420118
- THERMOTEC KTT130043 (20 EUR)
- NRF 38953 (20 EUR)
- MAXGEAR AC186345 (20 EUR)
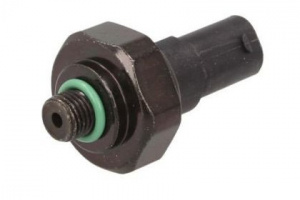
Level Sensor (B22/3, B22/8, B22/9)
The Level Sensor (1) function is to detect the vehicle height at the front axle and rear axle and supply the values to the AIRmatic with ADS control module.
The Level Sensor works by detecting the vehicle height using a link rod from upper transverse control arm at left and right front axle. A sensor at the rear axle monitors the movement of the torsion bar and determines the average vehicle height.
![]() |
![]() |
![]() |
The Level Sensors consist of two Hall Effect sensors in a single housing which produce two signals (redundant design).
Sensor failure is detected by comparing the two redundant signals of each sensor.
Level Sensor Identification
- B22/3 - Rear axle level sensor
- B22/8 - Left front level sensor
- B22/9 - Right front level sensor
Part Numbers:
- All 3 sensors have the same part number A0105427617 (EUR 150 OE, EUR 70 aftermarket) or A0105427717 (for vehicle with ABC suspension).
- Link for rear level sensor A2203200032 (EUR 40).
![]() |
![]() |
![]() |
A common fault is rust on the link of the rear level sensor. The link can be fixed or even self-made.
![]() |
![]() |
Part Numbers:
- Link (rod) for front left/right level sensor A2203200389 (EUR 28)
- Sensor bracket front left - A2203270840 (EUR 70)
- Sensor bracket front right - A2203270940 (EUR 70)
![]() |
![]() |
![]() |
AIRmatic Central Reservoir (42)
Metal compressed air reservoir. Stores compressed air for level control. Used for decoupling between compressor and level control.
![]() |
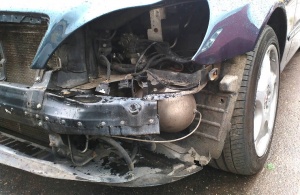
Comfort and sport switch (N72/1s3)
This switch controls Adaptive Damping System (ADS).
The switch with the indicator lamps is located in the upper part of the center console.
![]() |
![]() |
![]() |
The ADS automatically selects the optimum damping for the respective driving conditions. At the same time the suspension is set to either sporty or regular.
The suspension tuning is set according to:
- Your driving style
- Road surface conditions
- Your choice of suspension style, "sport" or "convenience", which you select using the damping switch.
The following suspension styles are available:
- "Convenience" - both indicator lamps (1) are off.
- "Sports 1" - one indicator lamp (1) is on.
- "Sports 2" - both indicator lamps (1) are on (on vehicles produced after 09/99).
The selected suspension style is stored in memory, even after the SmartKey is removed from the starter switch.
Level Control Switch (N72/1s2)
![]() |
![]() |
This switch controls AIRmatic Level Control System.
The following vehicle level settings can be selected when the vehicle is stationary:
- "Normal" - for driving on normal roads. The indicator lamp (1) is off.
- "Raised" - for driving on rough roads or with snow chains. The indicator lamp (1) is on.
Select the "Raised" level setting only when required by current driving conditions. Otherwise the fuel consumption may increase and handling may be impaired.
The vehicle chassis ride height is raised or lowered according to the selected level setting and to the vehicle speed (these height adjustments are so small that you may not notice any change):
- With increasing speed, ride height is reduced by up to approximately 3/4 in (20 mm).
- With decreasing speed, the ride height is again raised to the selected vehicle level.
The selected vehicle level setting remains stored in memory even if the engine is turned off and restarted. However, the vehicle lowers to regular level when you exceed a speed of 75 mph (120 km/h) or maintain a speed of between 50 mph (80 km/h) and 75 mph (120 km/h) for more than 5 minutes.
This can be used to raise the vehicle level by 25 mm (20 mm USA). The raised level switch position is indicated by the red indicator lamp (1) in the switch. In addition, the multifunction display in the instrument cluster displays: "AIRMATIC VEHICLE RISING".
![]() |
As long as the multifunction display in the instrument cluster shows the message: "AIRMATIC VEHICLE RISING", the desired vehicle level has not yet been reached. If the raising of the vehicle is cancelled due to the driving speed, the instrument cluster displays the following message for approx. 10s: "AIRMATIC LEVEL SETTING CANCELLED". If the vehicle is raised several times in quick succession, it may happen that the air compressor shuts down temporarily in order to prevent an overload. The raising sequence will then take an unusually long time.
AIRmatic with ADS Control Module (N51)
AIRmatic with ADS Control Module (N51) is located in left fuse box. Its task is to execute all control functions of ADS and AIRmatic.
![]() |
![]() |
![]() |
The AIRmatic with ADS Control Module (N51) receives input signals over CAN Bus from the following components:
- ESP control module
- Engine control module
- Transmission control module
- Instrument cluster
- Steering angle sensor
- ADS comfort and sport switch
- Level adjustment switch
- Three body accelerometers
- Two front axle level sensors
- One rear axle level sensor
- One Airmatic pressure sensor
The input signals are converted in the AIRmatic with ADS Control Module (N51) to output signals for the following components:
- Four Level control valves
- One main reservoir charge valve
- Four ADS damper valves
- Multi-function display
- Switch indicator lamps
- Air compressor
AIRmatic Suspension Spring Strut (40, 41)
The Air Suspension Spring Strut takes over all the functions of suspension, level control, level adjustment and damping to be carried out.
![]() |
![]() |
![]() |
Design of Air Suspension Spring Struts (40, 41)
A single-tube gas-filled damper unit or shock absorber is integrated into the air spring strut. A residual pressure valve is incorporated into the inlet fitting on the top of each air spring strut.
Design of Front Axle Spring Strut (40)
The Front axle air spring strut (40) consists of three main systems:
- Dust cover and protective boot called a bellows
- Air spring (strut top, residual pressure holding valve (k), seals, air bag/bladder (h) , strut tube (a))
- Gas pressurized damper or single-tube gas-filled shock absorber.
The coponents of the front axle spring strut are shown in the figures below. The air spring plunger is item 8 in the figure. It is the conical flared lower end of the protective boot or bellows. The air spring plunger fits over the support bushing which is the conical seat or item 9 on the damper unit.
![]() |
Front struts on W220s up to about 2004 did not have epoxy installed at the factory. Also many of the older style front strut have now been modified with mastic or epoxy added. Note: The epoxy is not the seal for the upper strut. It is a vibration damper to help the narrow neck of the brass valve at the top of the strut avoid cracking and leaking due to vibration. If you have a leak in this older style front strut there is a kit you can buy to fix the leak (top seal repair kit A2203202538, see below). Scraping out the old black epoxy and filling it back in will not fix this. The part that leaks is a half metal and rubber cap under the black epoxy and is secured with a metal lock ring. The newer seals have rubber mastic compound poured in the center to seal the circumference of the upper metal cap on the upper part of the front strut and to keep the brass fitting from breaking off.
![]() |
![]() |
![]() |
Operation of Air Spring Struts (40, 41)
- When filled with air, the rubber air bag or bladder (h) rolls up and down the alloy lower section strut tube (a).
- The strut tube (a) is covered by a protective boot or bellows.
- Without air and under load the protective boot or bellows is allowed to kink and crease and the air bag or bladder would also have the top pressed hard into the inside of the air chamber (l).
- The only sliding action is in the strut damper unit which is oil filled and gas pressurized.
Function of Air Spring Struts (40, 41)
The weight of the vehicle is carried by the compressible air (l) sealed into the air bag or bladder of the air springs. The rolling air bag or bladder (h) is made of rubber. Under dynamic load during driving, the air bag or bladder (h) rolls up parallel with the axis of the spring strut, thus providing the necessary spring travel. The roll-up zone on the air spring strut is sealed off from the outside by a rubber protective boot or bellows (n) as a protection against dirt.
The vehicle level is raised/lowered by increasing/reducing the air pressure in the air chamber (l), which results in a lengthening/shortening of the air spring strut (40).
Residual Pressure Holding Valve (k)
Each air spring strut incorporates a residual pressure holding valve (k) which blocks off the air spring pressure chamber from the supply line in the event of a pressure drop at or below a residual pressure of 4-5 bar.
Parts (Spring Strut)
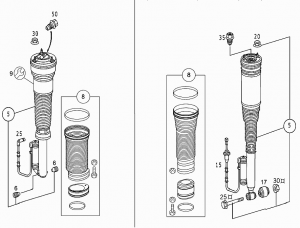
OE:
Front (without 4MATIC):
- A2203205113 (replaced by A2203202438)
- A2203202438
Front (4MATIC):
- Left: A2203202138
- Right: A2203202238
Rear:
- A2203205013
- A2203207913 (for option code Z04)
- A2203207813 (for option code Z07) (replaced by A2203202338)
- A2203202338 (for option code Z07)
OEM (Bilstein):
Since Bilstein is OE manufacturer for W220 AIRmatic struts, it is possible to buy OE struts directly from Bilstein much cheaper. It is possible to purchase a brand new Bilstein strut for about EUR 700.
- Front left (4Matic): 44-051518
- Front right (4Matic): 44-051525
- Front: 44-042295
- Rear: 44-042301
Miessler Automotive
Miessler Automotive sells new struts having the same features as the OEM.
- Front: FBN0-002S-4229
- Rear: FBN0-002S-4230
- Front right (4Matic): FBN0-002S-2238
- Front left (4Matic): FBN0-002S-2138
Arnott:
Arnott sells both new and remanufactured AIRmatic struts. It is possible to get 10% discount [1] when making an order online.
Arnott claims [2] that their products use an improved double thickness air spring bag/bladder manufactured by Continental which provides longer lifetime than the OE.
In fact, Arnott provides limited lifetime warranty [3] for their AIRmatic Air Suspension Struts.
- Arnott Remanufactured. An Arnott remanufactured AIRmatic strut costs about US$575, but note that it only has installed a new rubber air bags/bladders and not the shock piston seals or gas charge.
- Arnott New. Arnott new Air Spring Struts cost about US$624.
Note that with all new Arnott AIRmatic struts you lose the electronic damping feature. While the new Arnott struts allow to plug in the original wire harness from the car, it simply fools the AIRmatic computer in to thinking the selective damping is functioning. In reality it is not and the shock has constant damping setting corresponding to OE "comfort/convenience" setting ("sport 1" and "sport 2" damping settings are not available).
![]() |
![]() |
Mechanical springs:
A mechanical spring version of the complete suspension strut which eliminates the pneumatic parts can be bought from Strut masters. This requires both sides to be replaced as a minimum, and possibly all four wheels should be done together. This method uses clever electronic components to "trick" the W220 computers into sensing that an AIRmatic is actually installed so that error messages are not displayed. The BIG disadvantage is the loss of air suspension ride quality, automatic leveling and damping options. In some countries such modified cars will not pass annual technical inspection.
Adaptive Damping System (ADS II)
Function of Adaptive Damping System (ADS II)
The Adaptive Damping System (ADS II) via the Damping Valve Unit (Y51, Y52, Y53, Y54) adapts the damping force to the driving style and road condition. The damping force is regulated in damping valves (Y51, Y52, Y53, Y54). Each wheel has one damping valve installed between the upper and lower chambers of the single-pipe gas-filled shock absorber.
Each damping valve contains two electromagnetic valves (y1, y2), allowing four different damping force settings according to how they are actuated via the AIRmatic with ADS control module.
The extremely short adjusting time (milliseconds) means that the optimum damping force setting is available almost immediately if sudden changes in the vehicle level are required, such as during an obstacle-avoidance maneuver.
![]() |
![]() |
![]() |
Design of Damping Valve Unit (Y51, Y52, Y53, Y54)
- Y51 - left front axle damping valve
- y1 - front axle solenoid valve 1
- y2 - front axle solenoid valve 2
- p - piston reed valve pack
The Damping Valve Unit (Y51, Y52, Y53, Y54) consists of a casing and 2-piston reed valve packs (p). Located above are the spring-loaded solenoid valve pistons and the solenoids. The valve pistons and solenoids form the solenoid valve units (y1, y2).
If the solenoid valve coils (y1, y2) are not actuated, the spring-loaded solenoid valve pistons (y1, y2) keep the holes directly below them closed. Oil is displaced via the reed valve packs (p) and the oil duct located diagonally opposite in the casing.
If the solenoid valve coil (y1) is actuated, for example, the solenoid valve piston (y1) allows the hole to open and the oil can flow over this hole. Only a small amount of oil is displaced via the piston reed valve pack (p). The damping force levels are achieved by means of the differently positioned reed valve packs and controlling the solenoid valves.
Components of Damping Valve Unit (Y51, Y52, Y53, Y54)
Force Settings
The ADS suspension control module is used to achieve four different damping force settings:
- Damping force setting 1
- For comfortable rolling with small sprung mass vibrations and low longitudinal and lateral acceleration. With this damping force setting both solenoid valves y1 and y2 are open so that most of the oil flows parallel to the hard rebound and compression of the operating piston via the softer reed valves at the solenoid valves. The comfort rebound and compression setting is therefore achieved.
- Damping force setting 2
- The reed valves at the valve piston generate a firmer setting. If the vehicle is lowered, solenoid valve y2 is opened and solenoid valve y1 is closed. The reed valves (a = hard compression and b = soft rebound) at solenoid valve y1 generate a hard compression and a soft rebound.
- Damping force setting 3
- The reed valves at the valve piston generate an even firmer setting. If the vehicle is raised, solenoid valve y1 is opened and solenoid valve y2 is closed. The reed valves (c = hard rebound and b = soft compression) at solenoid valve y2 generate a hard rebound and a soft compression.
- Damping force setting 4 (driving safety setting)
- For increased driving safety with high longitudinal and lateral vehicle acceleration. Both solenoid valves y1 and y2 are closed. The reed valves (a = hard compression and c = hard rebound) generate a hard compression and rebound. All the oil flows via the hard rebound and compression of the operating piston. This damping force setting is also selected if the ADS system fails and the ADS suspension warning light (A1e27) comes on in the instrument cluster.
Damping force setting | Damping valves (Y51-Y54) | Valve control | ||
---|---|---|---|---|
Rebound | Compression | Solenoid valve (y1) | Solenoid valve (y2) | |
1 | Comfort | Comfort | Open | Open |
2 | Soft | Hard | Closed | Open |
3 | Hard | Soft | Open | Closed |
4 | Hard | Hard | Closed | Closed |
The "Actuations" menu under the AIRmatic control module in DAS can be used to force a damping setting for a particular strut regardless of the ride conditions. The "Development data" menu (in German) can be used to force damping setting for all struts (F3 - the hardest setting, F6 - the softest setting).
![]() |
![]() |
Multifunction display (A1p13)
Various messages concerning the AIRmatic and ADS are shown in the multifunction display in the instrument cluster and in the comfort and sport and level adjustment switches.
AIRMATIC VISIT WORKSHOP!
In the event of electrical faults in the AIRmatic or ADS system, the following message appears on the multifunction display in the instrument cluster: "AIRMATIC VISIT WORKSHOP!".
The fault is stored in the ADS suspension control module and can be read out using the diagnosis tool.
![]() |
![]() |
Limp-home Function
A malfunction in the adaptive damping system causes the ADS to shut down. The suspension is switched to the hardest setting. In the event of a fault in the suspension system or in the level adjustment system, the vehicle attempts to maintain the set level. Manual and automatic level adjustments are no longer possible.
AIRMATIC STOP, CAR TOO LOW!
If the vehicle level at the front axle is more than 50 mm (60 mm USA), or at the rear axle more than 60 mm (70 mm USA) below the normal level, the multifunction display in the instrument cluster displays the warning: "AIRMATIC STOP, CAR TOO LOW!".
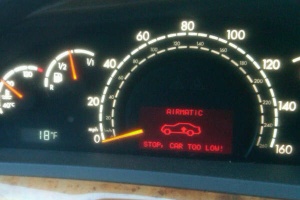
The display disappears again when the level has risen back to 48 mm or 58 mm (58 mm or 68 mm USA) respectively below the normal level.
Issues and Troubleshooting
Note: If the AIRmatic leaks substantially it is imperative that it be fixed as soon as possible or else the AIRmatic pump may burn out. If the leak cannot be fixed immediately remove the AIRmatic compressor relay (K40/7kO) to disable the AIRmatic Pump. For the relay and fuse locations see above. However BE WARNED, the vehicle may leak enough to be not drivable when turning the front wheels causes them to touch the top of the wheel arch (for 18" wheels and larger).
"AIRMATIC VISIT WORKSHOP!" message on the instrument cluster
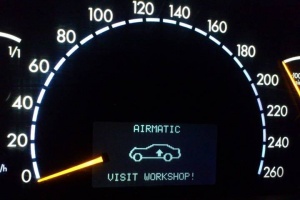
This message is shown in the event of electrical faults in the AIRmatic or ADS system. Use DAS to read error codes.
Error Code | Description | Probable cause |
---|---|---|
C1324-001 | Fault in component Y53y1 (Left rear solenoid valve 1) in assembly Y53 (left rear axle damping valve unit) | Could be caused by faulty solenoid valve in the strut in which case the strut or strut's damping valve unit should be replaced.
If the error code comes in pair with second selenoid valve of the strut then the problem is very likely in the connection. Check the electronic connection between the strut and AIRmatic with ADS control module (N51). |
C1325-001 | Fault in component Y53y2 (Left rear solenoid valve 2) in assembly Y53 (left rear axle damping valve unit) | See above. |
C1517-128 | Suspension strut is implausible. | This error code is shown when the AIRmatic system supplies or releases air from the strut, but does not observe the intended effect (likely level sensor or pressure sensor does not show the expected result). For example, it has been reported to appear in case where hoses on the valve block were mixed up. The AIRmatic system thought that it is pumping air in reservoir, but actually the air was passed to strut (and vice versa). |
"AIRMATIC STOP, CAR TOO LOW!" message on the instrument cluster
![]() |
![]() |
Vehicle Level Too Low
Most common reason for a car being too low is a leaking strut. The strut itself has a residual pressure holding valve which is designed to stop air escaping out of the strut once the internal pressure drops below a residual pressure of 4-5 bar.
Note: the same symptoms as a leaking strut can be experienced if the line to the strut is faulty or the valve block is faulty (see section "Level Control Valve Unit Leaking" and "Inspecting AIRmatic Level Control Valve Unit (Y36/6) for leaks"), so be sure to eliminate these causes before replacing a strut.
Air Bag/Bladder Leaking
Usually the the most common source of a leaking strut is a failed rubber Air Bag/Bladder (h).
Failure is caused by the Air Spring Air Bag/Bladder (h) chafing against the protective alloy dust cover over time. The original Air Bag/Bladder (h) is made from a very thin single nylon cord layer, and vertical weak spots or lines will develop and eventually pop through, causing a complete failure.
![]() |
![]() |
![]() |
Unlike the OE Air Bag/Bladder, re-manufactured ones usually use two ply rubber design that prevents vertical wear points and the Air Bag/Bladder is usually over two times thicker than the original one.
It is possible to replace a damaged Air Bag/Bladder (h), however, the rubber Air Bag/Bladder is attached to the strut tube and strut top with crimp rings. This requires access to an hydraulic crimper, which is not easily available for a DIYer.
Fortunately, it is possible to purchase on eBay a refurbished Air Spring which is the top part of an air suspension strut for around EUR 120 and mount it to the original damper unit (the lower part of an air suspension strut).
![]() |
![]() |
This requires the Strut to be removed from the car and the Air Spring to be separated from the Damper unit by partly dismantling the Air Spring. For the DIY Procedure see section "Replacing the Air Spring in an AIRmatic Strut".
If the leak is severe, a hissing sound can be heard from the wheel house area.
A faulty strut can often be located visually by observing the relative heights of each corner of the vehicle, but be aware that it is very likely that the wheel on the other side (or the wheel on other axle on the same side) will also be brought down significantly, but usually to a smaller extent.
To be thorough, an objective test is best performed.
- Ensure the vehicle is parked on a level surface.
- Measure the height at each corner of the vehicle and record the results.
Height Measuring Technique
Use a tape measure to measure from underneath the edge of a wheel arch to the centre of the M-B Star Logo in the wheel hub cap. This technique removes variations caused by tyre pressures.
![]() |
![]() |
![]() |
- Do not disturb the vehicle for 10 hours. (Ensure the car remains "asleep" during this time.)
- Re-measure the height at each wheel and record the results.
- Calculate the drop at each wheel and compare with the specification.
M-B DAS states the drop in vehicle height must be less than 20mm (30mm in very cold conditions) in 10 hours, ie less than 2mm per hour is allowed.
Top Seals Leaking
The seals at the tops of the front suspension struts develop leaks. This issue was more common with the older design in the pre '03-ish W220's compared to those from a few years later. There is available an epoxy repair kit that can be used to close the cracks. A professional repair costs around US$550 parts and labor for both sides.
Note the newer W220's post '03 and ones which have been modified with new replacement parts do not leak at the top seal which is an 'O' ring around the metal cover disc. The top of the air suspension strut on these later models is filled with a butyl mastic compound to reduce vibration on the residual valve inlet connection.
![]() |
![]() |
Repair Options for AIRmatic Air Suspension Strut
If any AIRmatic Air Suspension Struts, Front axle (40) or Rear axle (41) need complete replacement, see the part numbers and replacement options.
![]() |
![]() |
For the DIY Procedures see the sections below.
Replacement AIRmatic Front Axle and Rear Axle Air Springs are also available and can be installed with the original damping unit (see sections below).
![]() |
![]() |
AIRmatic Compressor Unit Failure
AIRmatic Compressor Unit (A9/1) failure or partial failure. To test this hypothesis start the car and see if compressor is running (you should hear compressor in the front right fender running).
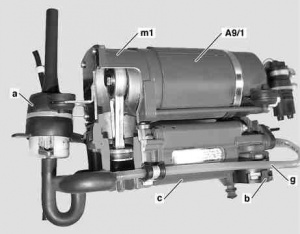
If it is not running, check AIRmatic Fuse and relay (see above). A faulty relay may cause compressor to run nonstop which will cause compressor to overheat and blow out the fuse.
Pressure Lines Leaking
The high-pressure line from the AIRmatic Compressor Unit (A9/1) to the AIRmatic Level Control Valve Unit (Y36/6) develops a leak. In this case replacement line or a repair joiner can be used.
It is possible that the pressure line to the strut develops cracks or micro cracks.
In case of front struts the line from valve block to strut can be tested with spray test.
However, in case of rear struts the line goes from the valve block to rear through interior and thus is not reachable. A simple test is to run an alternative line from the valve block to the strut to check if the original line is faulty (see the section on the line repair).
If the crack is large it may suffice to push air in the line and locate damaged point by hearing hissing sound.
Level Control Valve Unit Leaking
The AIRmatic Level Control Valve Unit (Y36/6) or valve block on top of the AIRmatic Compressor Unit (A9/1) fails (very common) and fails to close some valve.
In this case the pressure will be released back to air compressor and out of the system.
For how to inspect valve block for leaks see the section "Inspecting level control valve unit (Y36/6) for leaks".
Usually, in case of valve block leak the vehicle will not be completely down, since the residual pressure holding valve at the air inlet to the struts will prevent the pressure dropping below a pressure of 4-5 bar.

Central Reservoir Leaking
To test whether central reservoir can keep pressure DAS can be used which has a pressure test for reservoir.
If test shows that reservoir cannot keep the pressure, before replacing it, check with leak detector solution to test if the line to reservoir is faulty.
Level Sensor Faulty
There are two level sensors (B22/3, B22/8) for each front wheel and one for the rear axle (B22/9).
![]() |
![]() |
If the level sensor reports wrong height the system will think that vehicle already has the required level and will not raise the vehicle.
Information reported by level sensors can be viewed using DAS.
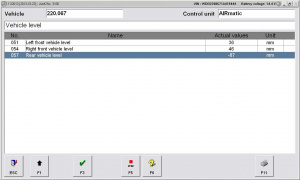
If the vehicle rises, but then falls down again, the level sensors are likely not the cause. If the vehicle is low, but there is no red error message in the instrument cluster about the vehicle level being to low, the level sensor (or its linkage) is at fault.
Vehicle Level Too High
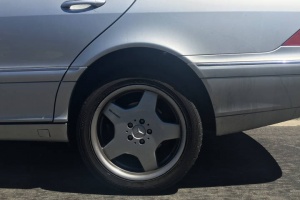
Level Control Valve Unit Leaking
It is possible that Level Control Valve Unit (Y36/6) fails to close some valves in which case the pressure will be released back to strut raising the car too high.
The vehicle will be high only while the car is off, since as soon as vehicle is started the computer will try to adjust the level to the programmed level.
Compressor Unit Release Valve Stuck
When Airmatic ECU decides to lower the vehicle, the corresponding valve in the valve block is opened to release the air out of the system. The air is released through the always-open port P on the valve block. The compressor unit has electrically operated overpressure/residual pressure valve built in the unit. If this valve is stuck, the air will not be released out of system even if ECU sends the electrical signal to release valve built in the compressor unit.
The problem can be as trivial as broken connector. Usually instrument cluster will show malfunction and AIRmatic control unit will report an error:
Error Code | Description | Probable cause |
---|---|---|
C1338-001 | Fault in component A9/1y1 (AIRmatic pressure release valve) | Broken connector (A1685452928) |
Level Sensor Failure
There are two level sensors for each front wheel and one for the rear axle.
If the level sensor reports wrong height the system will think that vehicle level is too low and will rise the vehicle above normal height.
Information reported by level sensors can be viewed using DAS.
Protective Boot/Bellows Failure
On older and higher mileage vehicles the lower dust cover on an AIRmatic air suspension strut starts to wear and fail. This plastic protective boot/bellows is designed to prevent dirt and contamination getting to the air spring bag/bladder. After around 100,000 miles (130,000Kms) they often show signs of cracking and tearing. Failure to replace means the end is near for the whole strut.
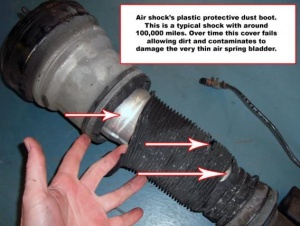
Upper Mount Rubber Bush Failure
A bumping or knocking noise coming from the top of the front suspension may indicate a worn upper mount rubber bushing in the Air Spring.
When the Air Springs were manufactured the upper mount rubber bushings were installed compressed. As the mounts weaken with age they can lose their compression and cause a bumping sound.
The image below shows a typical worn upper mount rubber bushing removed from an AIRmatic air suspension strut with around 80,000 to 100,000 miles (130,000KM to 161,000Km). A worn mount will also contribute to many unwanted problems with your air suspension.
![]() |
Note the Upper Mount Rubber Bushing can be replaced without removing the strut for the car. Do the first steps as shown in the procedure described in section "Dismantling Front Air Spring".
It appears from inspection of the exploded diagrams for the AIRmatic front and rear struts that the upper mount rubber bush may be identical for the front and rear struts. NOTE This is yet to be confirmed.
Individual W220 Upper Mount Rubber Bushings are not readily available. Only available in lots of 5 on Ali Express [4].
Emergency Procedure
In case of "AIRMATIC STOP, CAR TOO LOW!" warning on the instrument cluster, the vehicle should be stopped immediately and measures taken.
Possible consequences of riding with leaky strut:
- The compressor will run endlessly which may cause compressor burnout.
- If 18" or larger wheels are fitted, the tire will rub the inner fender.
- There is a risk of damaging other strut on the same axis.
There is a temporary fix for front struts, which can be used to get to the closest workshop:
![]() |
![]() |
![]() |
![]() |
The ride will be little bumpy, but not much harsher than it is when pushing the button that stiffens the suspension.
WARNING: Travelling long distances or over excessively bumpy roads with this temporary fix using a block of wood will damage the Transverse Control Arm Top (Upper Control Arm (UCA)).
Note the much better location of the M-B limp-home buffer A2203271230 (1a) below which puts all the force over the ball joint and not the arm of the UCA.
Original M-B limp-home buffers
![]() |
|
Front axle:
Mount limp-home buffer A2203271230 (1a) onto upper transverse control arm (6). Slowly lower vehicle and make sure that the limp-home buffer makes contact with top of wheelhouse.
Ŗear axle:
Slide limp-home buffer A2203280839 (1b) in between body fold and torsion bar (77). The body fold must lie in the groove of the limp-home buffer. Slowly lower vehicle and make sure that the torsion bar (77) makes contact with the limp-home buffer (1b).
![]() |
![]() |
![]() |
DIY tips
- Depressurise AIRmatic components (suspension struts, valve unit, reservoir unit) before removal using STAR Diagnosis. WIS states that components or the entire system must NOT be discharged by unscrewing pressure line connectors although most DIYers have done this without problems. Just be sure to open any pressure line connections slowly to avoid a sudden loss of pressure.
- Soiled pressure line connectors must be cleaned before unscrewing.
- Mark the Level Control Valve Unit (Y36/6) with the colours of the air lines BEFORE removing them to avoid having to look up line and port designations.
- Seal off the exposed pressure line ports immediately with blind plugs if possible. A piece of masking tape over the holes is a short term solution.
- Seal off the pressure lines immediately to keep clean by placing the exposed ends in small plastic bags sealed with tape.
- WIS states you must only use flare nut wrenches or special tools to unscrew the pressure lines, however most DIYers have used 10mm open ended spanners successfully. Just be careful to not round the hex head.
- Use a high temperature silicon grease such as Permatex 22058 Dielectric Tune-Up Grease to lubricate high pressure pipes, threads and O-rings. It is also a good idea to apply a small quantity of dielectric grease to any electrical plugs and sockets when re-installing them. This helps keep air and moisture away and stops corrosion. It also makes it infinitely easier to remove the connections next time.
- Make sure to do a thorough leak test after reassembling any high pressure air line connection as the O-ring is easily damaged. A very strong mix of household dish washing liquid detergent and water will act as a leak detector. Another good leak detector solution is Party Bubble Mix. It is best to paint the solution on rather than spray it which creates heaps of unnecessary bubbles. Inspect the wet connection as the bubbles caused by a cracked O-ring can be small and may develop very slowly. Failure to detect the damaged O-ring in the next figure cost the author two new rear struts as it was the O-ring slowly leaking and NOT one of the struts as was mistakenly diagnosed.
- Replacing one stut at a time is possible as long as the valve block has no problems. The valve block has a valve for each strut supply pipe and if the valves remain closed then no air will leak from the other struts whilst one strut is off. But be warned, if the valve block is faulty then any of the struts could loose air after releasing the supply line from a strut.
- The Allen head Stub Screws holding the bottom of the front strut use Loctite thread fastener so a little heat from a gas torch always does the trick in breaking the sealant.
- Do not fully remove the Stub Screw, just unscrew them so that about five threads are showing. It is very easy to damage the threads when reinstalling.
- When reinstalling a strut ensure that the plug at the electrical connection is pressed home firmly. TIP: Re-read the tip re Dielectric Tune-Up Grease and electrical connections. If the plug and socket have been cleaned and lubricated you should hear an audible 'click' when the connector is pushed fully home.
DIY Repairs
Before attempting any DIY repairs make sure to read the tips section above.
Testing strut for leaks
It is common to misdiagnose leaking valve block or line to the strut with leaking strut. Before replacing the strut, the leak should be verified by directly pumping the air to the strut and observing if the strut loses the air.
For this purpose a strut bypass valve below can be used. Pumping the strut requires to provide up to 10 BAR pressure. The usual Chinese 12v car tyre air compressors will fail long before that. We have achieved good success using Alca 227000 2-Cylinder 12v compressor.
![]() ![]() |
![]() |
Parts needed:
- G1/8" Schrader valve (EUR 1)
- G1/8" pneumatic fitting for 2.5*4mm pipe (EUR 1)
- Pipe 2.5*4mm 10m (EUR 6)
- MB connector A0003270369 (EUR 4)
- Compressor able to push 10 BAR at least
Inspecting AIRmatic Level Control Valve Unit (Y36/6) for leaks
Here's how to do a general leak test which will uncover most of the problems caused by faulty valve block.
On the right-hand side of the vehicle remove the wheel and part of the wheel house inner panel in front fender.
- Paint or spray the pressure line connections 1, 2, 3, 4, 5, P of the level control valve with leak detecting solution.
- Inspect for an indication of leaking. Severe leaks are evident immediately. Minor leaks can develop very slowly so be patient.
- The leak can come also from the body of the valve block (valve block is glued together from two parts).
- Wait for approx. 10-15 minutes after applying the solution and reinspect. This means that minor leaks can be recognized (forming a white cap).
![]() |
![]() |
![]() |
Common failure mode of the level control valve unit (Y36/6) is when some valves fail to close thus releasing the air out of system through the compressor-controlled port 'P' or through other valves back to struts.
To test for a leak in any valves of the valve block:
- Make sure that all valves are under pressure (struts and reservoir have pressure in them).
- Detach the connector of 'P' port and spray the port with leak detection spray. Alternatively the 'P' line can be disconnected at the air compressor end and immersed in a soapy solution (see below).
- After the test use compressed air to clean the valve.
Leak Testing Using STAR Diagnosis System (SDS) or Diagnosis Assistance System (DAS)
According to WIS, STAR Diagnosis System (SDS) offers an easy and thorough method for testing the AIRmatic. However, be warned that a very small leak caused by a cracked or damaged O-ring on one of the air line connectors may still pass the SDS AIRmatic Pneumatic Tests.
Using SDS navigate to AIRmatic Pneumatic Tests.
The following tests are available;
- A9/1 Compressor Test
- Y36/6y1 Left Front Strut Test
- Y36/6y2 Right Front Strut Test
- Y36/6y3 Left Rear Strut Test
- Y36/6y4 Right Rear Strut Test
- A9/1y1 Pressure Relief Valve Test
- Leak test between compressor and valve block (line between compressor and 'P' port in valve block).
- Leak test between valve block and suspension struts.
- Leak test between valve block and central reservoir.
- As an example this last test does the following;
- Central reservoir charge valve (in valve block) is opened.
- All other valves (in valve block) are closed.
- Compressor is turned on for <60 secs.
- Compressor is turned off.
- Compressor keeps the line to 'P' port (in valve block) closed.
- Central reservoir pressure is monitored for leakage for 120 secs.
- The Central reservoir pressure must not drop by more than 0.5 bar in that time.
- As an example this last test does the following;
1. Leak test between compressor and valve block (line between compressor and 'P' port in valve block).
As an example, the following result was obtained for a leak test for a FAULTY 'P' line to Level Control Valve Unit (Y36/6) or Valve Block. This is similar to the test using soapy solution.
- After all valve block valves were closed the compressor produced 10.56 bar within 10 secs which is INSIDE the specification of 10 bar within 40 secs.
- After the compressor was turned off the initial compressor pressure ('P' line) = 10.56 bar.
- After the 120 elapsed time the final compressor pressure ('P' line) = 5.30 bar.
- Thus the measured leakage rate was 5.26 bar in 120 secs which is OUTSIDE the specified 0.5 bar in 120 secs.
- SDS reported that there was a leakage in the valve block or the high pressure line between the compressor and the valve block ('P' port).
A squirt of some soapy solution on the high pressure line between the compressor and the valve block proved that the line and its associated connectors were not leaking. Thus the fault was a leak in the valve block. Once the 'P' port connector was removed from the valve block, a simple test by applying a soapy finger over the port produced obvious positive pressure of air escaping from the port, thus confirming the diagnosis of a leaky valve in the valve block.
Unfortunately the valve block can not be dismantled for inspection and cleaning thus a new Level Control Valve Unit (Y36/6) was required.
As a comparison, after replacing the Level Control Valve Unit (Y36/6) or Valve Block with a BRAND NEW OEM part, the following result was obtained for a leak test.
- After all valve block valves were closed the compressor produced 10.8431 bar within 10 secs which is withing the specification of 10 bar within 40 secs.
- After the compressor was turned off the initial compressor pressure ('P' line) = 10.8431 bar.
- After the 120 elapsed time the final compressor pressure ('P' line) = 10.8431 bar.
- Thus the measured leakage rate was 0.0 bar in 120 secs which is INSIDE the specified 0.5 bar in 120 secs.
2. Leak test between valve block and central reservoir.
As another example the following result was obtained for a leak test between valve block (Level Control Valve Unit (Y36/6)) and central reservoir for a FAULTY Level Control Valve Unit (Y36/6) or Valve Block.
- Initial Central Reservoir pressure = 12.07 bar reached in 60 secs.
- After Compressor turned off the Central Reservoir pressure = 10.84 bar.
- After 120 secs elapsed time the Central Reservoir pressure = 10.57 bar.
- Conclusion: This real world Central Reservoir and its associated supply line after 220,000Km produced a leakage rate of 0.27 bar in 120 secs, which is well within the specified 0.5 bar in 120 secs.
As a comparison, after replacing the Level Control Valve Unit (Y36/6) or Valve Block with a BRAND NEW OEM part, the following result was obtained for a leak test between valve block (Level Control Valve Unit (Y36/6)) and central reservoir.
- Initial Central Reservoir pressure = 7.549 bar reached in 60 secs.
- After Compressor turned off the Central Reservoir pressure = 7.41177 bar.
- After 120 secs elapsed time the Central Reservoir pressure = 7.41177 bar.
- Conclusion: This real world Central Reservoir and its associated supply line to a brand new Level Control Valve Unit (Y36/6) or Valve Block produced a leakage rate of 0.0 bar in 120 secs, which is well within the specified 0.5 bar in 120 secs.
Replacing Compressor Unit
|
- If possible depressurise the AIRmatic system using STAR DAS.
- Disconnect battery.
- Remove engine compartment paneling (right front part only).
- Unscrew pressure line connection (1) from AIRmatic compressor unit (A9/1).
- Detach connector on AIRmatic pressure reduction valve (A9/1y1).
- Disconnect connector for air compressor motor (3).
- Pull intake hose with air filter (2) out of longitudinal member.
- If the AIRmatic air filter (2) is replaced, the arrow on the air filter (2) must point upwards.
- Unscrew nuts (arrows) and remove AIRmatic compressor unit (A9/1).
- Detach air compressor relay (K40/7kO). Only when installing a new air compressor. When replacing the air compressor the air compressor relay (K40/7kO) should always be exchanged as the switching contacts may be damaged.
- Install in the reverse order.
Compressor Unit Repair
If the compressor unit is not able to provide pressure, the most common fault is worn piston ring or cylinder head inside the air compressor. The piston ring within the compressor unit of your air suspension system deteriorates over time. The OEM piston ring is made from a soft plastic that wears quickly, this wear substantially reduces the output of your compressor leading to noisy, slow rising or non-rising suspension. There are available piston rings with improved design.
Few notes to take into account:
- The replacement of piston ring will not help if the cylinder head is damaged/worn. Inspect head for damage and clean it from dust. There are also compressor repair kits that include new cylinder head.
- It is not uncommon for the torx bolts attaching piston head to the compressor to break. Make sure to order spare bolts with the kit and be prepared to drill out the old remains.
- While at it, don't forget to replace air dryer desiccant (silica gel) and dust filter.
Valve Block Repair
The most common faults and diagnosis:
- Fault in electrical solenoid valve. Can be tested by supplying 12v voltage to the pins of electrical connector. In case of failure the repair is not possible (all valve solenoids are part of one big monolith).
- Due to oxidation process the valve block separates and lets the air through (see picture below). Possible to clean the oxidation layer and reattach the halves.
- Valves do not close tight, letting the air through. Oxidation layer can be cleaned with some reagent. O-rings can be changed (see below).
- Bad pressure sensor (usually misdiagnosed). Pressure sensor can be replaced separately.
- Rusty or broken electrical contact pins of pressure sensor or valve control.
![]() |
![]() |
![]() |
O-ring repair kit
There are sellers on eBay who sell valve block O-ring repair kit with set of 18 O-rings (~30 EUR).
Instructions:
- Two mounting assemblies need to be removed to open the valve block casing. The removal of those two mounting bolts may require some PB Blaster penetrating fluid, as the blocks can have very heavy corrosion on those mounting bolts.
- There are also two lugs on each side used to hold the Solenoid Pack / Cover in place.
- Use four small electrical screwdrivers or wooden or plastic wedges to hold the plastic solenoid pack's lugs up.
- Douse with the whole assembly with WD40 or similar and wriggle, wriggle and wriggle until the two halves of the valve block come free.
- When reassembling the two halves of the valve block, add only the smaller o-rings to the solenoid posts, and put the larger o-rings into the recesses on the underside of the metal block and ensure they are well seated. This helps with reassembly to ensure the larger solenoid o-rings do not get damaged or misaligned when putting back together. You may find the larger o-rings getting nipped/cut if reassembled with them on the posts.
- On the underside of the metal block around the ports which the solenoid pins engage, there are some very small slots which marry up with some very small plastic moldings on the solenoid block. Ensure these slots are cleaned of any deposits. You can use a pin and a razor blade to tease out the deposits. Doing this will help ensure a nice snug fit when putting back together.
- Use a dielectric grease sparingly on the o-rings.
- Ensure all deposits are cleared off, and use an airline to blow through all the passages.
- You may need to use a vice carefully to press the solenoid block and metal block back together. Ensure the plastic cover clips well over the metal lugs on the metal block.
![]() |
![]() |
![]() |
Line Repair
For the location and routing of the AIRmatic air lines see above.
If you have diagnosed a leak in any of the AIRmatic pneumatic lines, the repair options are to:
- Cut out the failed section and reconnect using an in-line joiner.
- Replace the failed section of air line with a M-B repair kit (5 ft length only available).
- Replace the complete air line with an aftermarket high pressure flexible nylon pneumatic line.
- Bypass the complete air line with an aftermarket high pressure flexible nylon pneumatic line.
The air lines to the rear struts go through the interior and it may be difficult to find the leak unless the crack is large enough so that the crack can be located thanks to a loud hissing sound. Alternative line can be run from front valve block to the rear to test if the line is faulty.
![]() |
![]() |
M-B sells the AIRmatic air line (pipe/hose/tube) in 5 ft lengths, maximum. From the factory, the air line is built using a continuous length of line with no joins. The M-B 5 ft lengths are just for repairs, so connectors will be needed.
![]() |
However, you can buy aftermarket 4x2.5mm nylon high pressure flexible pneumatic lines of any length which are much cheaper than OEM lines (search keyword "4mm Hose Flexible Nylon Natural / Tube Pneumatic Air Line / 5m Roll"). Various colours are available and can be used to match the OEM colour code.
M-B also sells an air line repair connector (junction/fitting) A0003270169 which can be used to re-connect an air line after cutting out the broken section. However, there are also available cheap and reliable plastic "push in" connectors which can be used to easily connect air lines without any tools.
Leaking Front Strut Air Spring - Repair Options
Leaking front strut air spring
Air spring of the front suspension strut is shown in the next figure. The lower flared conical part of the air spring protective boot/bellows (n) is the "air spring plunger". The plunger mates to the "support bushing/bearing" which is the conical shaped seat on the damper unit.
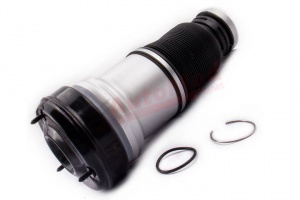
A common issue when a Front Suspension Strut deflates completely and the car is then jacked up so that the strut is fully extended is that the Air Spring Plunger separates from the Damper Support Bearing.
Note: Air suspension struts on which the Air Spring Plunger (7) is separated from the Support Bearing can sometimes be filled with air again without problems. They do not necessarily need to be exchanged for a new suspension strut. However the strut must be filled while the protective boot/bellows (n) is aligned to the Damper Support Bearing. The method is to pressurize the suspension strut using STAR Diagnosis and at the same time press the Air Spring protective boot/bellows upwards as far as it will go to remove any crinkles. Then pull it smoothly and evenly downwards and press onto the support bearing. No air must escape from the plunger to support bearing contact surface otherwise pressure can not be built up in the Air Spring.
For an AIRmatic strut to deflate completely there may be a catastrophic failure of some internal component such as the air bag/bladder (h), but it can also mean that the residual pressure holding valve (k) is leaking so that the strut deflates over time. This residual pressure holding valve (k) normally blocks off the pressure chamber in the air spring from the supply line and closes at or below a residual pressure of 4-5 bar. For a leaking residual pressure holding valve (k) to cause a full deflation, the air supply line or the relevant valve in the Level Control Valve Unit (Y36/6) would also need to be leaking.
A leaking Level Control Valve Unit (Y36/6) on its own should not cause the strut to deflate completely as the residual pressure holding valve (k) should be fully closed below 4-5 bar.
Leak test
Before replacing a supposed leaky AIRmatic strut, always carry out a leak test on the head bearing using soapy water. Proceed as follows:
- Fill the air spring (using the DAS or other means), and in the process pull the air spring plunger (7) downwards firmly by hand so that the air does not escape between the air spring plunger and the Damper support bearing (picture 2 and 3).
- Once the suspension strut is filled, carry out the leak test on the head bearing and repair if necessary. A repair kit is available for this purpose.
- After using the repair kit proceed as described above when filling the air suspension strut (picture 2 and 3) ie pull the air spring plunger (7) firmly downwards by hand so that the air does not escape between the air spring plunger and the support bearing.
Repair options
If the head bearing is not leaking and the plunger is fully seated on the support bearing then the options are to;
- Replace the complete AIRmatic strut.
- Replace just the Air Spring of the AIRmatic Suspension Strut. (Note: This is the cheaper option but requires dismantling the failed Suspension Strut. It is a good option if the damper unit is in good condition. Refurbished Air Springs are available from Suspension Workshops.
Remove/install front suspension strut
If a replacement front axle spring strut (40) has been procured, it is quite an easy task to swap them over.
- Position wheels straight ahead
- Jack up the rear or just one side of the car as required. Support the car on stands.
- Remove f32/40A (AIRmatic compressor fuse) from the relay box in engine compartment right. This is not strictly necessary, as the compressor should not engage if engine is not running.
- Empty suspension strut (40) affected using DAS. (Note: it is not strictly necessary to do this step - just be careful when opening the pressure line to release any residual air slowly.)
- Unscrew pressure line connection (40a). Remove the pressure airline from the head of the strut using 10mm open ended spanner. Residual pressure in suspension strut up to 3.5 bar. Plug the pressure line for the duration of the repair operations. Installation: Check pressure line O-ring and replace if necessary.
- Unscrew nuts (40b) on front end. Remove the three upper mounting nuts (13mm) at the strut head. Installation: Fit nuts (40b) then refill suspension strut in fully-assembled vehicle before torquing to specification (lightly tighten the three strut upper mounting nuts - they will be torqued fully once the car is ready to drive).
- Disconnect left front axle multiple circuit junction connector, major assembly compartment (X62/7) right front axle multiple circuit junction connector, major assembly compartment (X62/6). Connectors of damping valve unit and rpm sensor. Press against spring (arrow) to remove. (Note: WIS says to press down on the spring retaining clip to release the multi-electrical connectors.) If necessary the multi-electrical plugs X62/6 or X62/7 can be released by praising the spring retaining clip upwards. Separate the front strut multi electrical connector into two connectors thus releasing the front strut so that it can be removed.
- Remove bolts (40c) from spring strut (40). Installation: After installing, the bolts (40c) must close at least flush with the suspension strut (40) or be seated slightly lower in it.
Note: The AIRmatic front strut is attached to the ball joint of the lower suspension arm with two stub screws (5mm hex Allen key screws) on the bottom of the spring strut.
- If required, apply heat to the bottom allen stub screws. Several people have reported difficult screw removal resulting in several broken hex wrenches, frustration or even stripped set screws that had to be drilled out. A very effective method to remove the screws is to use heat from a blow torch. A micro torch provides a nice small sharp flame that is easily controlled as to not cause any collateral damage.
- Loosen the two bottom allen stub screws (5mm hex Allen key). Do not fully remove the stub screws, just unscrew them so that about five threads are showing.
- Loctite can be added to the exposed threads before installation. Note: It is very easy to strip the thread when starting the stub screws in dirty holes on an old damper unit. Not completely removing the stub screws during disassembly eliminates this problem. If a stub screw mangles the start of a thread, remove the Air Strut to a work bench and thoroughly clean the threads on both holes. They will be full of old Loctite sealer. Then screw a stub screw into the 'good' side and keep screwing it all the way through until it comes out the far side, and in the process reshaping the mangled thread. Do this a couple of times and the stub screw should then start properly. It is far easier to start the stub screws on a work bench than when in the car.
- Slacken suspension strut (40) on ball joint of spring control arm (17) using a suitable lever. Check cup seal of ball joint in spring control arm (17) for damage.
Undo the upper control arm ball joint nut (17mm) until it reaches the end of its thread and leave in place to protect the thread.
Use a ball joint separator tool to remove the upper control arm ball joint.
Ball joint separator tool.
- Remove spring strut (40) downwards towards the side. Installation: When installing tighten the upper nuts (40b) first.
- Fill suspension struts (40) in question using DAS. Pressurize to 5 bar. During filling the wheels must not contact the ground, as when filling in the deflected condition the air spring bellows in the suspension strut (40) is destroyed. In other words: Never completely lower the vehicle if the air shocks are not pressurized. Lower the jack partly until the car is at normal vehicle height (lower vehicle until distance axle center to lower edge of fender is about 400mm). Start the engine and wait for at least two minutes for everything to stabilize.
- Check AIRmatic for leaks.
- Install in the reverse order
Torque specifications:
- Nut, front suspension strut to front end: 20 Nm
- Bolt, front suspension strut to spring control arm: 20 Nm
- Air suspension pressure line to front suspension strut: 5 Nm
Tutorials
Excellent replacement tutorials for the front struts are available here:
Remove/install rear suspension strut
Replacing rear strut is more time consuming than replacing front strut.
![]() |
|
Removal:
- Depressurize suspension strut concerned (41) using DAS. (Note: it is not strictly necessary to do this step - just be careful when opening the pressure line to release any residual air slowly.)
- Remove f32/40A (AIRmatic compressor fuse) from the relay box in engine compartment right. This is not strictly necessary, as the compressor should not engage if engine is not running.
- Jack up one side of the car as required. Support the car on stands.
- Remove rear wheel.
- Remove cover (arrow) in parcel shelf. To avoid damage to the trim on the C-pillar it is best to remove it as it certainly will be damaged (bruised/compressed and possibly dirtied) if not removed. To remove C-pillar unscrew T30 bolt under SRS tab and pull it off.
- Unscrew pressure line connection (41a) using 10mm open ended spanner. Be warned: pressure in the line between the valve block and the suspension strut can be very high so if pressure has not been released using DAS, slowly unscrew the valve allowing the residual pressure to escape. (The residual pressure valve on the top of the strut prevents the release of the last bit of pressure. Residual pressure in suspension strut is up to 3.5 bar. This means that the strut will still exert considerable force on the suspension components.)
- Plug the pressure line for the duration of the repair operations (just to make sure that dirt does not get in).
- Unscrew nuts (41b) using the smallest 13mm socket and driver available.
- Pull off grommet and disconnect electrical connector of damping valve unit (Y53x1/ Y54x1)
- Remove bolts (or plastic rivets) (72d) on spring control arm cover (72c). Remove spring control arm cover (72c).
- Detach brake caliper from the wheel. Disconnect brake wear sensor and remove brake wear sensor bracket (right side only). The removal of brake caliper is not strictly necessary if vehicle is lifted high and hence there is enough space to pull out the strut downwards.
- Remove stabilizer bar link bottom nut using 16mm socket and 22mm wrench. Detach the bottom part of the stabilizer bar.
- Remove bolted connection (2) of suspension strut (41) on spring control arm (72) using 21mm socket from both sides. The residual pressure in the strut will prevent the bolt from being removed. Use unscrewing (instead of pulling) to remove the bolt.
- Remove bolted connection (1) of thrust arm (4) on rear axle carrier. In practice, this step is not necessary as even without loosening this bolt the string control arm should easily swing out of the way for the strut removal.
- Remove bolted connection of spring control arm (72) on rear wheel carrier (using 21mm socket from one side and Torx E18 socket from the other). The residual pressure in the strut will prevent the bolt from being removed. Use unscrewing (instead of pulling) to remove the bolt.
- Pull down track control arm (72) and remove strut assembly (41) by lowering it and pulling it out to the side.
Installation:
- Install strut by loosely fitting nuts (41b). (The vehicle must be in the ready to drive mode when torquing these three nuts.)
- Install bolted connection (2) of suspension strut (41) on spring control arm (72). (The vehicle must be in the ready to drive mode when torquing this bolt.)
- Install bolted connection (1) of thrust arm (4) on rear axle carrier (if this bolt was loosened or removed). (The vehicle must be in the ready to drive mode when torquing this bolt.)
- Reattach stabilizer bar link bottom nut
- Install bolted connection of spring control arm (72) and wheel carrier by wriggling the wheel carrier (use a jack to raise spring control arm as needed). (The vehicle must be in the ready to drive mode when torquing this bolt.)
- Route strut's electrical line and reconnect connector of damping valve unit (Y53x1/ Y54x1)
- Attach spring control arm cover (72c)
- Reattach brake caliper (if was removed)
- Reattach wheel
- Screw pressure line connection (41a)
- Fill suspension struts affected using DAS. Pressurize to 5 bar. Warning: During recharging the wheels should never be in contact with the floor; refilling with the suspension compressed leads to destruction of the air suspension bellows in the strut (41). If DAS is not available, start the car and check that the strut gets pressurized. If the strut is not being pressurized, stop the car, lock, unlock and start the car again. Operate Level Control Switch (N72/1s2) to force strut height adjustment.
- Release the car from the jack slowly to check that the strut has enough pressure. Do not release the wheels fully before the struct has enough pressure.
- Check that the car is on the ground and the vehicle is fully supported on the new strut.
- Torque three fitting nuts (41b).
- Attach cover (arrow) in parcel shelf. Reattach C-pillar.
- Torque bolted connection (2) of suspension strut (41) on spring control arm (72)
- Torque bolted connection (1) of thrust arm (4) on rear axle carrier (if this bolt was loosened or removed)
- Torque bolted connection of spring control arm (72) and wheel carrier
- Check for leaks
Torque specifications:
- Suspension struts: Nut, rear suspension strut to body: 20 Nm
- Suspension struts: Air suspension pressure line to rear air spring: 5 Nm
- Suspension struts: Nut, rear strut to spring control arm: 110 Nm
- Spring control arm: Self-locking nut, to rear subframe: 50 Nm + 90 degrees
- Spring control arm: Self-locking nut, to rear axle carrier: 70 Nm
- Stabilizer bar link bottom nut: 40 Nm
Tutorials
Excellent replacement tutorials for the rear struts are available here:
Replacing the Air Spring in an AIRmatic Strut
As already described, a very common reason for a leaking strut is damage in the strut's rubber air bag/bladder (h). It is possible to purchase on eBay a refurbished front and rear air spring which is the top part of an air suspension strut for around EUR 120 and mount it to the original damper unit (the lower part of an air suspension strut). This requires the strut to be removed from the car and the air spring to be separated from the damper unit by partly dismantling the air spring. Note: Replacing only the strut's rubber air bag/bladder (h) of the air suspension strut is not suitable for a DIY project as it requires an hydraulic crimping tool.
Dismantling Front Air Spring
- Remove the complete front axle AIRmatic spring strut (40) from the vehicle.
- Remove the epoxy/mastic using a hammer and a screw driver. (TIP: If you are doing this with the strut still in the car, avoid getting pieces of epoxy/mastic in the engine.)
Removing top seal of front strut. Top seal removed. - Using a special tool (see below) unscrew the residual pressure holding valve (k).
Tool to unscrew the residual pressure valve. Residual pressure holding valve (removed). - If required close the opening of the residual pressure holding valve (k) with a short bolt M8, so that no dirt can penetrate into the air suspension strut.
- Using a special tool (see below) fit the tool to the Strut. Tighten the central nut to the plate from the inside and this will wind down the bolt pushing the Air Spring top metal disc inwards slightly releasing the snap ring.
Strut top seal tool. Strut top seal tool. - Remove the snap ring. (TIP: Use a small screwdriver to help remove the circlip lock snap ring but make sure it does not cause any scratches and burrs, otherwise the sealing of the new lock ring may be compromised. Remove any sharp edges or burrs if required.) (Note: a new circlip lock snap ring is provided in the top seal kit, see below.)
- Remove the tool.
- Remove the top seal metal disc cover with its 'O' ring. (Note: Run a small screwdriver around the edge of the disc and then keep manipulating the disc until it starts to come free. Use a small screw driver to lever the disc out. A very strong magnet can help.) (Note: a new top seal metal disc cover and a new 'O' ring are provided in the top seal kit, see below. A new top seal metal disc cover and a new 'O' ring are often provided with a new/refurbished air spring.)
Snap ring. Metal disc cover. Outside view of metal disc (A2203280621). Inside view of metal disc (A2203280621). - Inspect the inside of the top of the Front Strut for any sharp edges or burrs and remove if required.
- Drill a 4mm hole and if necessary insert a screw or similar device part way into the nylon plug which can then be pulled out. (Note: a new nylon plug is available with part number TBD.)
Strut after removing metal disc. Plastic plug removed. Nylon cover. Strut after removing plastic nylon plug. - Use an air impact driver to undo the lock nut on the top of the damper piston rod (e). (Note: unfortunately it is essential to use an impact wrench as the piston rod in the damper unit can not be restrained from turning. The impact wrench shocks the nut undone.)
- Remove the complete air spring from the damper unit.
Strut spring separated from damper unit. - From the inside of the Air Spring use a long piece of rod or tubing to press out the upper mount rubber bush.
Outside view of the strut with bush removed. Inside view of the strut with bush removed. - The yellow arrow points to the hole going through the upper mount rubber bush for the damper piston rod (e).
- The blue arrow points to the inside of the Air Spring for the rubber air bellows (h).
- The red circle shows the threaded brass air inlet to the Air Spring.
Reassembly Front Air Suspension Strut (40)
- Fasten the air bag/bladder (h) to the strut top using the 1st crimp ring.
- Install the strut tube (a) into the air bag/bladder and secure with the 2nd crimp ring.
- The next Figure shows the rubber air bag/bladder which is mounted on the outside of the strut tube (a) and is held in place by metal crimp rings.
- Notes:
- The bottom end or plunger of the lower strut tube (a) is tapered which is for sealing to the support bearing on the damper unit.
- Note: the Airmatic strut can leak air from the bottom of the lower section if not seated against the rubber of the damper unit correctly.
- Check the Seal between the damper and the air spring.
- Install top alloy dust cover.
- Install the protective boot/bellows to the top dust seal alloy cover.
- Thoroughly clean the damper unit before it is fitted into the air spring.
- The next Figure shows a close-up of the strut damper with the bump stop buffer (i) and bump stop cover. The damper is fitted after the air spring has been assembled. It slides through the strut top and then has the upper mount rubber bush and nut fitted followed by the nylon cover and then the top metal disc cover and lock ring. Note the large conical rubber support bearing which provides the air spring to damper seal.
- Prepare the strut top plate to take the Damper Unit.
- The next three figures show;
- (left image) the strut top plate with the hole for the damper,
- (center image) the strut top plate with the upper mount rubber bush in place waiting for the nyloc nut, (Note: an impact wrench is used to tighten the nut (with Loctite applied) to the damper piston rod.)
- (right image) the strut top with the nylon cover placed over the nut.
- The next three figures show;
- The next two figures show the metal disc cover with the 'O' ring installed (TIP: use silicon grease to ensure it is leak free) and the lock ring ready to be fitted using the strut top seal tool.
- Install the residual pressure holding valve (k) using the commercial tool or DIY modified spanner.
- Support the strut vertically and fill the top of the strut with a black butyl mastic to reduce vibration damage to the air inlet valve.
- TIP: If a pour-able butyl mastic can not be sourced, Sika manufacture a range of butyl mastic sealers which can be extruded in thin layers (5mm thick). Use a spatula to smooth the layer evenly and then leave it to set. Repeat the layering process until the cavity is filled. The result is not as neat as the OEM but it does the job. If required the extruded layers technique can be done with the Air Strut installed in the car as the compound is quite viscous and will not run.
Tools Required for Replacing Air Spring in Front Air Suspension Strut (40)
- AIRmatic residual pressure holding valve tool. Used to remove and install the brass residual pressure holding valves at each of the air inlets to the front air suspension struts. DIY tool can be made by modifying either a ½” or 3/8" spanner by grinding it down to fit the residual pressure holding valve.
Commercial 1/4" drive tool. 1/2" spanner. DIY residual pressure tool. Critical dimensions of the residual pressure holding valve.
- DIY home-made strut top seal tool can be made from a 150mm x 150mm piece of 6mm (1/4") steel plate.
mark-up dimensions for the DIY front strut top seal remover tool. Parts for DIY strut top seal tool. - Accurately mark up the steel plate as per the figure above which shows the mark-up dimensions for the DIY AIRmatic front strut top seal remover tool.
- Draw the two diagonals to establish the centre of the plate.
- Mark with a centre pop.
- Set a divider to 61.5mm radius.
- Draw a circle with the divider around the centre pop producing the pitch circle diameter of 123mm.
- Centre pop the first hole on one of the diagonals.
- Use the divider still set to a radius of 61.5mm and mark six arcs around the circumference of the PCD. This divides the PCD into six equal chords. (Alternatively set the divider to 106.5mm and scribe across the PCD in two places.)
- Centre pop the required intersections for the other two 8mm holes.
- Visually check that the centre pop marks match the pitch circle diameter (pcd) of the strut top plate mounting bolts.
- Drill the three off 8mm holes.
- Drill one 10mm hole in the center.
- Obtain three off 120mm long 8mm bolts for the three 8mm holes.
- Use three 8mm joiner nuts to attach the 8mm bolts to the strut top. (Alternatively four off 8mm nuts can be welded together to make one off 'long' nut.)
- Obtain one off 150mm long 10mm bolt for the center 10mm hole.
- Thread a nut right to the top of the 10mm bolt and add a flat washer with a little bit of grease.
- Accurately mark up the steel plate as per the figure above which shows the mark-up dimensions for the DIY AIRmatic front strut top seal remover tool.
- Impact driver (Note: is absolutely essential for removing the nut at the top of the damper unit.)
- Top seal repair kit. Includes: steel cap, brass valve and spring clip. Part number A2203202538 (~EUR 125).
Top seal repair kit (A2203202538).
Tutorials
Excellent replacement tutorials for the front and rear struts are available here:
Remove/install front axle level sensors
Remove/Install:
- Replace self-locking nuts and bolts
- Remove front wheels
- Disconnect connectors at front left and right level sensors (B22/8, B22/9)
- Unscrew nut (86c) on connecting rod (86) from front left and right level sensors (B22/8, B22/9)
- Unscrew nut (86b) on connecting rod (86) from upper wishbone (6) and remove connecting rod (86). Installation:Attach connecting rod (86) to the outermost hole (f) on the upper wishbone (6).
- Unscrew bolts (86d) on retaining plate (86a) and remove front left and right level sensors (B22/8, B22/9)
- Install in the reverse order
- After replacing the level sensors, calibrate vehicle level with Star Diagnosis (level calibration)
Torque specification:
- Nut, level sensor connecting rod to upper wishbone: 10 Nm
- Nut, connecting rod to level sensor: 5 Nm
- Bolt/nut of level sensor to retaining plate: 4 Nm
Remove/install rear axle level sensor
![]() |
|
Remove/Install:
- Replace self-locking nuts and bolts
- Disconnect plug from rear axle level sensor (B22/3)
- Unscrew nut (85e) of control rod (85) from stabilizer bar intermediate lever (81)
- Unscrew nut (85d) of control rod (85) at level sensor (B22/3) and remove control rod (85). Do not separate control rod (85) or change the adjustment.
- Remove bolts (85c) of retaining plate (85a) at level sensor (B22/3) and remove level sensor (B22/3)
- Install in the reverse order
- Calibrate vehicle level using Star Diagnosis after replacing the level sensor
Torque specification:
- Nut, level sensor link rod to torsion bar intermediate lever: 10 Nm
- Nut, control rod to level sensor: 5 Nm
- Bolt, level sensor to retaining plate: 4 Nm
- Nut, retaining plate to frame floor: 8 Nm
Airmatic Adjusting Levels Using STAR Diagnosis System (SDS) or Diagnosis Assistance System (DAS)
See Section Airmatic Adjusting Levels Using DAS